Example – Yaskawa MotionWorks IEC Toolboxes User Manual
Page 143
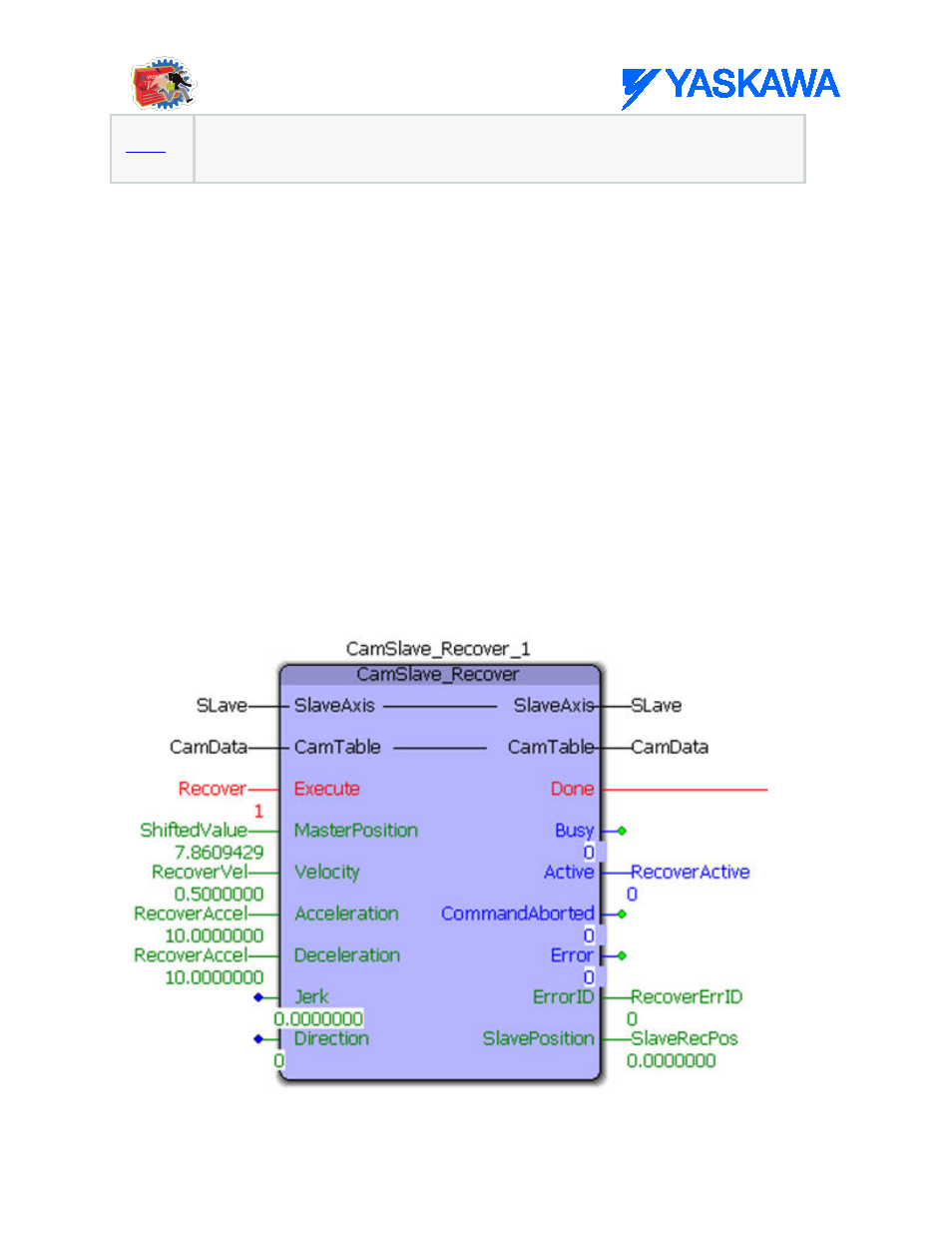
Cam Toolbox: Function Blocks
MotionWorks IEC61131-3 Toolboxes: 2013-09-13
130
The DataType connected to a function block parameter specified as ANY type does not
match the required data size. Right click on the function block and select “Object
Properties” to determine which parameters are ANY type.
Example
E-Stops can result in the instantaneous loss of control of the axes. Manually clearing debris or scrap from the
machine and adjustments after E-Stops and alarms can cause a change in motor position, all resulting in a de
synchronization of the master and slave.
The example given below illustrates how the CamSlave_Recover block can solve E-Stop recovery issues. The
logic analyzer plot shows the axes when the E-Stop occurred. At this point, the Y_CamIn outputs InSync and
Busy change to FALSE. A slight drift in the master axis position can be seen after the E-Stop. This can be due
to axis inertia, or because of adjustments made to the machine. The CamSlave_Recover block is executed to
physically move the slave to the position that corresponds to the master’s current position as determined by
looking in the CamTable.
The distance that the slave axis traverses in this process can be seen in the illustration. Once the
CamSlave_Recover is Done, the slave can be re-engaged with the master using Y_Camin.
Important: In this recovery condition, the ‘EngagePosition’ must be set to the master axis’ current position and
the EngageData.SlaveAbsolute=TRUE must be applied.