Torque prove – Rockwell Automation 21G PowerFlex 750-Series AC Drives Programming Manual User Manual
Page 461
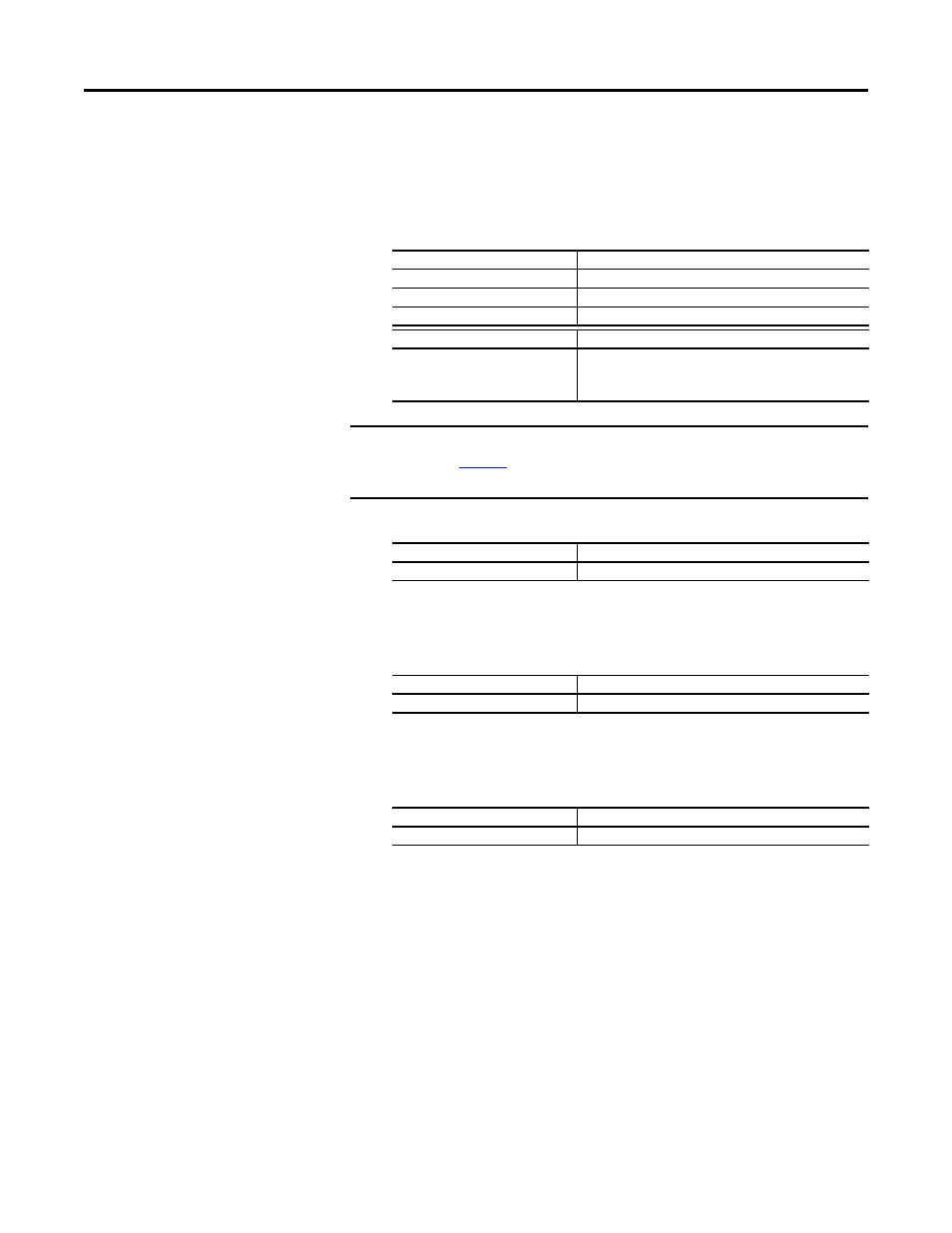
Rockwell Automation Publication 750-PM001J-EN-P - October 2014
461
Application Notes
Appendix B
Torque Prove
Carefully perform the following steps in the order presented.
1.
Enter Torque Prove parameter settings.
2.
Set speed deviation.
This setting can be lowered once the system has been tuned. The lower this
value, the faster the protection.
3.
Set speed deviation level.
This setting can be lowered once the system has been tuned. The lower this
value, the faster the protection.
4.
Set brake float tolerance.
Sets the level where the mechanical brake sets in encoderless mode.
I/O Module Parameter (Port X)
Setting
P10 [RO0 Sel]
0.00 (Disabled)
P6 [Dig Out Invert]
Bit 0 “Relay Out 0” = 1 (Output Inverted)
P10 [RO0 Sel]
Port 0, P1103 [Trq Prove Status], Bit 4 “Brake Set” = 1
Drive Parameter
Setting
P1100 [Trq Prove Cfg]
Bit 0 “TP Enable” = 1
Bit 1 “Encoderless” = 1
Bit 5 “BrkSlipEncls” = 1
IMPORTANT
After Torque Prove is activated, the drive is in an alarm state as described on
. Carefully read the Attention statement and acknowledge it by
setting the required parameter.
Drive Parameter
Setting
P1105 [Speed Dev Band]
10 Hz
Drive Parameter
Setting
P1106 [SpdBand Intgrtr]
0.200 Secs (Default)
Drive Parameter
Setting
P1111 [Float Tolerance]
2...3 times Slip Frequency of Motor.