9diagnostics & error management – Lenze 8400 StateLine User Manual
Page 441
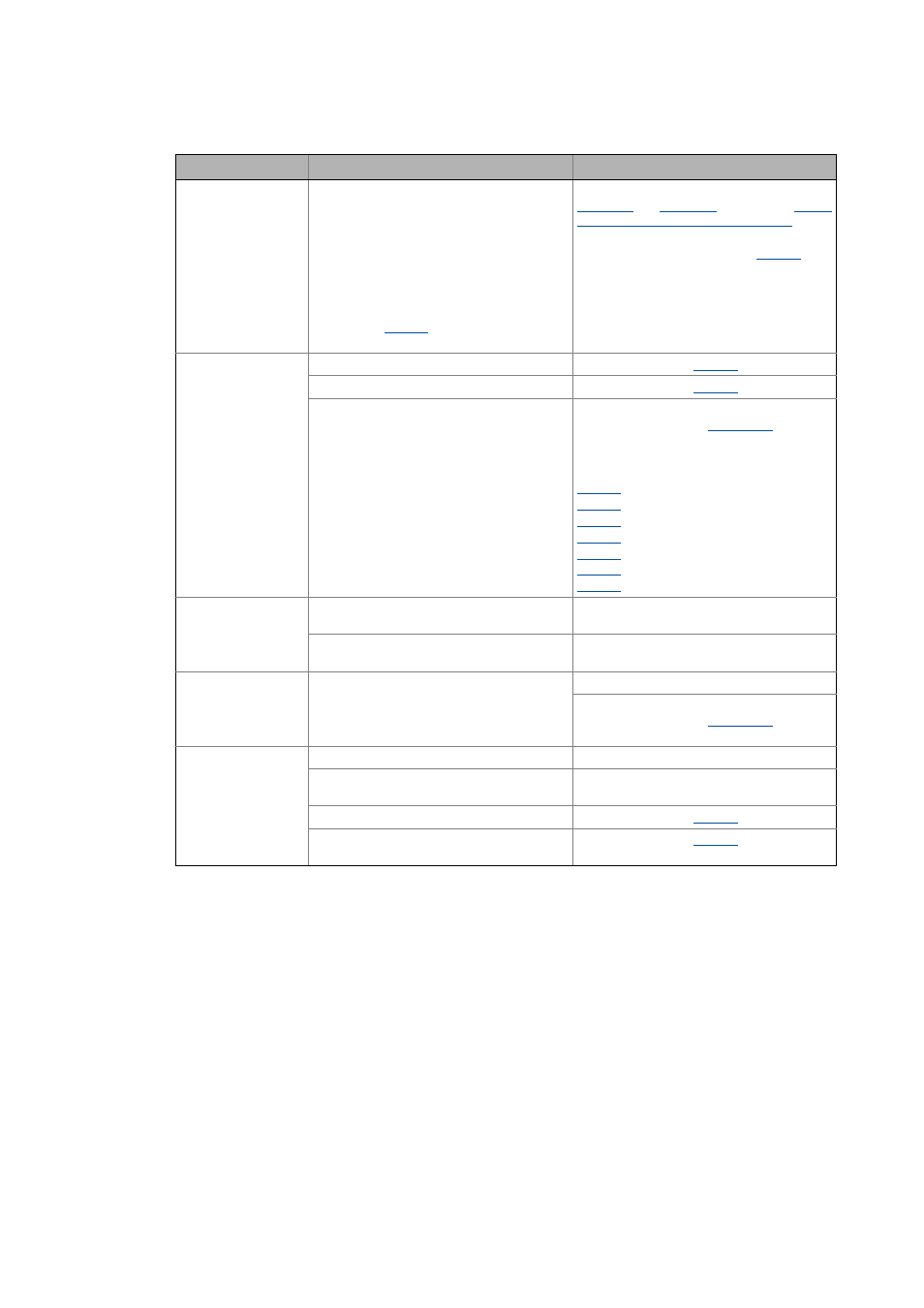
Lenze · 8400 StateLine · Reference manual · DMS 12.0 EN · 06/2014 · TD05/TD14
441
9
Diagnostics & error management
9.7
Maloperation of the drive
_ _ _ _ _ _ _ _ _ _ _ _ _ _ _ _ _ _ _ _ _ _ _ _ _ _ _ _ _ _ _ _ _ _ _ _ _ _ _ _ _ _ _ _ _ _ _ _ _ _ _ _ _ _ _ _ _ _ _ _ _ _ _ _
Motor rotates
regardless of setpoint
"0"
The setpoint is selected via the analog input
(blank where necessary).
The analog input has a tolerance of ± 1 % and
is designed as bipolar input unlike in the case
of the 8200 vector. For this reason, no dead
band has been set in the Lenze setting.
When a setpoint of 0.3 % has been selected,
e.g. a speed of 4.5 rpm (with reference speed
= 1500 rpm) is the result. As the auto-DCB
is set to 3 rpm. the
speed oscillates between 0 and 4 rpm.
Set dead band for the analog input in
(see chapter "
adaptation by means of characteristic
")
- or -
Increase auto-DCB threshold in
Motor consumes too
much current
V
min
boost has been selected too high
V/f base frequency has been selected too low Correct setting with
Rated motor data (stator resistance, speed,
current, frequency, voltage) and cos ϕ
and/or magnetising inductance is not
adapted to the motor data
Execute automatic motor parameter
identification with the
device
command
- or -
Adjust motor parameters manually:
: Motor stator resistance
: Rated motor speed
: Rated motor current
: Rated motor frequency
: Rated motor voltage
: Motor cosine phi
: Motor magnetising inductance
Motor parameter
identification is
aborted with error
LP1
Motor is too small compared to the rated
device power (>1 : 3)
Use device with lower rated power
DC injection brake (DCB) is active via
terminal
Deactivate DC injection brake
Drive behaviour with
vector control is not
satisfactory
different
Optimise or manually adapt vector control
Execute automatic motor parameter
identification with the
device
command
Torque dip in field
weakening range
or
motor stalling when
being operated in the
field weakening
range
Motor is overloaded
Check motor load
Motor windings are wired incorrectly
Reverse from star connection to delta
connection
V/f reference point is set too high
Override point of field weakening is set too
low
Maloperation
Cause
Remedy