3 using feed-forward control, 4 using proportional control – Yaskawa SGDB User Manual
Page 131
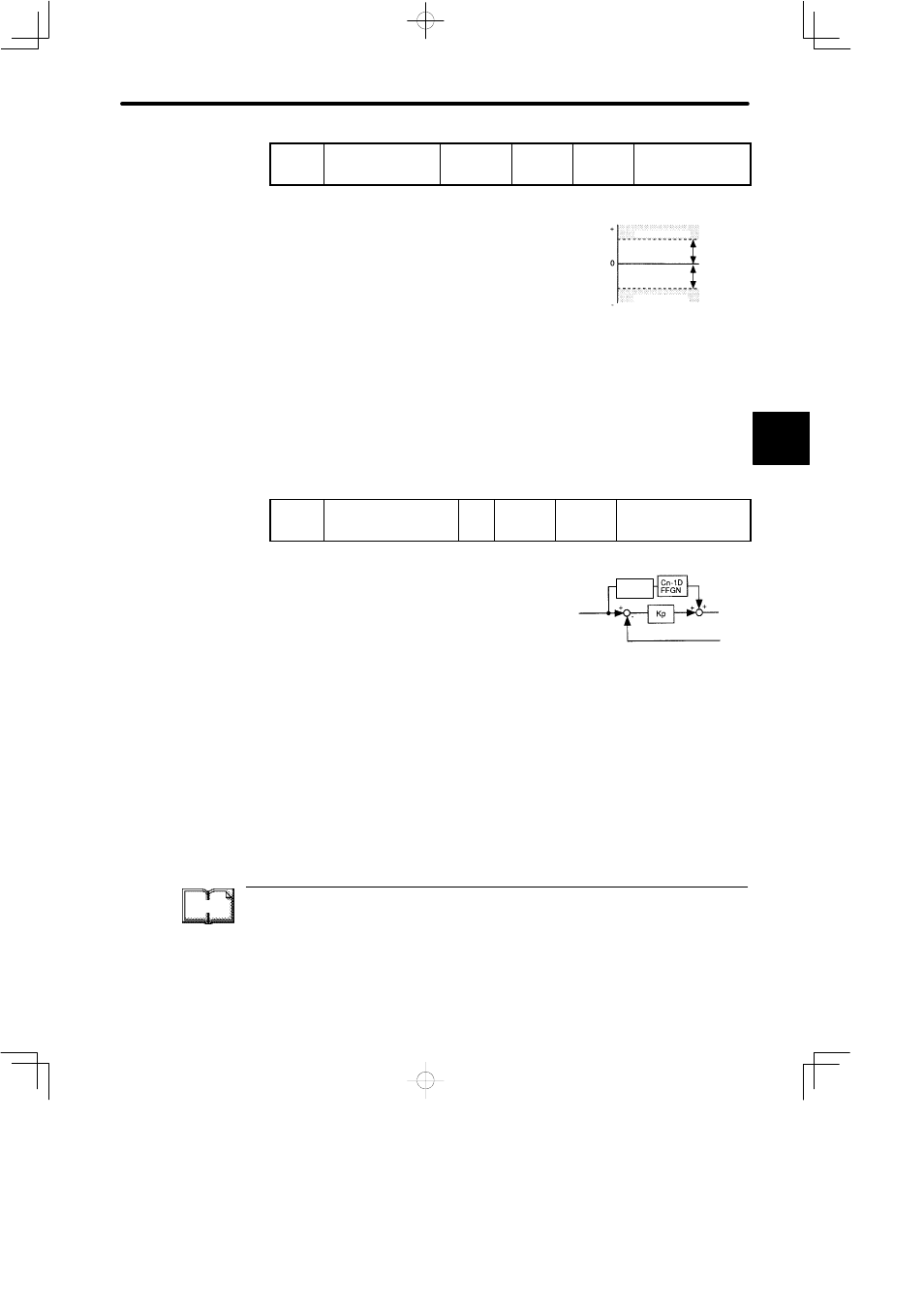
3.6 Minimizing Positioning Time
119
Cn-1E
OVERLV
Overflow
Unit: 256
References
Setting
Range: 1
to 32767
Factory
Setting:
1024
For Position Control
Only
Set in this parameter the error pulse level at which
a position error pulse overflow alarm (alarm A.31)
is detected.
If the machine permits only a small position loop
gain value to be set in Cn-1A, an overflow alarm
may arise during high-speed operation. In this
case, increase the value set in this parameter to
suppress alarm detection.
3.6.3 Using Feed-forward Control
Feed-forward control shortens positioning time. To use feed-forward control, set the follow-
ing parameter.
Cn-1D
FFGN
Feed-forward Gain
Unit:
%
Setting
Range: 0
to 100
Factory
Setting: 0
For Position Control
Only
This parameter is set to apply feed-forward fre-
quency compensation to position control inside
the SERVOPACK.
Use this parameter to shorten positioning time.
Too high a value may cause the machine to
vibrate. For ordinary machines, set 80% or less in
this constant.
3.6.4 Using Proportional Control
If parameter Cn-2B is set to 0 or 1 as shown below, input signal /P-CON serves as a PI/P
control changeover switch.
• PI Control: Proportional/Integral control
TERMS
Feed-forward control
Control for making necessary corrections beforehand to prevent the control system from
receiving the effects of disturbance.
Using feed-forward control increases effective servo gain, enhancing response perfor-
mance.
3
Normal control
Error pulse
Cn-1E
OVERLV
(Alarm A.31)
(Alarm A.31)
Reference
pulse
Differe
ntiation
Feedback pulse