4 using holding brake – Yaskawa SGDB User Manual
Page 120
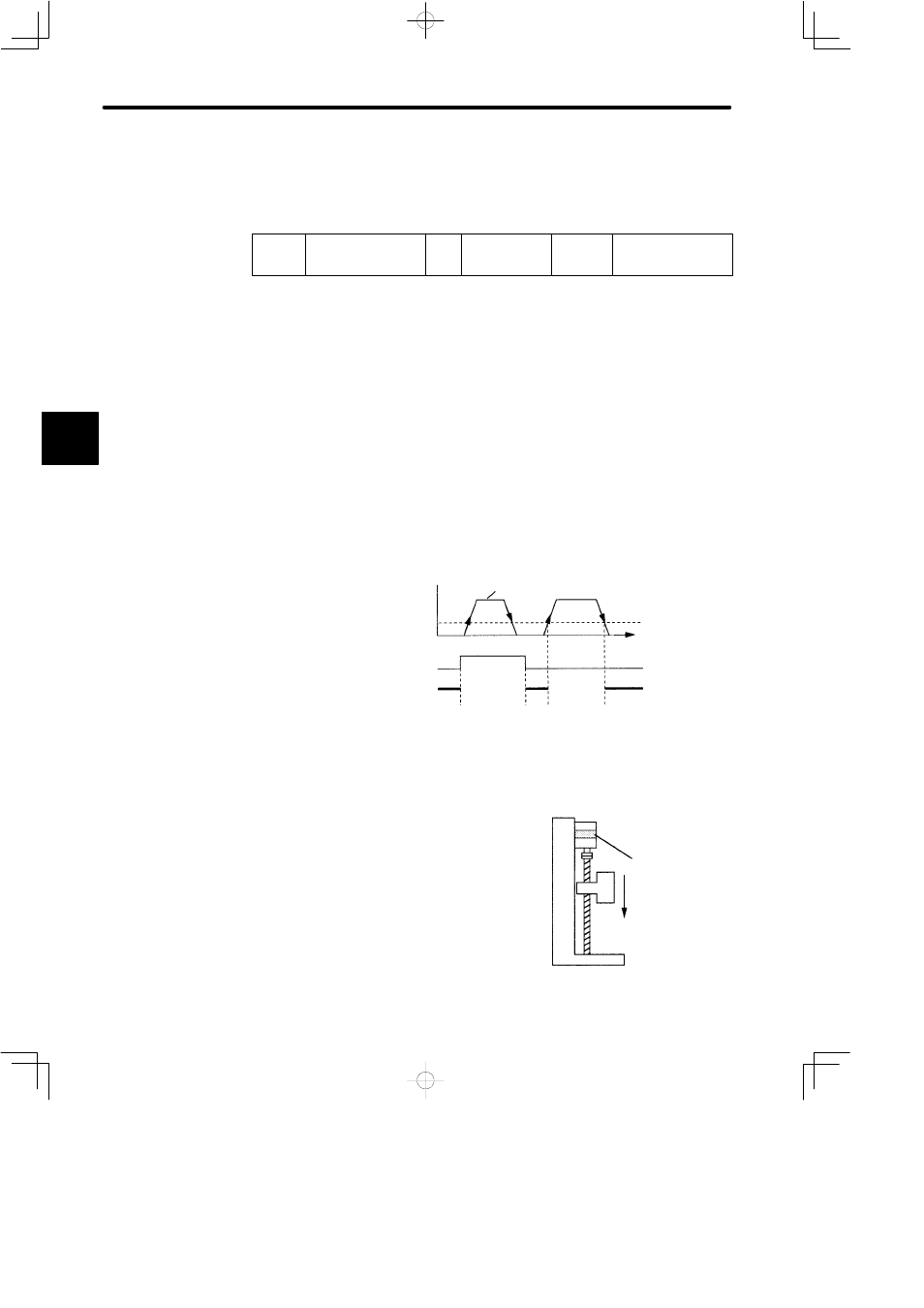
APPLICATIONS OF Σ-SERIES PRODUCTS
3.4.4 Using Holding Brake
108
J
Settings
Set in the following parameter the motor speed level at which zero-clamp is to be per-
formed:
Cn-29
ZCLVL
Zero-Clamp Level
Unit:
min
−1
Setting Range:
0 to 10000
Factory
Setting:
10
For Speed Control
Only
If zero-clamp speed control is selected, set the motor speed level at which zero-clamp is
to be performed. If a value higher than the maximum motor speed is set, the maximum
speed value is used.
Conditions for Zero-clamp
Zero-clamp is performed when all the following conditions are met:
• Zero-clamp speed control is selected (Parameter Cn-2B=10).
• /P-CON (1CN-41) is turned ON (0 V).
• Motor speed drops below the preset value.
Speed
V-REF speed reference
Preset value for
zero-clamp
/P-CON input
Zero-clamp being
performed
Open (OFF)
Closed (ON)
Time
3.4.4 Using Holding Brake
Holding brake is useful when a servo drive is used
to control a vertical axis. A servomotor with brake
prevents the movable part from dropping due to
gravitation when the system power is turned OFF.
3
Servomotor
Holding brake
Prevents movable
part from shifting
due to gravitation
when power is
turned OFF
- Tag Generator (30 pages)
- MP3300iec (82 pages)
- 1000 Hz High Frequency (18 pages)
- 1000 Series (7 pages)
- PS-A10LB (39 pages)
- iQpump Micro User Manual (300 pages)
- 1000 Series Drive Option - Digital Input (30 pages)
- 1000 Series Drive Option - CANopen (39 pages)
- 1000 Series Drive Option - Analog Monitor (27 pages)
- 1000 Series Drive Option - CANopen Technical Manual (37 pages)
- 1000 Series Drive Option - CC-Link (38 pages)
- 1000 Series Drive Option - CC-Link Technical Manual (36 pages)
- 1000 Series Drive Option - DeviceNet (37 pages)
- 1000 Series Drive Option - DeviceNet Technical Manual (81 pages)
- 1000 Series Drive Option - MECHATROLINK-II (32 pages)
- 1000 Series Drive Option - Digital Output (31 pages)
- 1000 Series Drive Option - MECHATROLINK-II Technical Manual (41 pages)
- 1000 Series Drive Option - Profibus-DP (35 pages)
- AC Drive 1000-Series Option PG-RT3 Motor (36 pages)
- Z1000U HVAC MATRIX Drive Quick Start (378 pages)
- 1000 Series Operator Mounting Kit NEMA Type 4X (20 pages)
- 1000 Series Drive Option - Profibus-DP Technical Manual (44 pages)
- CopyUnitManager (38 pages)
- 1000 Series Option - JVOP-182 Remote LED (58 pages)
- 1000 Series Option - PG-X3 Line Driver (31 pages)
- SI-EN3 Technical Manual (68 pages)
- JVOP-181 (22 pages)
- JVOP-181 USB Copy Unit (2 pages)
- SI-EN3 (54 pages)
- SI-ET3 (49 pages)
- MECHATROLINK-III (35 pages)
- EtherNet/IP (50 pages)
- SI-EM3 (51 pages)
- 1000-Series Option PG-E3 Motor Encoder Feedback (33 pages)
- 1000-Series Option SI-EP3 PROFINET (56 pages)
- PROFINET (62 pages)
- AC Drive 1000-Series Option PG-RT3 Motor (45 pages)
- SI-EP3 PROFINET Technical Manual (53 pages)
- A1000 Drive Option - BACnet MS/TP (48 pages)
- 120 Series I/O Modules (308 pages)
- A1000 12-Pulse (92 pages)
- A1000 Drive Software Technical Manual (16 pages)
- A1000 Quick Start (2 pages)
- JUNMA Series AC SERVOMOTOR (1 page)
- A1000 Option DI-101 120 Vac Digital Input Option (24 pages)