3 sl cycles (group i) – HEIDENHAIN TNC 407 (280 580) User Manual User Manual
Page 225
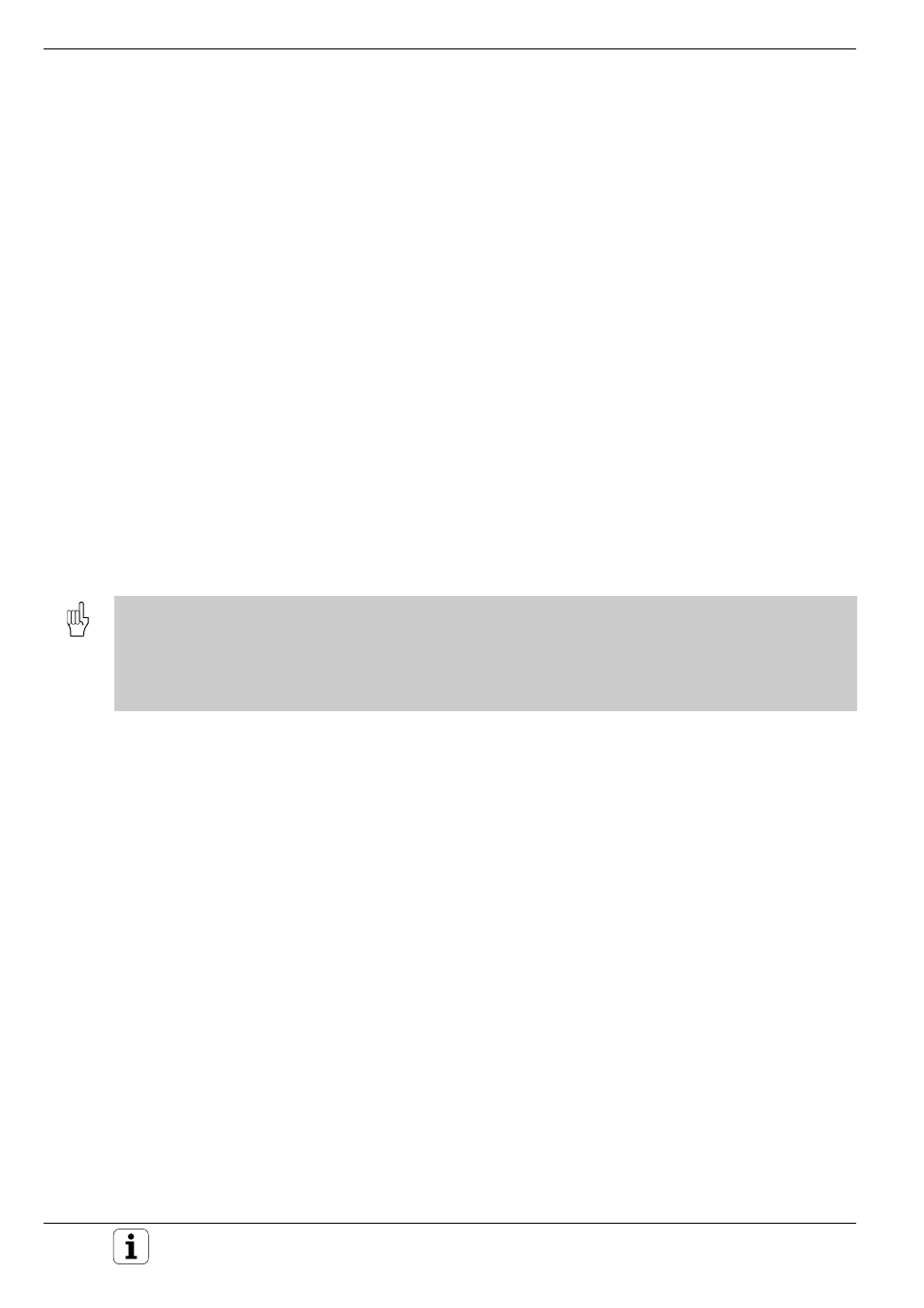
8-18
8
Cycles
TNC 407/TNC 415 B/TNC 425
8.3 SL Cycles (Group I)
SL cycles are highly efficient cycles that allow machining of any required
contour. SL cycles have the following characteristics:
• A contour can be composed of several overlapping subcontours.
Any islands or pockets can form a subcontour.
• The subcontours are defined in subprograms.
• The control automatically superimposes the subcontours and calculates
the points of intersection formed by overlapping.
The term SL cycles is derived from the characteristic Subcontour List of
cycle 14, CONTOUR GEOMETRY. Since this is purely a geometry cycle,
no intersection data or feed values are defined.
The machining data are specified in the following cycles:
• PILOT DRILLING (cycle 15)
• ROUGH-OUT (cycle 6)
• CONTOUR MILLING (cycle 16)
The SL cycles of group II offer further, contour-oriented machining proc-
esses and are described in the following section.
Each subprogram defines whether RL or RR radius compensation applies.
The sequence of points determines the direction of rotation in which the
contour is to be machined. The control deduces from these data whether
the specific subprogram describes a pocket or an island:
• The control recognizes a pocket if the tool path lies inside the contour,
• and an island if the tool path lies outside the contour.
• The machining of the SL contour is determined by MP 7420.
• Please be sure to run a graphic simulation before executing a program to see whether the contours were
correctly defined
• Memory is limited for SL cycles. In one SL cycle, for example, 128 straight line blocks can be programmed.
• All coordinate transformations are allowed in programming the subcontours.
• Any words starting with F or M in the subprograms for the subcontours are ignored.
For easier familiarization, the following examples begin with only the
rough-out cycle and then proceed progressively to the full range of
functions provided by this group of cycles.
Programming parallel axes
Machining operations can also be programmed in parallel axes as SL
cycles. (In this case, graphic simulation is not available). The parallel axes
must lie in the machining plane.
Input data
Parallel axes are programmed in the first coordinate block (positioning
block, CC block) of the first subprogram called in cycle 14 CONTOUR
GEOMETRY. Coordinate axes entered subsequently will be ignored.