IAI America ERC3 User Manual
Page 369
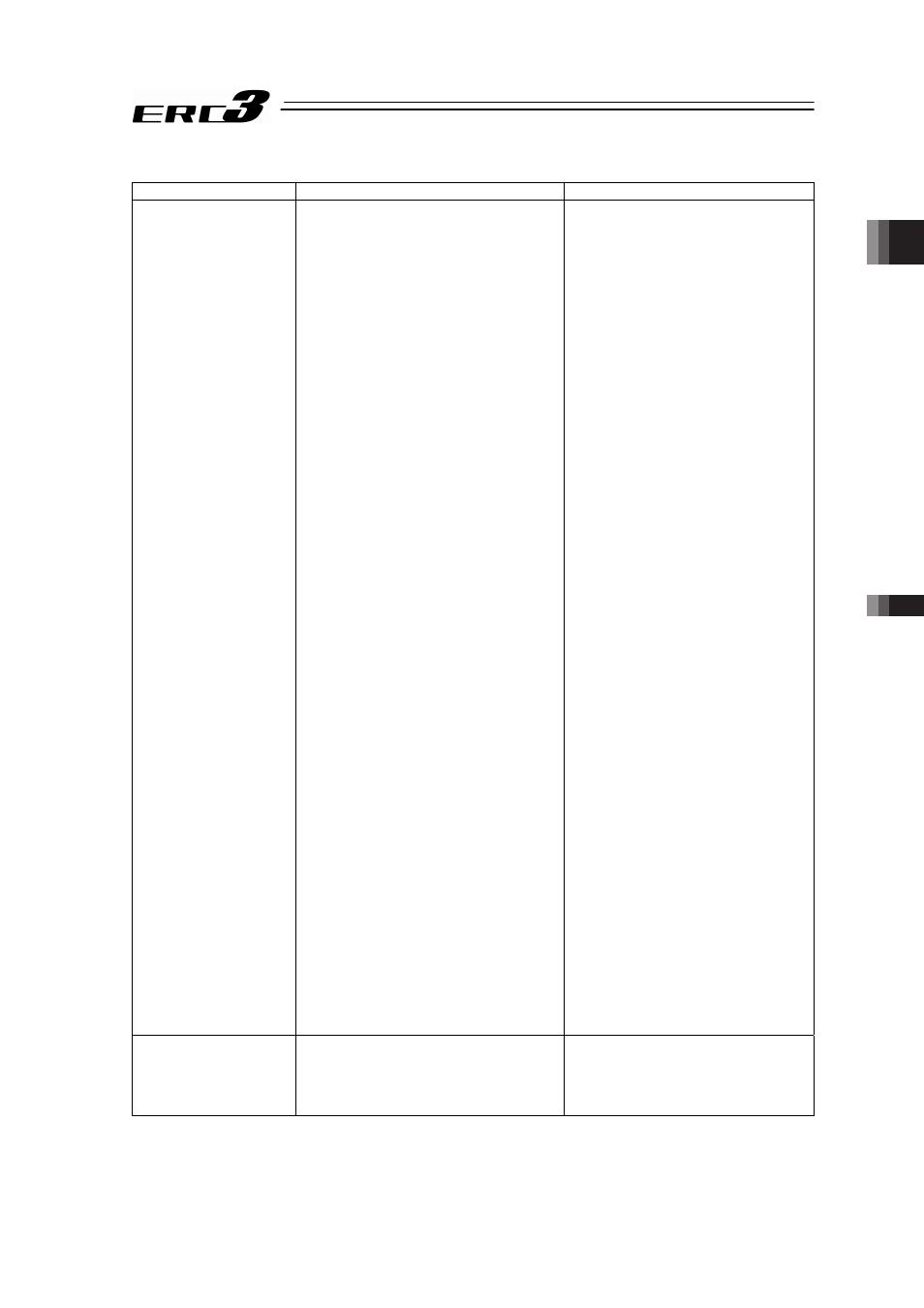
Chapter 7
Troubleshooting
7.2 Fault Diagnosis
359
[In the case of Pulse Train Control Mode]
Situation
Possible cause
Check/Treatment
The actuator does not
stop at the command
position.
PIO signal processing or parameter
setting is incorrect.
1) Incorrect electronic gear ratio
2) Acceleration/deceleration is set
incorrectly in the host controller.
3) Noise
4) The pulse-train type, a parameter, is
selected incorrectly.
5) The unit moving distance per pulse,
which is a setting condition of
electronic gear ratio, a parameter, is
too small.
1) Check the setting of electronic gear
ratio. The host controller also has
the electronic gear ratio parameter.
Set the electronic gear ratio not to
be inconsistent with that of the host
controller. In addition, reduce the
electronic gear ratio as much as
possible. If not, data overflow may
occur in arithmetic processing to
disable correct positioning.
[Refer to Chapter 4, 4.3 [3] (1)
Electrical Gear Setting.]
2) The actuator operates at the speed
and acceleration/deceleration
based on the frequency of input
pulses. Check if the
acceleration/deceleration set in the
host controller exceed the rating
acceleration/deceleration of the
actuator.
3) Noise can be misread as the pulse
if it jumps into the pulse train.
Take proper measures against
noise. [Refer to Chapter 2, 2.3.4
Noise Prevention and How to
Attach Electrical Devices.]
Check the cable connection
between the controller and AK-04 if
AK-04 is used.
• Cable length :
50mm or shorter recommended
(as short as possible)
• Shield treatment :
Use the shield treatment wire.
4) Check the pulse-train type.
[Refer to Chapter 4, 4.3 [3] (2)
Format Settings of Command
Pulse Train.]
5) Do not make the unit moving
distance less than the resolution of
the encoder. The actuator does not
move unless pulses by the
resolution of the encoder are input.
[Refer to Caution in Chapter 4, 4.3
[3] (1) Electronic Gear Setting]
(Note) In case of 2) or 3), the
actuator may not sometimes
operate.
You may not find case 4)
when the actuator is moved
for a long distance at a high
frequency.
The actuator does not
reach the command
position when operated
with extremely low
speed.
To avoid unnatural move, the actuator
would not move unless the differential
pulse becomes 3 pulses or more.
Set to the full-servo mode.
(Set Parameter No.53 Stop Mode initial
setting to 4.)