IAI America ERC3 User Manual
Page 220
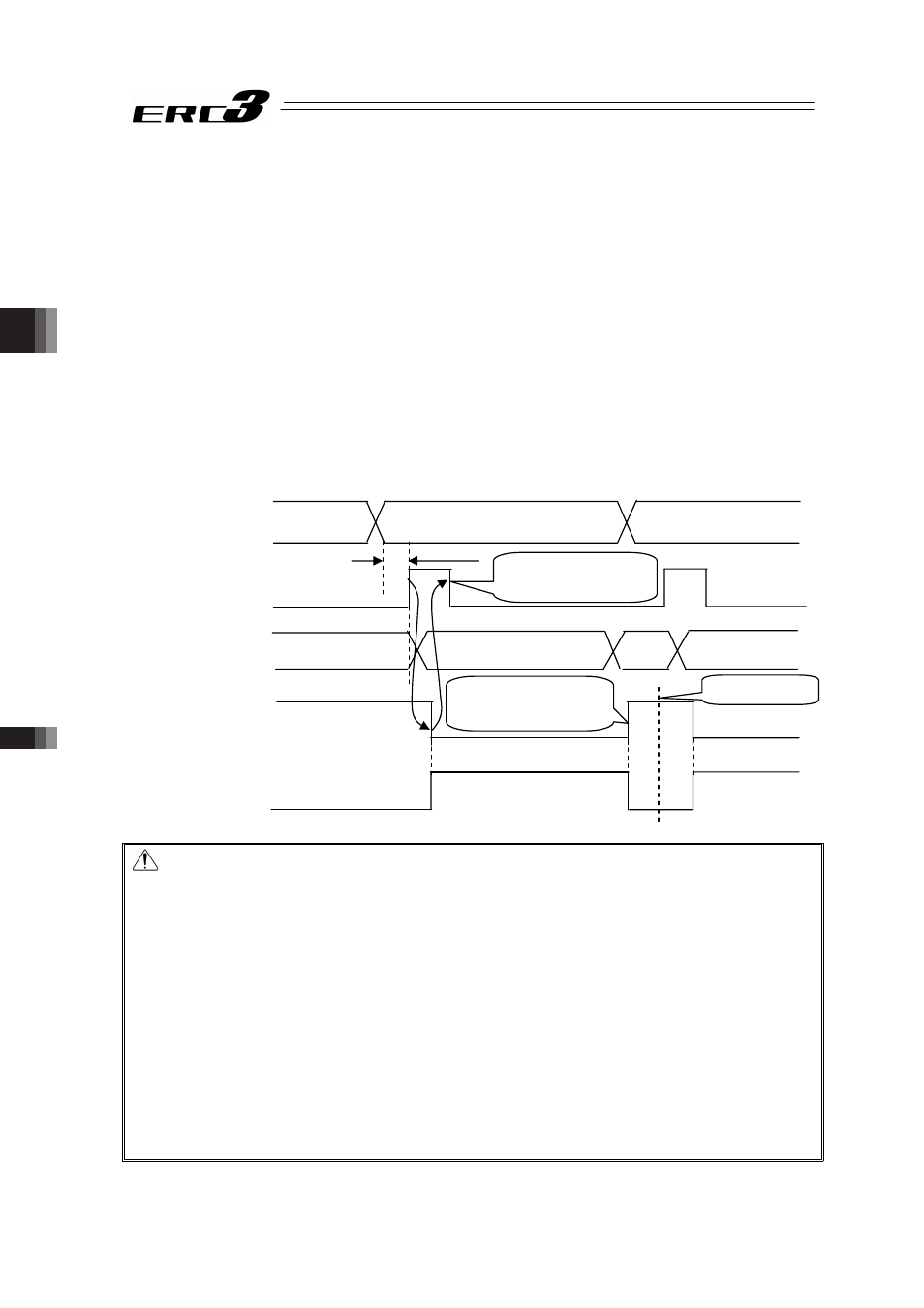
Chapter 4 Operation
4.2 Operation in Positioner Mode
4.2.3 Operation in Positioner Mode 2 (Operation Using PIO Converter)
210
Control method
1) First enter command position No. PC1 to PC** with binary data. Next turn start signal
CSTR ON. Then the actuator starts acceleration depending on the data in the specified
position table for positioning to the target position.
2) At operation start, positioning complete signal PEND is turned OFF. Always turn the CSTR
signal OFF. Without it, the completed position number is not output and the positioning
complete signal is not turned ON at the completion of positioning.
3) When the positioning is completed, the positioning complete position numbers are output
from complete position No.PM1 to PM** with binary data and also positioning complete
signal PEND is turned ON.
4) Moving signal MOVE is turned ON as soon as the operation is started and turned OFF at
the completion of positioning.
5) Positioning complete signal PEND is turned ON if the remaining moving distance enters
into the positioning width. PEND signal that is turned ON will remain ON unless the start
signal CSTR turns ON again, or the servo is turned OFF. It would not turn OFF even if it
goes out of the positioning width.
(Note 1)
Note 1 A switchover is available to INP (Setting 1) in Parameter No.39. PEND becomes an
in-position signal that turns OFF out of the positioning width.
Note 1 The completion position No. output is set to 0 during movement of the actuator.
Caution:
(1) Set the period taken from entering position No. to turning CSTR ON to 6ms or larger. In spite of
6ms timer process in the PLC, commands may be input to the controller concurrently to cause
positioning to another position. Take the scanning time in the PLC into account to set a period as
2 to 4 times as the scanning time. Set the value similarly if the PLC reads the complete position.
(2) At the completion of positioning, positioning complete signal PEND is not turned ON if start
signal CSTR remains ON. If this occurs, turn CSTR OFF then PEND is turned ON immediately.
Therefore, create the sequence program so that turning PEND OFF makes CSTR turned OFF
and the PLC waits for the state in which PEND is turned ON.
(3) At the positioning to the position same as that specified in the stop (complete) position number,
PEND is turned OFF once but moving signal MOVE is not turned ON.
Therefore, use PEND to turn CSTR OFF.
(4) MOVE turns ON at the start of an operation and PEND turns OFF at almost the same time.
MOVE turns OFF when there is no more movement command existing. Therefore, in the
normal stop, PEND turns ON after MOVE is turned OFF, however, when the positioning width
setting is wide, PEND would turn ON even during an operation of the actuator.
Command position No.
PC1 to PC**
(PLCĺController)
Completed position
PM1 to PM**
(ControllerĺPLC)
Start signal CSTR
(PLCĺController)
Positioning Completion Signal
PEND
(ControllerĺPLC)
Moving Signal MOVE
(ControllerĺPLC)
T1t6ms
PM1 to PM** = 0
(Note 1)
PM1 to PM** = 0
(Note 1)
Turned OFF by
turning PEND OFF
Turned ON after
entering into
positioning width zone
Target Position