3] list of pio signals – IAI America ERC3 User Manual
Page 113
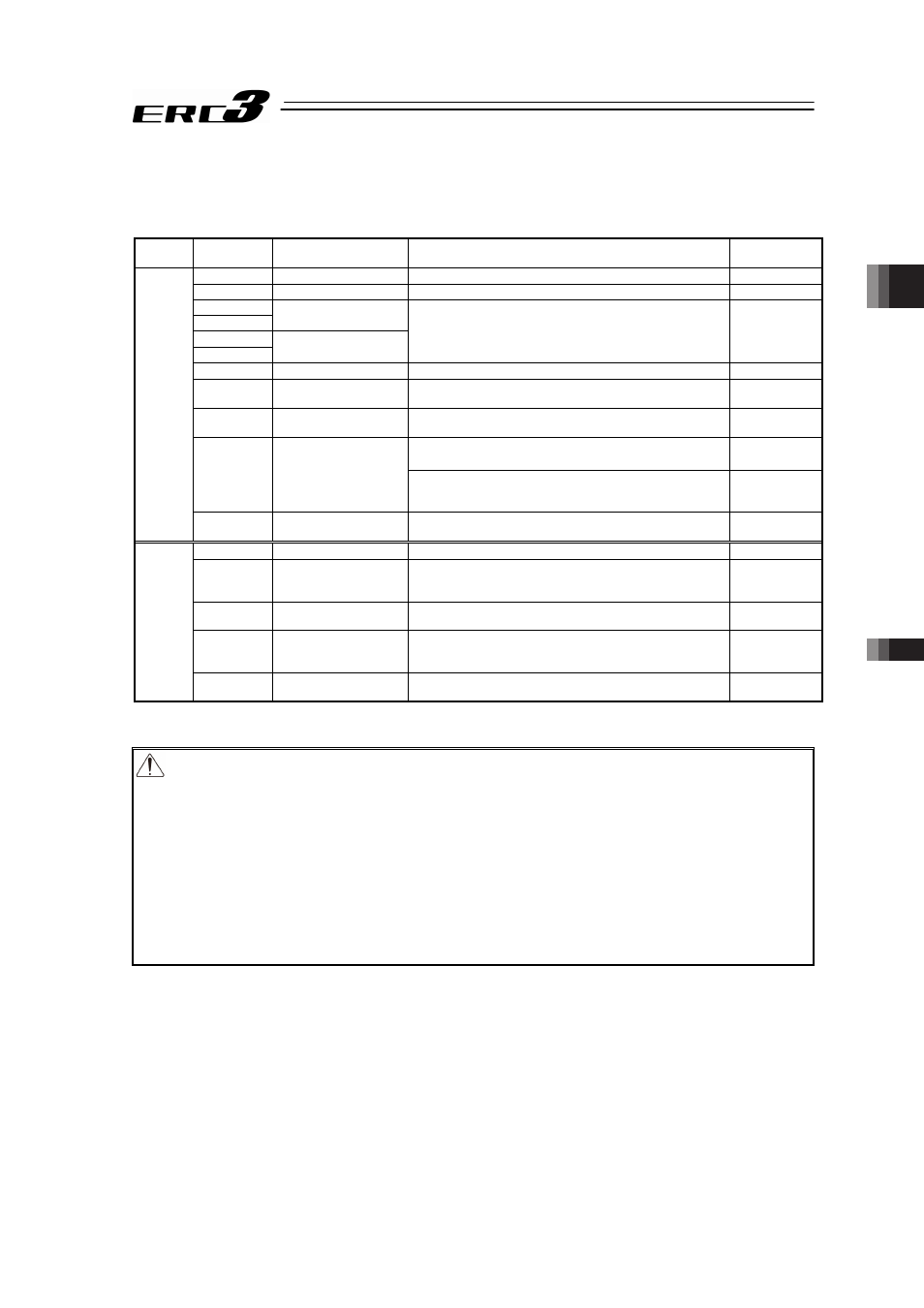
Chapter 3 Wiring
3.2 Pulse
Train Control Mode
103
[3] List of PIO Signals
The table below lists the functions of PIO signals. Refer to the section shown in Relevant
Sections for the details of the control of each signal.
Category
Signal
Abbreviation
Signal Name
Function Description
Relevant
Sections
EMG
Emergency Stop Input It shuts the motor power supply.
4.3 [3]
BK
Brake Forcible Release The brake will forcibly be released.
4.3 [4]
PP
/PP
Differential Pulse Train
Input (+)
NP
/NP
Differential Pulse Train
Input (-)
Input the pulse train from the host controller.
4.3 [7]
SON
Servo ON
Servo is ON while this signal is turned ON.
4.3 [6]
TL
Torque Limit Select
Applies torque limit to the motor with the signal on and the
value set to the parameter.
4.3 [7]
HOME
Home Return
The controller will perform home return operation when
this signal is turned ON.
4.3 [6]
When Parameter No. 25 = 0 (Positioning mode)
An alarm will be reset when this signal is turned ON.
4.3 [6]
RES
Reset
When Parameter No. 25 = 1 (Pressing mode)
Alarm reset is conducted with this signal being ON when
TL signal is not ON.
4.3 [6]
Input
DCLR
Deviation Counter Clear Have the deviation counter reset with this signal being
ON.
4.3 [7]
SV
Servo ON Status
This signal will remain ON while the servo is ON.
4.3 [6]
INP
Positioning Completion
It is turned ON when the remaining movement pulse
amount in the deviation counter is in the positioning width
range.
4.3 [6]
TLR
Torque Under Control Turns ON when torque reaches the limit while in torque
restriction (TL signal is ON).
4.3 [7]
HEND
Home Return
Completion
This signal will turn ON when home return has been
completed.
It will be kept ON unless the home position is lost.
4.3 [6]
Output
*ALM
Alarm
Turns ON when the controller is in normal condition, and
turns OFF when an alarm is generated.
4.3 [6]
Signal with “*” expresses the signal of active low. It is ON when the power is applied to the controller, and turns OFF when
the signal is output.
Caution: Torque restriction by TL Signal is available even if Parameter No.25 = 0. Thus, it is
possible to have a positioning move with the torque restricted in such cases as when
pushing out a breakable work piece. However, when it comes to a situation that the
actuator cannot move, it may create a big deviation (servo lag pulses) as it may
occur for the pressing control. If TL Signal is turned off under this condition, the
operation may be started with the maximum torque at the same time, and make a
sudden move. If it is not to be used, set User Parameter No.61 Torque Restriction
Command Input to invalid (= 1).
If Parameter No.25 = 0, the deviation counter cannot be cleared since there is no
DCLR Signal. Move to the opposite side or turn the servo OFF if a movement cannot
be made any more.