Chapter 3 wiring 3.7 wiring method – IAI America ERC3 User Manual
Page 155
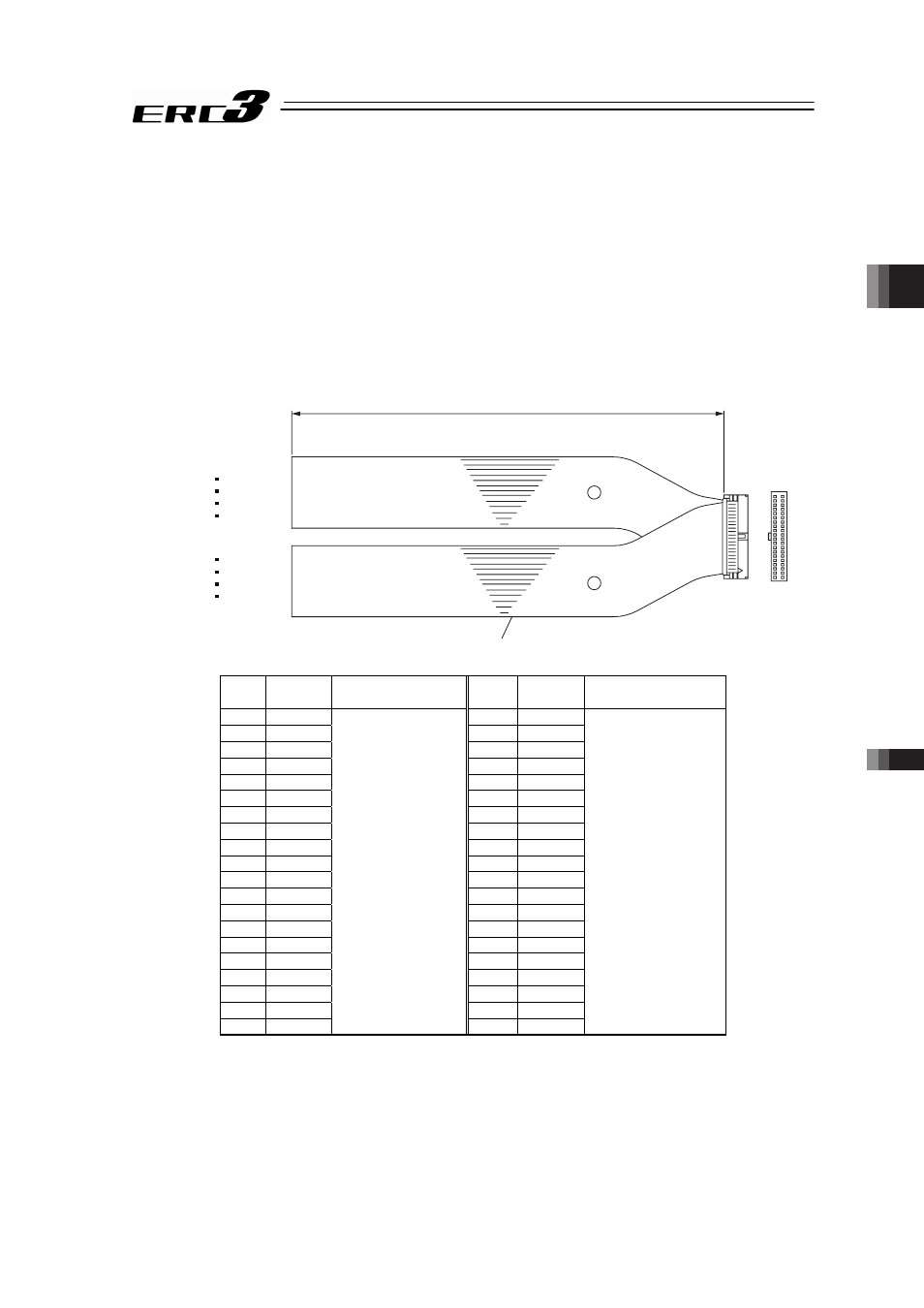
Chapter 3 Wiring
3.7 Wiring Method
145
3.7.3 Wiring between PIO Converter and Host Controller (e.g. PLC)
The connection of I/O for PIO Converter is to be conducted with the dedicated I/O cable. The
cable length is shown in the model code of PIO Converter. Check the model code of PIO
Converter. Selection can be made from 3m or 5m as well as standard 2m. 10m is also
applicable at maximum if purchased separately. [Refer to 1.1.5 How to read the model]
Also, the end of the cable harness to be connected to the host controller (PLC, etc.) is just cut
and no treatment is conducted so the wiring layout can be performed freely.
Model: CB-PAC-PIOƑƑƑ
(ƑƑƑ indicates the cable length L. Example 020 = 2m)
Flat Cable (20-core) × 2
BK-4 (20B)
BR-3 (1B)
BK-2 (20A)
BR-1 (1A)
20A
20B
1A
1B
Half Pitch MIL Socket
HIF6-40D-1.27R (Hirose Electric)
A
B
L
No treatment
conducted
No treatment
conducted
No.
Cable
Color
Wiring
No.
Cable
Color
Wiring
1A
BR-1
1B
BR-3
2A
RD-1
2B
RD-3
3A
OR-1
3B
OR-3
4A
YW-1
4B
YW-3
5A
GN-1
5B
GN-3
6A
BL-1
6B
BL-3
7A
PL-1
7B
PL-3
8A
GY-1
8B
GY-3
9A
WT-1
9B
WT-3
10A
BK-1
10B
BK-3
11A
BR-2
11B
BR-4
12A
RD-2
12B
RD-4
13A
OR-2
13B
OR-4
14A
YW-2
14B
YW-4
15A
GN-2
15B
GN-4
16A
BL-2
16B
BL-4
17A
PL-2
17B
PL-4
18A
GY-2
18B
GY-4
19A
WT-2
19B
WT-4
20A
BK-2
Flat Cable
٤
A
(Press Welding)
AWG28
20B
BK-4
Flat Cable
٤
B
(Press Welding)
AWG28
For the signal assignment of each wire, refer to the following considering the operation mode.
1) Positioner Mode 2 ·············3.3.3 [3] PIO Circuit
2) MEC Mode 2 ·····················3.5.3 [3] PIO Circuit