IAI America ERC3 User Manual
Page 271
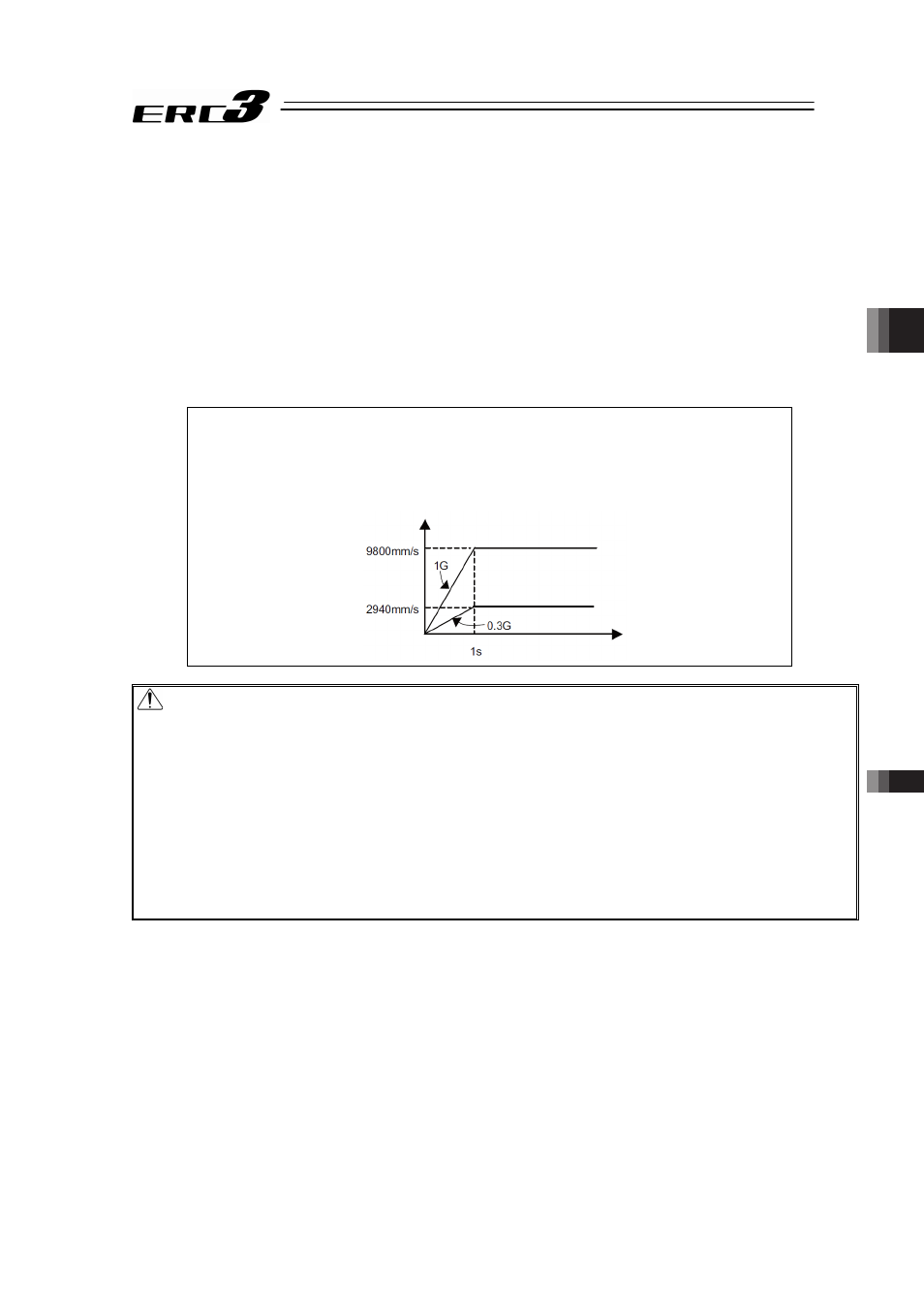
Chapter 4 Operation
4.4 Operation in MEC Mode 1 and 2 (Operation with PLC)
261
1) Position [mm] ············It is the positioning stop point. The position from the origin is to be set.
The positions must satisfy the following relationships: Start point <
Intermediate point < End point
2) Speed [mm/s] ············Set the velocity in the operation.
Do not attempt to input a value more than the maximum velocity or
minimum velocity
(Note 1)
.
(Note 1) For the minimum speed, you can either check in “1.2.1
Actuator” or figure out from the formula below.
Min. Speed [mm/s] = Lead Length [mm] / No. of Encoder Pluses / 0.001 [s]
3) Acceleration [G]·········Set the acceleration for the startup.
4) Deceleration [G] ········Set the deceleration (G) at which the actuator stops.
(Reference) Acceleration is explained. The same concept applies to deceleration.
1G = 9800mm/s
2
: Acceleration at which the actuator can accelerate to up
to 9800mm/s per second
0.3G: Acceleration at which the actuator can accelerate to up to
9800mm/s
u
0.3 = 2940mm/s
Caution: Setting the acceleration/deceleration
(1) Do not attempt to establish the setting exceeding the rated acceleration/deceleration of
the actuator. Failure to follow this may cause the life of the actuator to be shortened
extremely.
(2) If the actuator or work part receives impact or vibrates, lower the
acceleration/deceleration. If the actuator is used continuously in such condition, the life
of the actuator will drop significantly.
(3) If the transferable weight is significantly smaller than the rated payload capacity,
accelerations/decelerations greater than the rating may be set. You can shorten the
cycle time this way, so contact IAI if you are interested. When contacting IAI, let us
know the weight, shape and installation method of the work part as well as installation
condition of the actuator (horizontal/vertical).
5) Push force [%]···········Set the push torque (current-limiting value) to be used in push-motion
Instruction as a percent value.
Increasing the current-limiting value increases the push force.
If “0” is set, positioning Instruction is performed.
[Refer to the 1.2.1 Actuator for the relation between the pressing force
and current limiting value.]
6) Push width [mm] ·······Set the travel during push-motion Instruction.
When push-motion Instruction is performed, the actuator moves at the
speed and rated torque set as part of positioning information, just like
normal positioning, until the remaining travel enters the range set here.
Once the remaining travel enters this range, the actuator moves to the
position set in 1) while pushing the load.
How the actuator operates as it pushes the work part toward the end
point, start point and intermediate point is illustrated below.
Speed
Time