IAI America ERC3 User Manual
Page 246
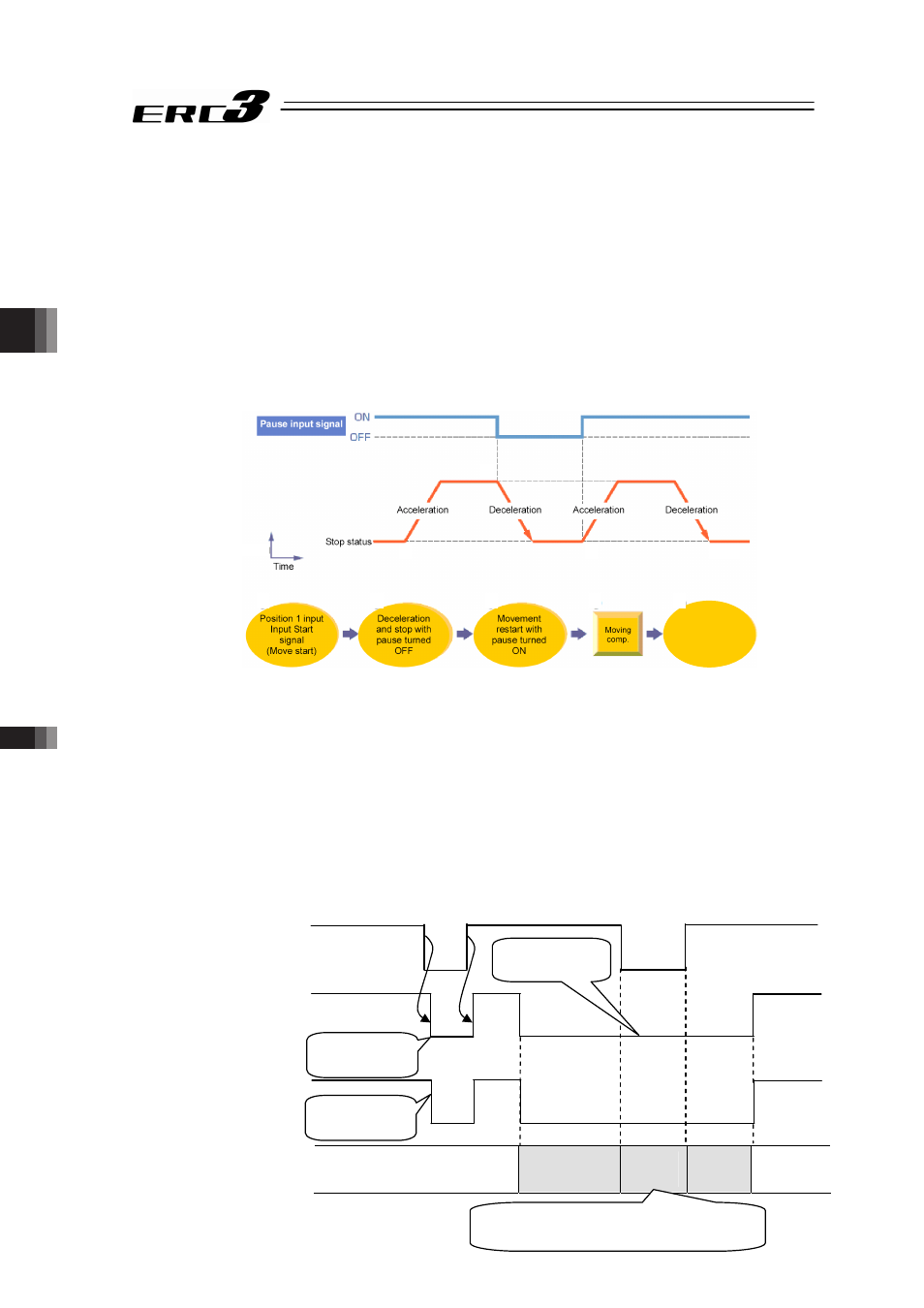
Chapter 4 Operation
4.2 Operation in Positioner Mode
4.2.3 Operation in Positioner Mode 2 (Operation Using PIO Converter)
236
(6) Pause and Operation Interruption (ST*, *STP, RES, PE*, PEND)
Pause is possible during movement. In this mode, the following two methods are possible for
pause.
1) Use of pause signal *STP
Turning reset signal RES ON during the pause allows the remaining moving distance to be
cancelled to interrupt the operation.
2) Use of start signal ST*
This method is valid when Parameter No.27 “Move command type” is set to “0” (factory
setting). The actuator can only be moved while the ST* signal is set to ON and stopped if
ST* is turned OFF. Since setting the ST* signal to OFF is assumed as interrupt of operation,
the remaining moving distance may not be cancelled.
I. Use of pause signal *STP
Control method
The pause signal is an input signal always set to ON. So, it is normally used to remain ON. Use
this function for interlock in case where an object is invaded into the moving direction of the
actuator being moved.
1) If pause signal *STP is turned OFF during operation of the actuator, the actuator is
decelerated to a stop. The deceleration is defined by the value set in the position table.
2) During pause, current position No. PE* and positioning complete signal PEND are not
turned ON.
3) If pause signal *STP is returned to ON, the actuator continues the remaining movement.
The acceleration is the value set in the position table.
4) Turning reset signal RES ON during pause (*STP being OFF) allows the remaining
movement to be canceled to interrupt the operation.
Before operation
Positioning complete state
Operation
Temp.
stop
Cont.
Op.
Position
complete
Velocity
Positioning
Completion
Signal Output
1)
2)
3)
4)
5)
1)
3)
4) 5)
2)
Turning RES ON here allows
continuous operation to be cancelled
Pause signal*STP
(PLCoController)
Positioning completion signal
PEND
(ControlleroPLC)
Operation of actuator
PEND turned
OFF
PEND and PE
not turned ON
Current position No.
PE*
(ControlleroPLC)
PE* turned
OFF