7 dual- axes on a dual- processing system – Rockwell Automation 8520 9/Series CNC Lathe User Manual
Page 777
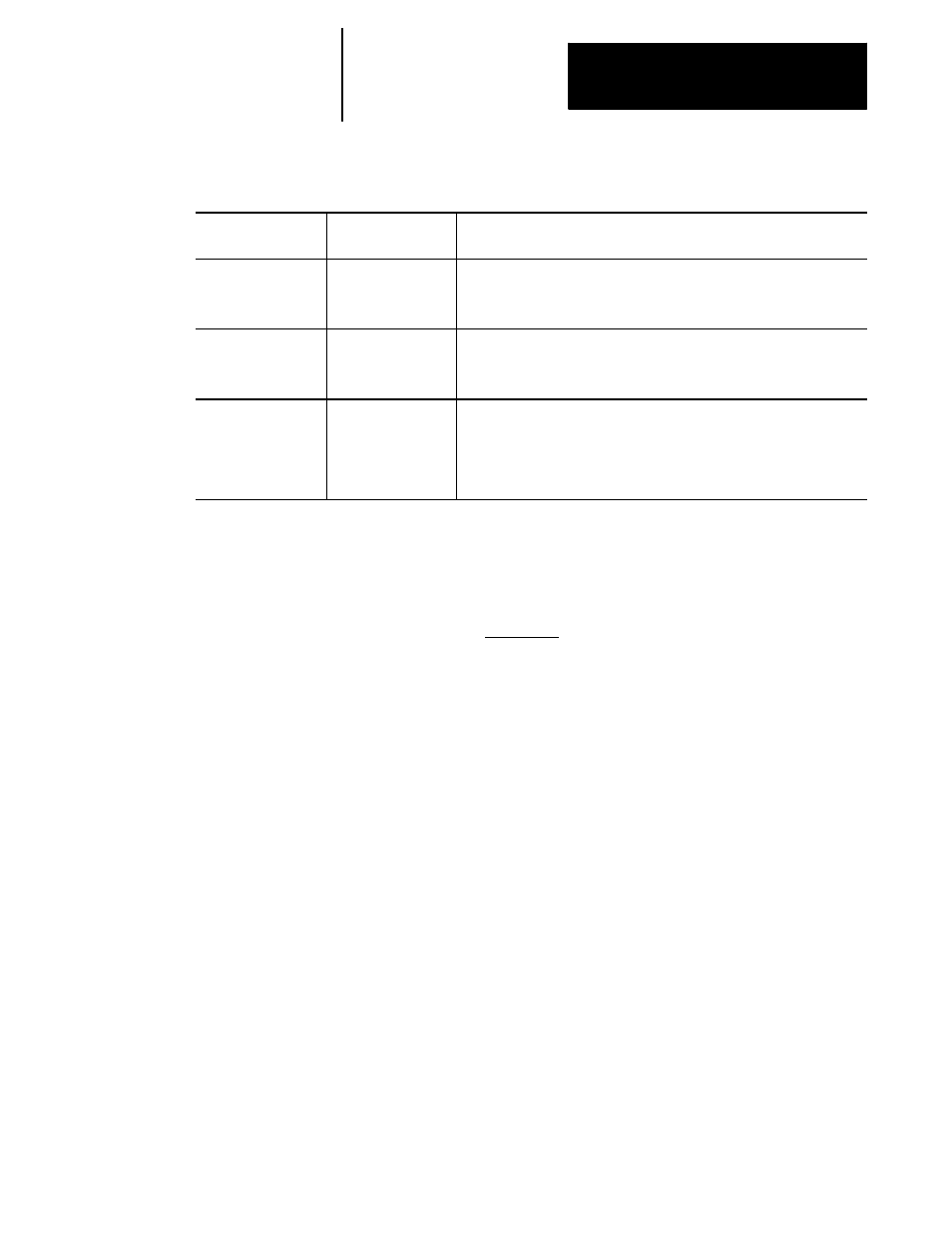
Chapter 30
Using a 9/Series Dual--Processing System
30-37
Example 30.10
Changing Processes with Tool Offsets
Process One
Activates this Tool
Process Two
Activates this Tool
Shared Axis
T1010;
(controls shared axis)
T000;
Process one activates tool offset on shared axis as defined in AMP
(delayed/immediate shift/move). When process two takes control of the
shared axis, the shared axis tool offset is canceled on the shared axis until it
is returned to the process.
T1111;
(controls shared axis)
T1111;
Has same offset for both processes. When you shift the shared axis between
processes, the offset remains active on the axis. When the shared axis
changes processes the tool offsets are re-initialized and the AMP selected
activation method (delayed/immediate shift/move) still occurs.
T1111;
T2222;
(controls shared axis)
Process two activates tool offset on shared axis as defined in AMP
(delayed/immediate shift/move). When you switch the shared axis to
processes one, the offset changes to the tool offset value requested in
process one. Since the offsets are re-initialized when shared axes change
processes, the AMP selected activation method (delayed/immediate
shift/move) still occurs.
The Dual--Axis feature allows the part programmer to simultaneously
control multiple axes while programming commands for only one. It
differs from the split axis feature of the control in that the split axis feature
is used to control a single axis positioned by two servo motors.
The dual--axis feature is especially useful for twin turret lathes and other
machines running with parallel cutting tools. Figure 30.15 shows a typical
configuration for dual axes.
30.7
Dual- Axes on a
Dual- Processing System