Important – Rockwell Automation 8520 9/Series CNC Lathe User Manual
Page 582
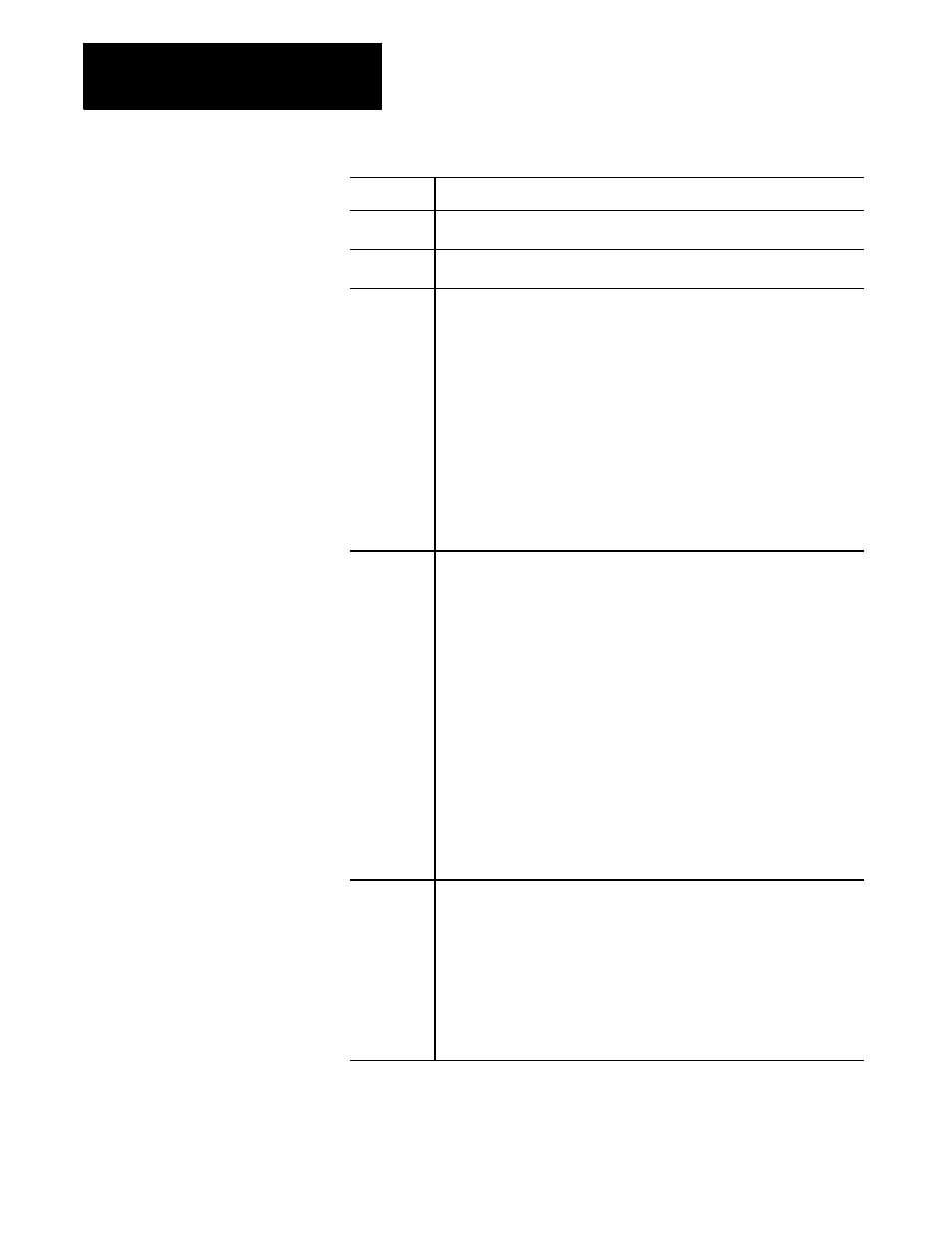
Compounding Turning Routines
Chapter 24
24-18
Where :
Is :
P__
the sequence number (N-word) of the first block in the set of contour blocks that
define the final contour.
Q__
the sequence number (N-word) of the last block in the set of contour blocks that
define the final contour.
U W
determine the finishing allowance that is left on the part when the routine is
completed. This finish allowance is typically removed later in the program when
a G72 finishing routine block is executed. The actual value of the finish
allowance is equal to the average of the U and W parameters (U+W)/2. It is not
necessary to enter both of these parameters in the calling block. If only one is
entered, the control uses half of the entered parameter value as the finish
amount. The finish allowance is optional and does not need to be programmed.
See Figure 24.15 to determine the sign of U and W. U and W are always
programmed as incremental values.
Important:
This manual makes the assumption that W and U are assigned
in AMP as the incremental axis names that correspond to the Z and X axes
respectively.
Important:
The value assigned to U is affected by radius/diameter mode
(G08/G09). W is not affected by radius diameter mode. If programming in
diameter mode the value of the finish allowance is really ((U/2)+W)/2.
I K
determine the amount of stock to be removed on the final pass of the routine.
The actual amount of material removed on this final pass is equal to the average
of the I and K parameters (I+K)/2. It is not necessary to enter both of these
parameters in the calling block. If only one is entered the control uses half of the
entered parameter value. The final pass is optional and does not need to be
programmed. It is not a roughing pass and it does not remove the finish
allowance. A final pass cuts tool paths that are parallel to the workpiece finish
shape.
Important:
This manual makes the assumption that I and K are assigned in
AMP as the integrand axis names that correspond to the X and Z axes
respectively.
Important:
The value assigned to I is always an incremental, radius value
regardless of the current mode (radius/diameter). K is always an incremental
value and is not affected by radius/diameter mode.
Important:
The system installer has the option of forcing a final pass to be
made by setting the proper AMP parameter. If this is the case the control cuts
the final pass regardless of whether I or K is programmed. When I and K are not
programmed and the system installer has forced a final pass to be made, the
control assumes I and K to be zero.
D__
the depth of cut for each pass except the final pass. No sign needs to be entered
for this parameter. The depth of cut for the final pass is determined with the I and
K parameters. D is always an incremental value regardless of the current mode.
Important:
It is possible to override the programmed depth of cut (D) using
an AMP parameter. The override setting is made in increments of 1% ranging
from 0-255%. See documentation prepared by the system installer for details.
The system installer may also determine a maximum allowable value of D in
AMP. If the D value programmed is larger than the maximum allowed in AMP,
the control overrides the programmed value and use the AMP assigned
maximum value.