Runtime errors – Rockwell Automation 1747-PT1, D1747NP002 Hand-Held Terminal User Manual
Page 355
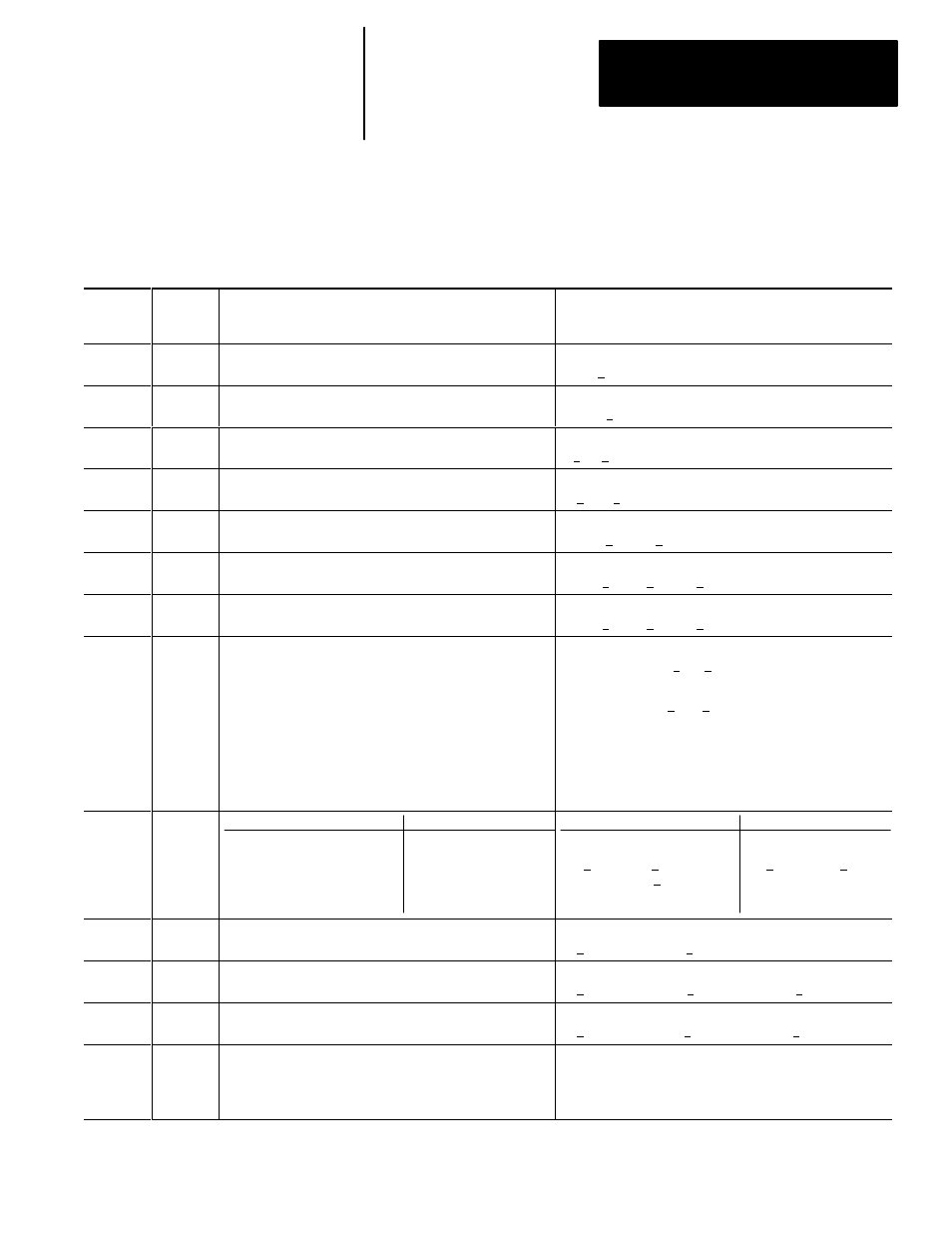
Chapter 26
PID Instruction
26–11
Error code 0036 appears in the status file (S:6) when a PID instruction
runtime error occurs. Code 0036 covers the following PID error conditions,
each of which has been assigned a unique single byte code value that appears
in the MSbyte (most significant byte or upper 8 bits) of the second word
(word 1) of the PID control block.
Error
Code
(Decimal)
Error
Code
(Hex)
Description of Error Condition or Conditions
Corrective Action
4352
11H
1) Loop update time D
t
> 255, or
2) Loop update time D
t
= 0
Change loop update time D
t
to
0 < D
t
< 255
4608
12H
1) Proportional gain K
c
> 255, or
2) Proportional gain K
c
= 0
Change proportional gain K
c
to
0 < K
c
< 255
4864
13H
Integral gain (reset) T
i
> 255
Change integral gain (rate) T
i
to
0 < T
i
< 255
5120
14H
Derivative gain (rate) T
d
> 255
Change derivative gain (rate) T
d
to
0 < T
d
< 255
8448
21H
1) Scaled setpoint max Smax > 16383, or
2) Scaled setpoint max Smax < –16383
Change scaled setpoint max Smax to
–16383 < Smax < 16383
8704
22H
1) Scaled setpoint min Smin > 16383, or
2) Scaled setpoint min Smin < –16383
Change scaled setpoint min Smin to
–16383 < Smin < Smax < 16383
8960
23H
Scaled setpoint min Smin > Scaled setpoint max Smax
Change scaled setpoint min Smin to
–16383 < Smin < Smax < 16383
12544
31H
If you are using setpoint scaling and Smin >
setpoint SP > Smax, or
If you are not using setpoint scaling and 0 >
setpoint SP > 16383,
then during the initial execution of the PID loop, this error occurs
and bit 11 of word 0 of the control block is set. However, during
subsequent execution of the PID loop if an invalid loop setpoint
is entered, the PID loop continues to execute using the old
setpoint, and bit 11 of word 0 of the control block is set.
If you are using setpoint scaling, then change the
setpoint SP to Smin < SP < Smax, or
If you are not using setpoint scaling, then change
the setpoint SP to 0 < SP < 16383.
16640
41H
Scaling Selected Scaling Deselected
1) Deadband < 0, or 1) Deadband < 0, or
2) Deadband > 2) Deadband > 16383
(Smax - Smin), or
3) Deadband > 16383
Scaling Selected Scaling Deselected
Change deadband to Change deadband to
0 < deadband < 0 < deadband <
(Smax – Smin) < 16383
16383
20736
51H
1) Output high limit < 0, or
2) Output high limit > 100
Change output high limit to
0 < output high limit < 100
20992
52H
1) Output low limit < 0, or
2) Output low limit > 100
Change output low limit to
0 < output low limit < output high limit < 100
21248
53H
Output low limit > output high limit
Change output low limit to
0 < output low limit < output high limit < 100
24576
60H
PID is being entered for the second time. (PID loop was inter-
rupted by an I/O interrupt, which is then interrupted by the PID STI
interrupt.)
You have at least three PID loops in your program: One in the
main program or subroutine file, one in an I/O interrupt file, and
one in the STI subroutine file. You must alter your ladder program
and eliminate the potential nesting of PID loops.
Runtime Errors