Rockwell Automation 1747-PT1, D1747NP002 Hand-Held Terminal User Manual
Page 349
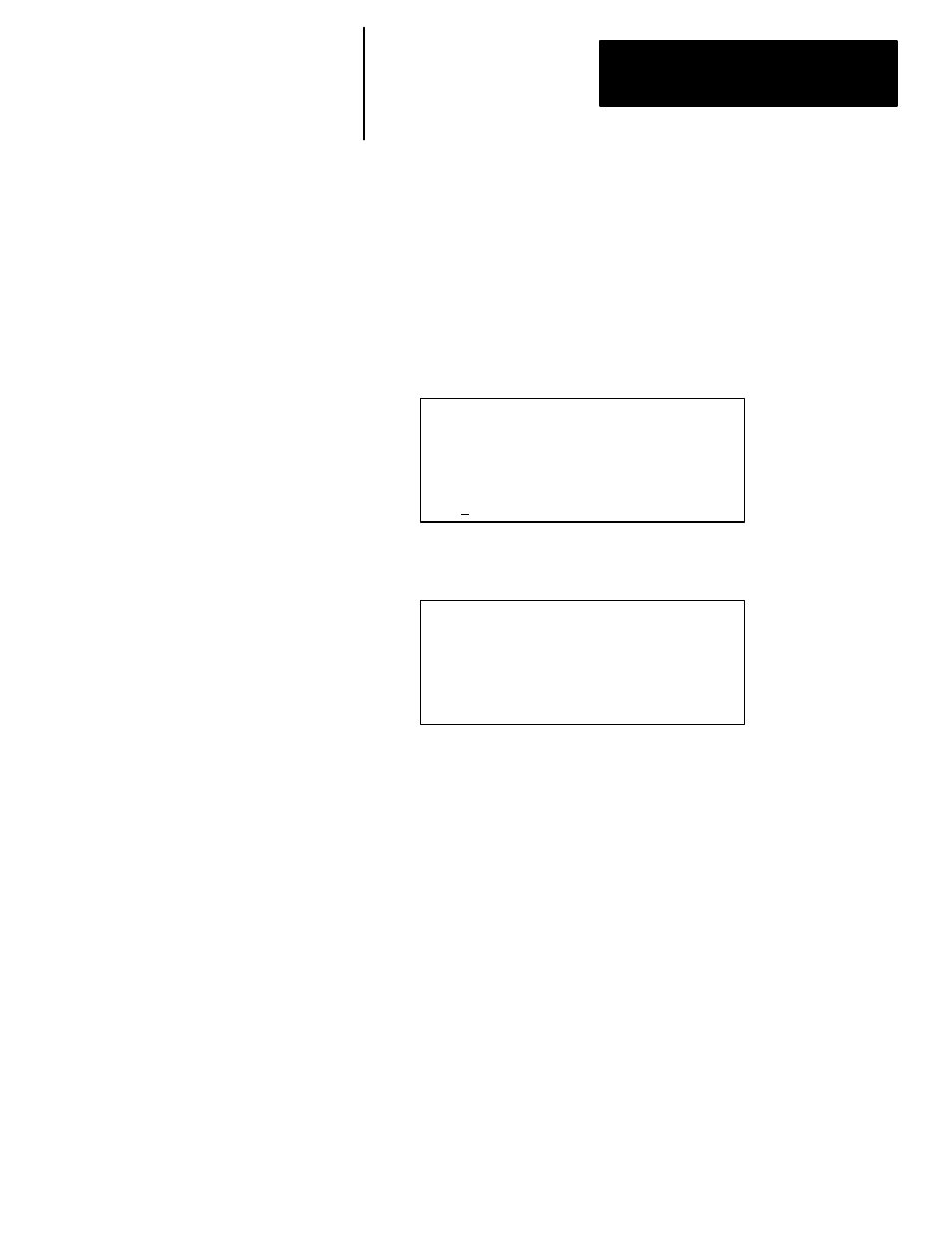
Chapter 26
PID Instruction
26–5
•
Process (also called the Process Variable, PV) – This is an element
address that stores the process input value. This address can be the
location of the analog input word where the value of the input A/D is
stored. This value could also be an integer value if you choose to
pre-scale your input value to the range 0–16383.
•
Output (also called Control Variable, CV) – This is an element address
that stores the output of the PID instruction. The output value ranges
from 0 to 16383, with 16383 corresponding to a control output percent of
100. This is normally an integer value, so that you can scale the PID
output range to the particular analog range your application requires.
The display below shows typical values entered for these parameters:
F1
F2
F3
F4
F5
ZOOM on PID –(PID)– 1/3 2.0.0.0.*
NAME: PROP INTEGRAL DERIVATIVE
CONT BLK: N7:2
PROCESS: N7:0
OUTPUT: N7:1
CONTROL BLOCK SIZE 23 WORDS
ENTER CONTROL BLK: N7:2
NEXT PG
Pressing
[F1],
NEXT_PG brings up the second display:
F1
F2
F3
F4
F5
ZOOM on PID –(PID)– 2/3 2.0.0.0.*
NAME: PROP INTEGRAL DERIVATIVE
GAIN: 0 [/10] MIN OUT: 0%
RESET: 0 [/10 M/R] MAX OUT: 0%
RATE: 0 [/100 MIN] AUTO/MAN: AUTO
SETPOINT: 0 DEADBAND: 0
ENTER GAIN: 0
You enter the following parameters at this display:
•
Gain (control block word 3) – This is the Proportional gain (k
c
), ranging
from 0.1 to 25.5. A rule of thumb is to set this gain to one half the value
needed to cause the output to oscillate when the reset and rate terms
(below) are set to zero. Entered range: 1–255.
•
Reset (control block word 4) – This is the Integral gain (1/T
I
), ranging
from 0.1 to 25.5 minutes per repeat. A rule of thumb is to set the reset
time equal to the natural period measured in the above gain calibration.
Entered range: 1–255. Note: the value 255 will add the minimum integral
term possible into the PID equation.
•
Rate (control block word 5) – This is the derivative term (T
D
). The
adjustment range is 0.01 to 2.55 minutes. A rule of thumb is to set this
value to 1/8 of the integral time above. Entered range: 1–255.
•
Setpoint (SP) (control block word 2) – This is the desired control point
of the process variable. Type in the desired value and press ENTER. You
can change this value with instructions in your ladder program. Write the
value to the third word in the control block (for example write the value
to N7:4 if your control block is N7:2). Without scaling, the range of this
value is 0–16383. Otherwise, the range is scaled setpoint min (Smin)
(word 8) to scaled setpoint max (Smax) (word 7).