Rockwell Automation 1747-PT1, D1747NP002 Hand-Held Terminal User Manual
Page 350
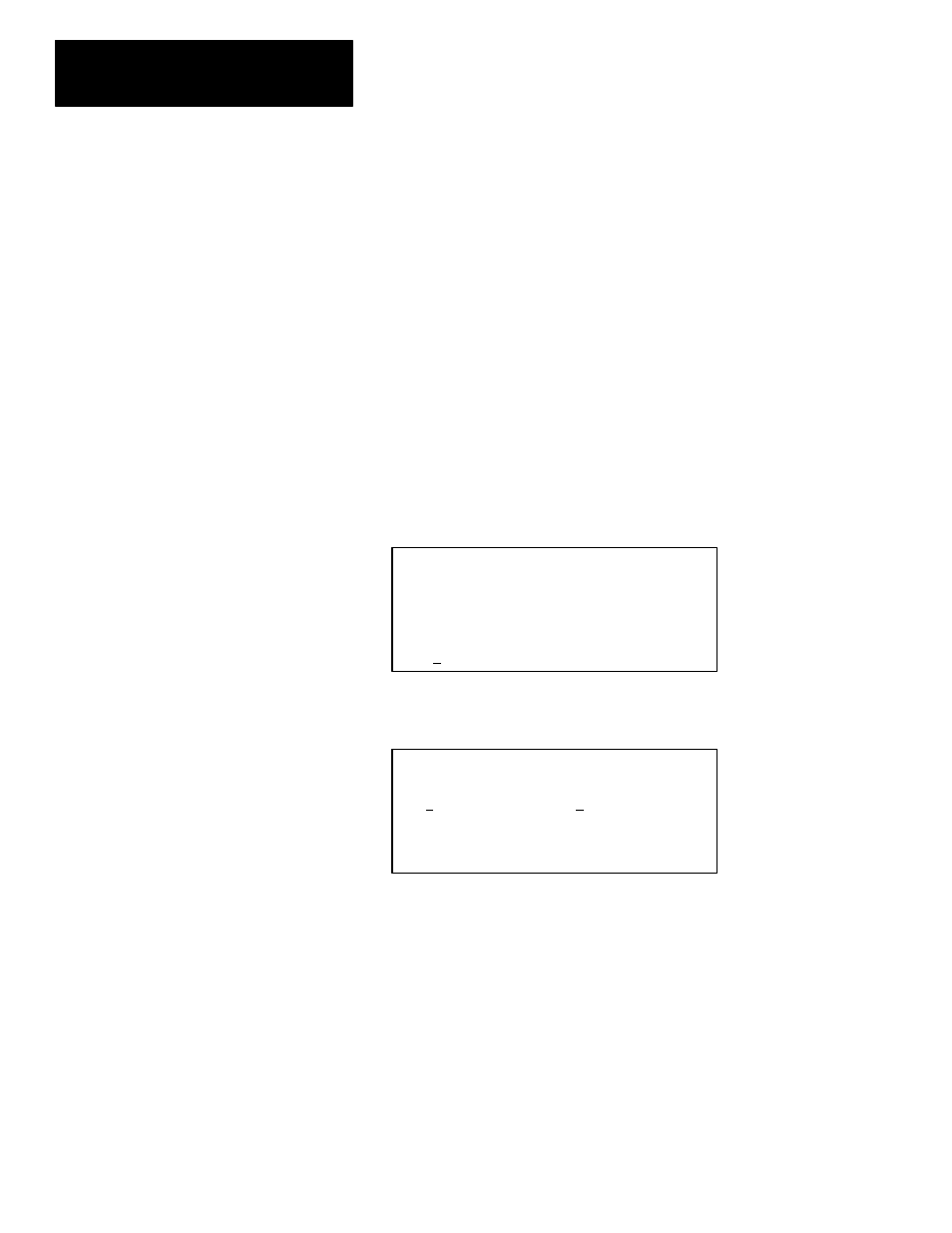
Chapter 26
PID Instruction
26–6
•
Minimum output (control block word 12) – If you want to use output
limiting or alarms, enter a value. If the output limit bit is also set, this
value is the minimum control output percent (word 16) that the control
variable (CV) obtains or outputs.
•
Maximum output (control block word 11) – If the output limit bit is
also set, the value you enter is the maximum control output percent (word
16) that the control variable (CV) obtains or outputs.
•
Auto/manual (control block word 0, bit 1) – The default condition is
AUTO. This indicates that the PID is controlling the output. MANUAL
indicates that the user is setting the output value. When tuning, we
recommend that changes be made in the MANUAL mode, followed by a
return to AUTO. Output limiting is applied in the MANUAL mode.
•
Deadband (control block word 9) – Enter a non-negative value. The
deadband extends above and below the setpoint by the value you enter.
The deadband is entered at the zero crossing of the process variable PV
and the setpoint SP. This means that the deadband is in effect only after
the process variable PV enters the deadband and passes through the
setpoint SP. Range: 0-scaled max, or 0–16383 when no scaling exists.
The display below shows typical values entered for these parameters:
F1
F2
F3
F4
F5
ZOOM on PID –(PID)– 2/3 2.0.0.0.*
NAME: PROP INTEGRAL DERIVATIVE
GAIN: 25 [/10] MIN OUT: 5%
RESET: 10 [/10 M/R] MAX OUT: 95%
RATE: 1 [/100 MIN] AUTO/MAN: AUTO
SETPOINT: 500 DEADBAND: 5
ENTER GAIN: 255
NEXT PG
Pressing
[F1]
, NEXT_PG brings up the third display:
F1
F2
F3
F4
F5
ZOOM on PID –(PID)– 3/3 2.0.0.0.*
NAME: PROP INTEGRAL DERIVATIVE
LOOP UPDATE: 0 [X10ms]
SET PT MIN: 0 SET PT MAX: 0
MODE: STI OUT LIMIT: NO
CONTROL: REVERSE
ENTER LOOP UPDATE: 0
You enter the following parameters at this display:
•
Loop update (control block word 13) (D
t
) – This is the time interval
between PID calculations. The entry is in 0.01 second intervals. A rule
of thumb is to enter a loop update time five to ten times faster than the
natural period of the load (determined by setting the reset and rate
parameters to zero and then increasing the gain until the output begins to
oscillate). When in the STI mode, this value must equal the STI time
interval value S:30. Entered range: 1–255. In timed mode, the PID loop
is only calculated upon time–out of the loop update and not every scan.