Axis-specific parameters, Appendix – IAI America TT-C3 User Manual
Page 310
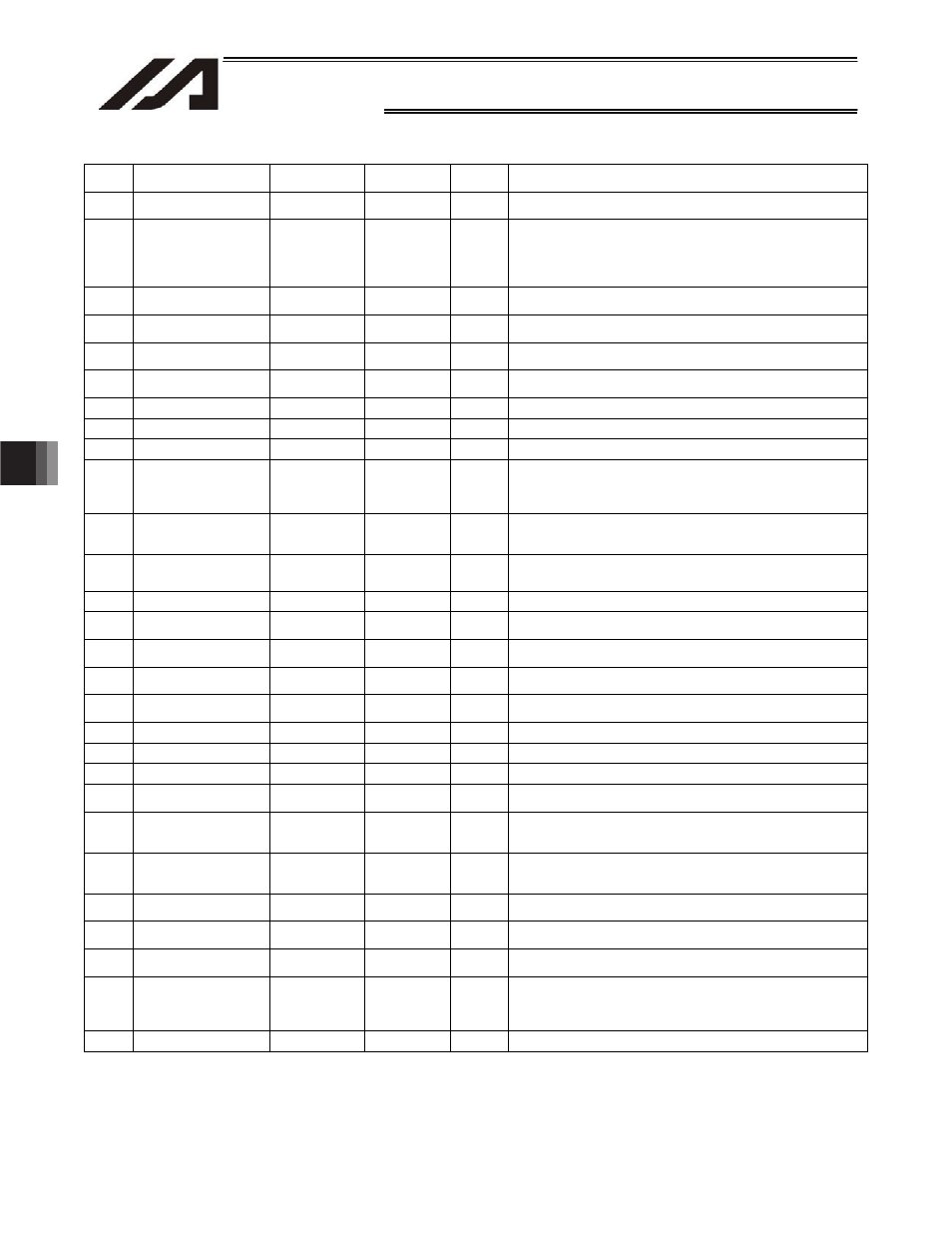
300
INTELLIGENT ACTUATOR
Appendix
Appendix
Axis-Specific Parameters
No Parameter
name
Default value
(Reference)
Input range
Unit
Remarks
31
Offset travel speed at
home return
3
1 to 500
mm/sec
32
Actual distance between
phase Z and end
0 -1
to
99999
0.001
mm
Absolute distance from the end (mechanical or LS). Obtained
automatically if the distance is a negative value. When multiple
actuators are combined, it is recommended to write the flash ROM
after automatic acquisition. (Refer to axis-specific parameter No.
76)
33 Ideal
distance
between
phase Z and end
0
0 to 99999
0.001
mm
Absolute distance from the end (mechanical or LS). (Refer to axis-
specific parameter No. 76)
34 Brake
equipment
specification
0
0 to 1
0: Not equipped, 1: Equipped
35
Brake unlock check time
10
0 to 3000
msec
Time after receiving a brake-unlock start response until transition to
an operation-enabled status
36
Brake lock check time
10
0 to 1000
msec
Time after receiving a brake-lock start response until start of servo
OFF
37
Change prohibited
0
0 to 1
0: Rotary encoder
38
Encoder ABS/INC type
0
0 to 1
0: INC, 1: ABS
39
Change prohibited
1
0 to 1
40 Pole-sense
initial
tryout
direction selection
(For future expansion =
Change prohibited)
0
0 to 1
0: Negative end of the coordinate system
1: Positive end of the coordinate system
41 Pole
sense
speed
(For future expansion =
Change prohibited)
25
1 to 100
DRVVR
42
Encoder resolution
800
0 to 99999999
Pulse/rev,
0.001
Pm/pulse
Pulses (before division)/rev, in the case of a rotary encoder
43
Encoder division ratio
0
-7 to 7
Pulses are multiplied by (“n”th power of 1/2).
44 Length
measurement
correction
0 -99999999
to
99999999
0.001
mm/1M
Valid only for linear movement axes. (Coordinates other than the
encoder reference Z point will change proportionally.)
45 to
46
(For expansion)
0
47
Screw lead
6000
1 to 99999999
0.001
mm
Valid only for linear movement axes.
48 to
49
(For expansion)
0
50
Gear ratio numerator
1
1 to 99999999
51
Gear ratio denominator
1
1 to 99999999
52 (For
expansion)
0
53
Setting bit pattern 1 of
each axis
0 0H
to
FFFFFFFFH
54
Travel distance for push
stop detection at home
return
20
1 to 99999
0.001
mm
Used to check the push motion during home return.
55
Travel distance for push
stop detection at
positioning
30
1 to 99999
0.001
mm
Used to check the push motion during PUSH command operation.
56 Push-abort
deviation
ratio at home return
5000
1 to 99999
Deviation is compared against “Steady-state deviation of push
speed + Push-speed pulse speed x Abort deviation ratio.”
57 Push-abort
deviation
ratio at positioning
5000
1 to 99999
Deviation is compared against “Steady-state deviation of push
speed + Push-speed pulse speed x Abort deviation ratio.”
58
Positioning band
100
1 to 9999
0.001
mm
59 Allowable
deviation
error ratio
(Maximum speed pulse
ratio)
300
1 to 9999
Deviation is compared against “Steady-state deviation of maximum
operating speed of each axis + Pulse speed of maximum operating
speed of each axis x Allowable deviation error ratio.”
60
Position gain
45
1 to 9999
/s