Melsec-q, 5 data used for positioning control, Table 1 – MITSUBISHI ELECTRIC Mitsubishi Programmable Logic Controller QD75D User Manual
Page 119: Pr.17 torque limit setting value, Pr.18 m code on signal output timing
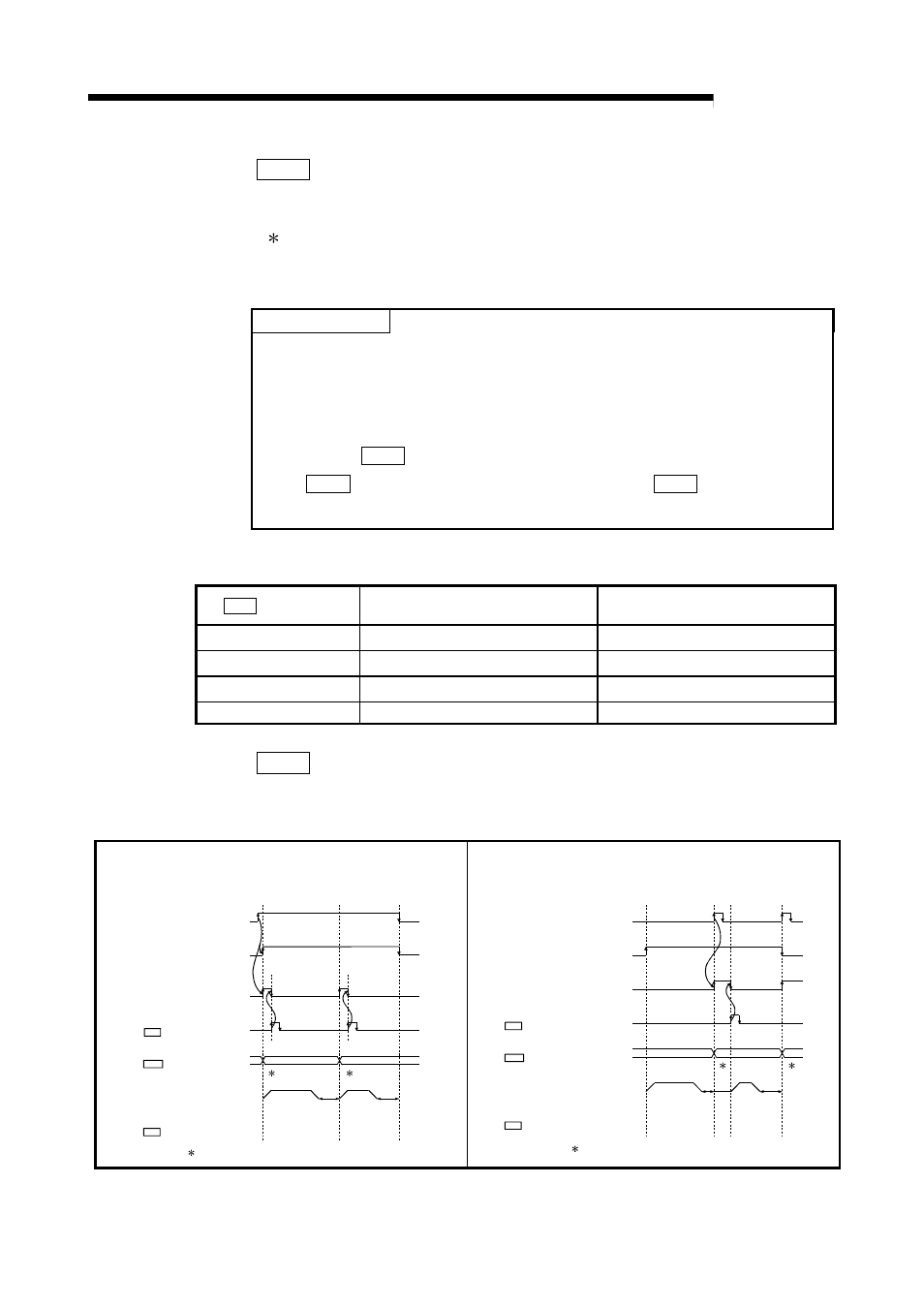
5 - 31
MELSEC-Q
5 DATA USED FOR POSITIONING CONTROL
Pr.17 Torque limit setting value
Set the maximum value of the torque generated by the servomotor as a
percentage between 1 and 500%.
The torque limit function limits the torque generated by the servomotor within
the set range.
If the torque required for control exceeds the torque limit value, it is controlled
with the set torque limit value.
Usage conditions
Limits for pulse train output type
(a)
A drive unit that can issue a torque limit command with the analog voltage is
required.
(b)
The D/A conversion module and the D/A conversion module and drive unit
must be wired.
(c)
The set "
Pr.17
Torque limit setting value" is set in the buffer memory
"
Md.35
Torque limit stored value", so transmit that "
Md.35
Torque limit
stored value" to the D/A conversion module with the sequence program.
[Table 1]
Pr.1
setting value
Value set with peripheral device
(unit)
Value set with sequence program
(unit)
0 : mm
0.1 to 214748364.7 (µm)
1 to 2147483647 (×10
–1
µm)
1 : inch
0.00001 to 21474.83647 (inch)
1 to 2147483647 (×10
–5
inch)
2 : degree
0.00001 to 21474.83647 (degree)
1 to 2147483647 (×10
–5
degree)
3 : pulse
1 to 2147483647 (pulse)
1 to 2147483647 (pulse)
Pr.18 M code ON signal output timing
This parameter sets the M code ON signal output timing.
Choose either WITH mode or AFTER mode as the M code ON signal output
timing.
WITH mode......... An M code is output and the M code ON
signal is turned ON when a positioning
operation starts.
m1
m2
01 (continuous)
00 (end)
Positioning start signal
[Y10,Y11,Y12,Y13]
BUSY signal
[XC,XD,XE,XF]
Positioning
M code ON signal
[X4,X5,X6,X7]
M code OFF request
[1504,1604,1704,1804]
Cd.7
Operation pattern
Da.1
Valid M code
Md.25
: m1 and m2 indicate set M codes.
AFTER mode ...... An M code is output and the M code ON
signal is turned ON when a positioning
operation completes.
: m1 and m2 indicate set M codes.
m1
m2
01 (continuous)
00 (end)
Positioning complete signal
[X14,X15,X16,X17]
BUSY signal
[XC,XD,XE,XF]
Positioning
M code ON signal
[X4,X5,X6,X7]
M code OFF request
[1504,1604,1704,1804]
Cd.7
Operation pattern
Da.1
Valid M code
Md.25
Note: If AFTER mode is used with speed control, an M code will not be output and the M code ON signal will not be
turned ON.