7 parameter of the motion profile is not evaluated, 8 utilisation of the dc busbar system is xxx, 18 drive dimensioning messages – Lenze DSD User Manual
Page 443
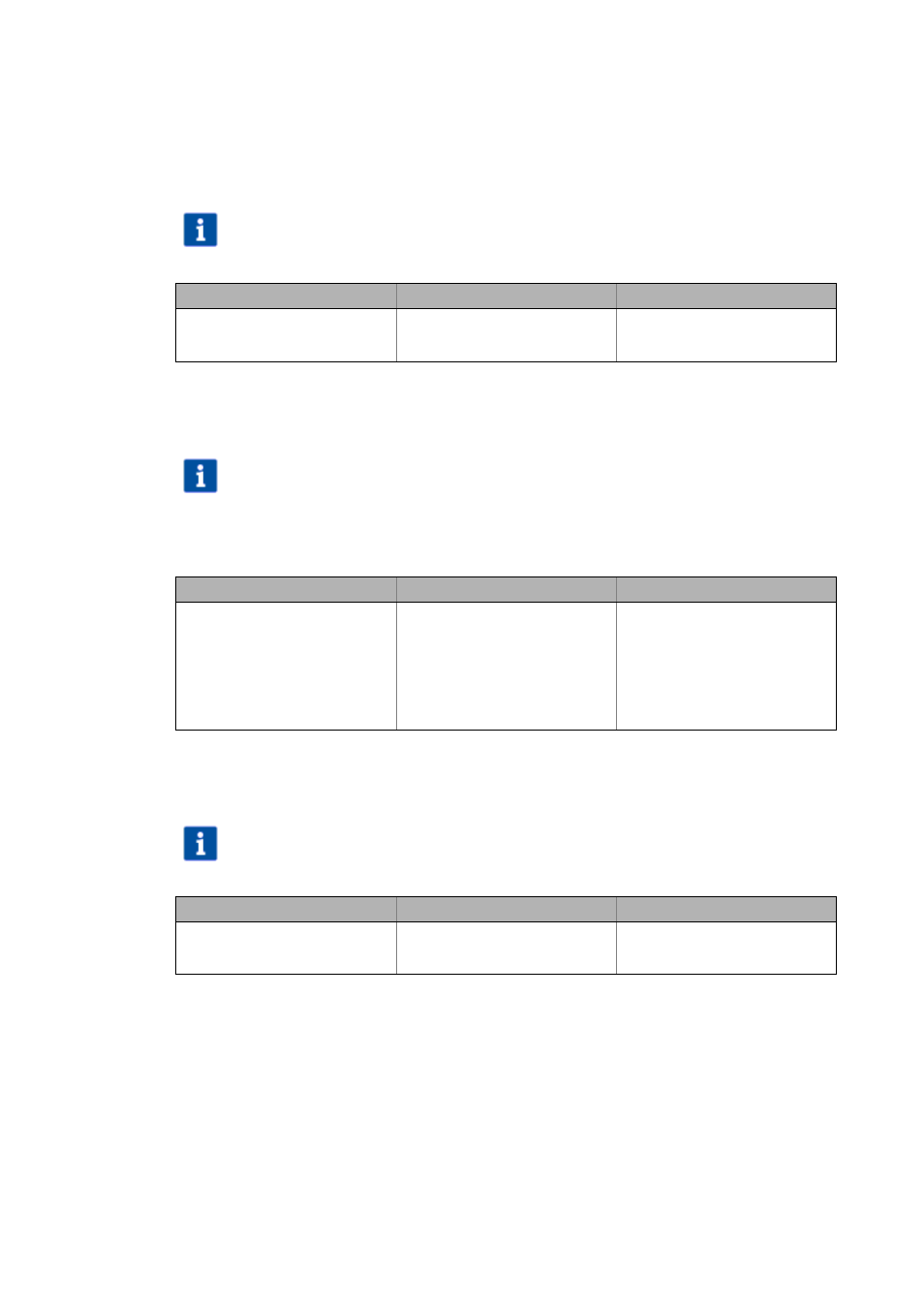
Lenze · Drive Solution Designer · Manual · DMS 4.2 EN · 12/2013 · TD23
443
18
Drive dimensioning messages
18.1
Applications
_ _ _ _ _ _ _ _ _ _ _ _ _ _ _ _ _ _ _ _ _ _ _ _ _ _ _ _ _ _ _ _ _ _ _ _ _ _ _ _ _ _ _ _ _ _ _ _ _ _ _ _ _ _ _ _ _ _ _ _ _ _ _ _
18.1.7
Parameter of the motion profile is not evaluated
18.1.8
Utilisation of the DC busbar system is xxx %
18.1.9
Torque setting range > 50 for winding control mode xxx
Note!
The motion profile contains the parameter "xxx".
The parameter is not required for the application and thus not evaluated.
Cause
Effects
Possible remedies
The opened motion profile contains a
parameter that does not appear in
the selected application.
DSD ignores the parameter in the cal-
culation of the motion profile.
• Select an application in which the
parameter appears.
• Correct the motion profile.
Note!
In the worst case, the utilisation of the DC busbar system may be %.
Hence, the sum of the DC-bus currents of the axis modules may exceed the permissible limit value (100 A)
of the DC busbar system.
Check the sequence of the axis modules for optimal current distribution in the DC busbar system.
See DSD protocol for the required power of the individual axis modules as an orientation guide.
Cause
Effects
Possible remedies
Due to an unfavourable arrangement
(sequence) of the axis modules, the
DC busbars may be overloaded.
Excessive heat generation damages
the DC busbar system.
• Check topology to ensure that the
current value in the DC busbar
system, including sections, does
not exceed 100 A.
• Divide the DC-bus connection and
supply via separate power supply
modules or regenerative power
supply modules.
Note!
The selected winding control mode xxx is not suitable for torque setting range yyy (limit value: 50).
Select a control mode with tensile force sensor in the web or a dancer control.
Cause
Effects
Possible remedies
The torque setting range results from
the entered values for tensile force
and diameter.
Minimum tensile forces cannot be
reached or cannot be repeated.
• Carry out recommended meas-
ures.