17 rotary table drive, 1 calculations, Rotary table drive – Lenze DSD User Manual
Page 170: 7applications
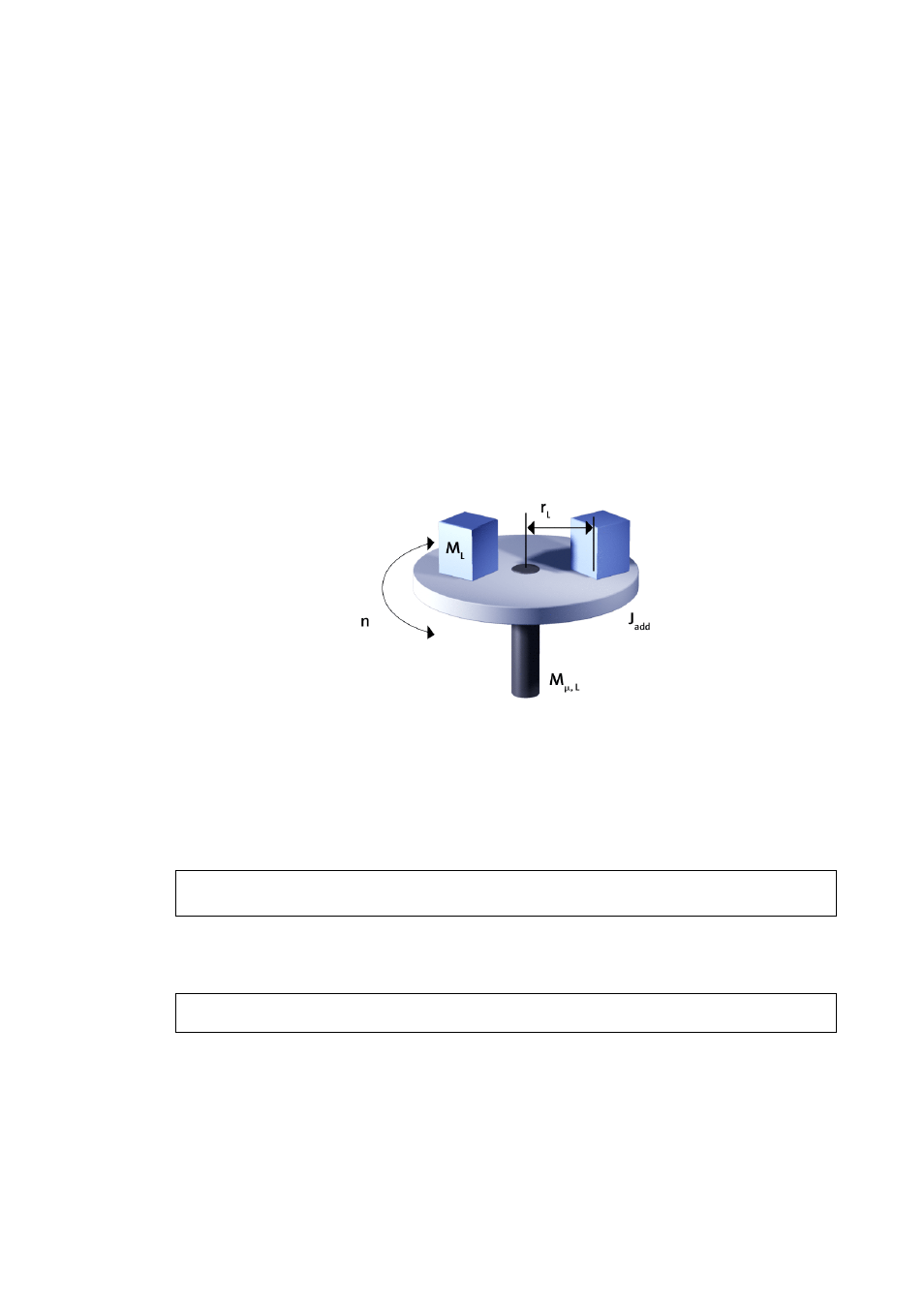
7
Applications
7.17
Rotary table drive
170
Lenze · Drive Solution Designer · Manual · DMS 4.2 EN · 12/2013 · TD23
_ _ _ _ _ _ _ _ _ _ _ _ _ _ _ _ _ _ _ _ _ _ _ _ _ _ _ _ _ _ _ _ _ _ _ _ _ _ _ _ _ _ _ _ _ _ _ _ _ _ _ _ _ _ _ _ _ _ _ _ _ _ _ _
7.17
Rotary table drive
A rotary table drive is often used for positioning processes in filling and packaging machines. The
table is placed horizontally, the payloads are arranged symmetrically.
The mechanics define the achievable speed and thus the dynamic performance of the positioning
process to a great extent, as well as the repeat accuracy and therefore the quality of the positioning.
Characteristics of a rotary table drive
• In the case of a rotary table drive a mass inertia has to be accelerated and decelerated again in
a rotary manner.
• Friction torques have to be overcome, which can be caused by the bearing friction and within
the machining process.
Requirements with regard to a drive system for positioning
• High dynamic performance to achieve short positioning times,
• High accuracy, according to the application
• High degree of reliability
7.17.1
Calculations
For a rotary table drive according to the drawing the following applies:
Moment of inertia
For the calculation of the moment of inertia no eccentric masses are taken into consideration.
[7-162] Equation 1: Moment of inertia
Dynamic torque of the application
[7-163] Equation 2: Dynamic torque of the application
J
sum
J
add
m
L
r
L
2
⋅
+
=
M
dyn
J
sum
α
⋅
=