11 drive dimensioning – Lenze DSD User Manual
Page 333
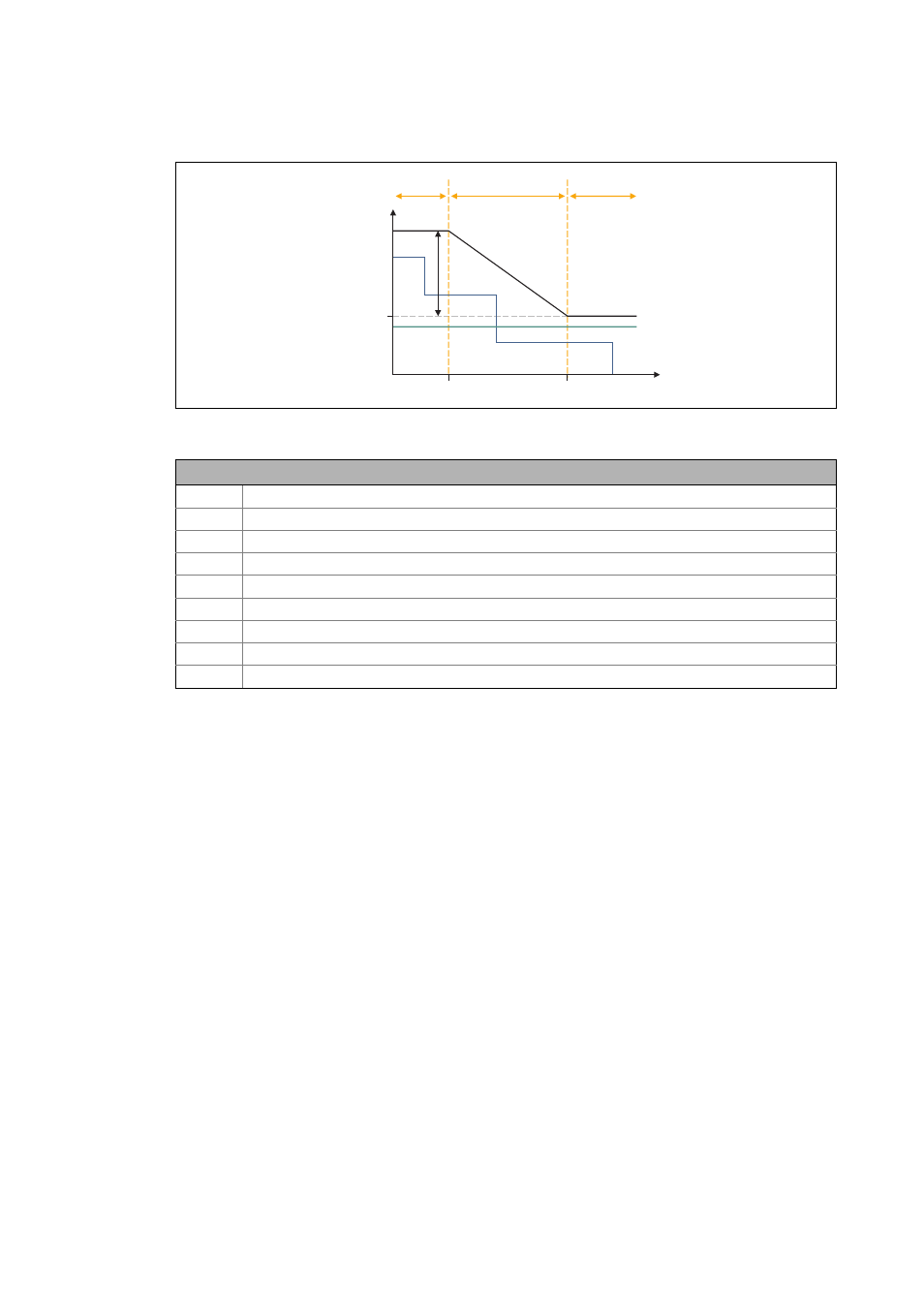
Lenze · Drive Solution Designer · Manual · DMS 4.2 EN · 12/2013 · TD23
333
11
Drive Dimensioning
11.4
Lenze gearbox selection
_ _ _ _ _ _ _ _ _ _ _ _ _ _ _ _ _ _ _ _ _ _ _ _ _ _ _ _ _ _ _ _ _ _ _ _ _ _ _ _ _ _ _ _ _ _ _ _ _ _ _ _ _ _ _ _ _ _ _ _ _ _ _ _
[11-10] Wöhler characteristic (load over number of stress cycles)
When the static strength and the endurance strength are calculated, the calculations in the DSD dif-
fer depending on the selected kinematic characteristic.
• In case of the freely defined motion profile, the current torque profile is checked against the
max. torque (2 × M
per,out
) and against the rated torque M
per,out
.
• The equivalent torque is calculated on the basis of the motion profile.
• The equivalent torque refers to the rated torque M
per,out
and expresses the stress of the gear-
box bearings even if the gearbox is operated in the range rated for endurance strength re-
garding the toothing.
• The fatique strength is only calculated if the gear toothing is operated in the fatique strength
range (i.e.. above the permissible output torque).
• If the value is < 100 %, the wear is within a permissible range. The gearbox withstands the
loads for at least five years.
• If the value is > 100 %, the wear is probably out of range. The gearbox does probably not with-
stand the loads for five years.
• An alternating torque at the toothing is called alternating load and stresses the gearbox more
than a non-alternating torque (e.g. in case of a hoist drive).
• For a drive dimensioning with freely defined motion profile, an alternating load factor is au-
tomatically calculated. When the static strength is tested and the fatique strength is calcu-
lated, this factor is taken into consideration. Here, the required torque is multiplied by a value
of 1 … 1.4.
1000
3 × 10
6
2.0
M [Nm]
N
M
per,out
2
1
0
Description
Static strength
Fatique strength
Endurance strength
Torque (double torque for calculating the short-time strength)
Wöhler characteristic: characteristic curve for the evaluation of the load
Torque load collective
Equivalent torque
Number of duty cycles
M
per,out
Rated torque at the output end