10 application notes for motion profiles, 1 minimum acceleration and deceleration times, 8motion design – Lenze DSD User Manual
Page 263
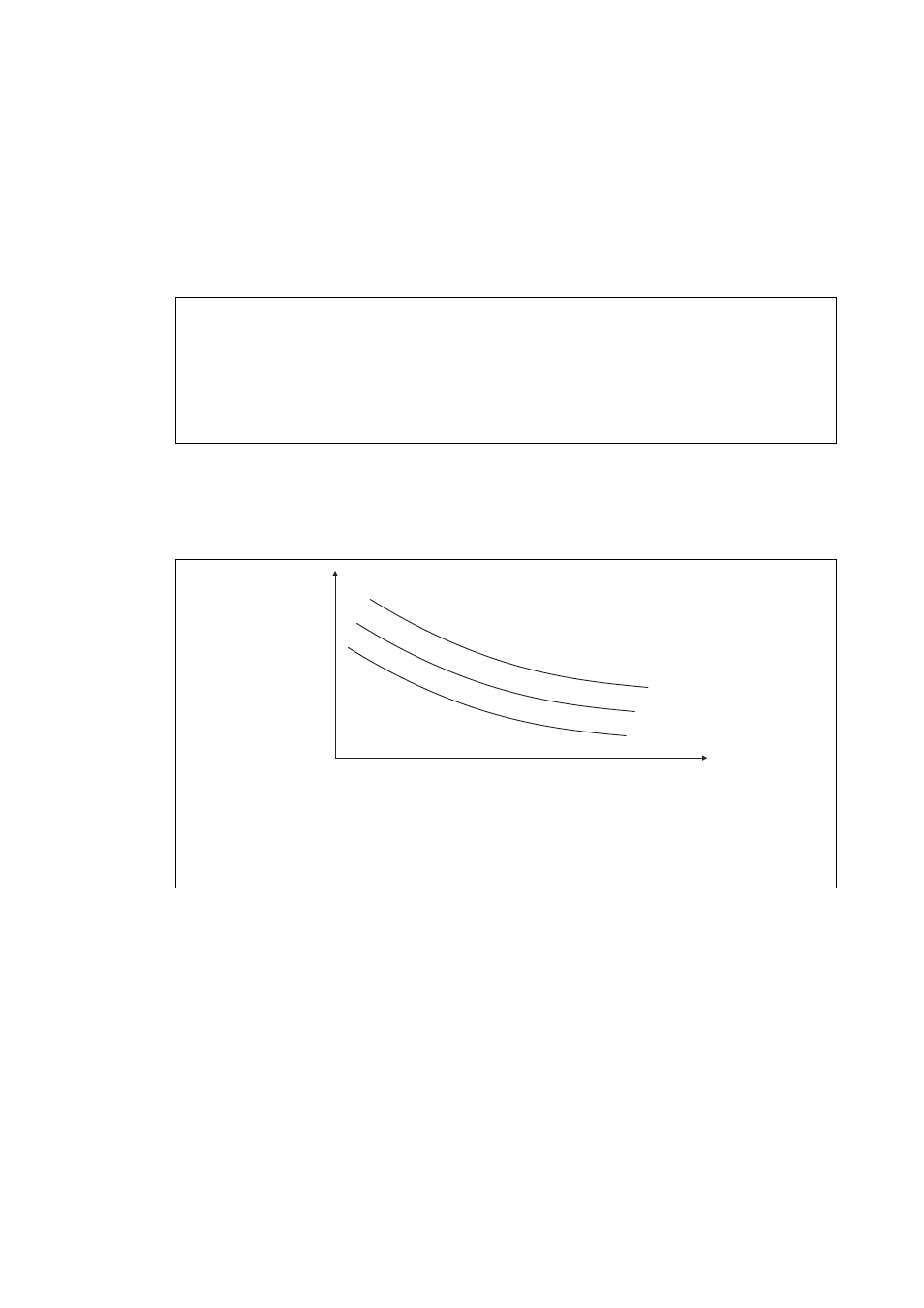
Lenze · Drive Solution Designer · Manual · DMS 4.2 EN · 12/2013 · TD23
263
8
Motion design
8.2
MotionDesigner
_ _ _ _ _ _ _ _ _ _ _ _ _ _ _ _ _ _ _ _ _ _ _ _ _ _ _ _ _ _ _ _ _ _ _ _ _ _ _ _ _ _ _ _ _ _ _ _ _ _ _ _ _ _ _ _ _ _ _ _ _ _ _ _
8.2.10
Application notes for motion profiles
8.2.10.1
Minimum acceleration and deceleration times
For increasingly lower acceleration and deceleration times the requirement with regard to the dy-
namic torque increases proportionally to the acceleration and reciprocal to the acceleration or de-
celeration time:
• Thus a greater drive is required, which, however, has to accelerate itself as well.
• For greater motors the accelerating power is smaller than for smaller motors. It is therefore
possible that a motor selected later on can no longer meet the specifications.
• These interdependencies are automatically taken into consideration in the DSD, so that a
warning is output if limit values are exceeded.
[8-1]
Acceleration capability as a function of the frame size
t
r
= acceleration time
t
f
= deceleration time
M
dyn
= dynamic torque
α = angular acceleration
M
N
= rated torque
Standard asynchronous motor
Asynchronous servo motor
Synchronous servo motor
M
dyn
a or M
dyn
α
∼
∼
M
dyn
1
t
r
----
or M
dyn
1
t
f
----
∼
∼
a,
a
motorsize
~ M
N