1 "application" image, 3user interface – Lenze DSD User Manual
Page 28
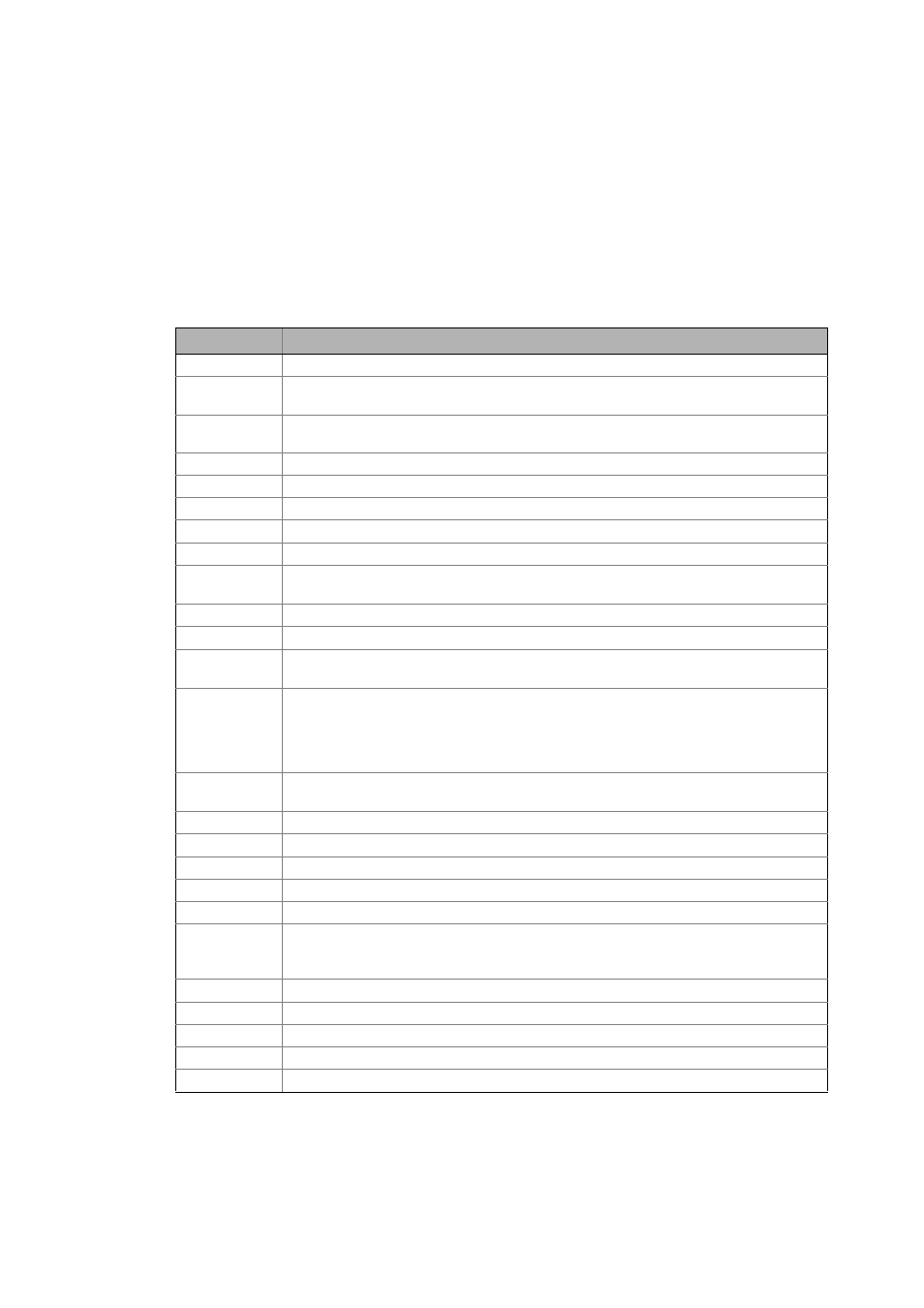
3
User interface
3.1
Control and function elements
28
Lenze · Drive Solution Designer · Manual · DMS 4.2 EN · 12/2013 · TD23
_ _ _ _ _ _ _ _ _ _ _ _ _ _ _ _ _ _ _ _ _ _ _ _ _ _ _ _ _ _ _ _ _ _ _ _ _ _ _ _ _ _ _ _ _ _ _ _ _ _ _ _ _ _ _ _ _ _ _ _ _ _ _ _
• The drawing shows additional information required for a dimensioning process.
• Above the images of the components, important parameters and their values are shown in
tables.
• Below the images of the components, depending on the dimensioning a button is displayed,
via which you can call the diagrams for the component.
3.1.3.1
"Application" image
Symbol
Description
a
max
Max. acceleration of the application
d
dim
Dimensioning diameter
• Diameter which is reached after termination of the acceleration phase.
HW
Winding characteristic (hard/soft), describes the tensile force drop for rewinders as a function
of the reel diameter
J
max
Max. moment of inertia of load
k
f
Tensile force setting range, K
F
= F
max
(d
max
)/F
min
(d
min
)
k
M
Torque setting range, k
M
= M
max
/M
min
l
max
Length of the winding material for a max. reel diameter d
max
and a min. material thickness s
min
m
max,L
Max. mass of the winding material
M
max
Required max. torque of the application
• Is determined from the diagram for the torque.
Mode
Winder control mode
n
av
Average speed of the application
n
max
Max. speed of the application
• Is determined from the diagram for the speed.
P
cto
Base process power of the application used for motor dimensioning
• The base process power is a theoretical value resulting from the max. speed and the max.
torque of the application.
• The base process power often equals the max. required power, since the max. speed and the
max. torque are often required at the same time.
P
max
Required max. power of the application
• Is determined from the diagram for the power.
P
rms,cto
Required thermal power of the motor
q
dim
Dimensioning winding ratio, q
dim
= d
max
/d
min
q
max
Max. winding ratio, q
max
= d
max
/d
min
N(*.dsd)
Number of DSD projects
N
D
Number of drive axes with multi-axis system.
Movement of drive axes
• Axes coordinated
• Axes uncoordinated
t
Crd
Coordinated cycle time
P
mot,max
Max. occurring motor power
P
mot,av
Average power (mean value)
P
gen,av
Required average power of the brake resistor, taking into account the thermal time constant.
P
gen,max
Max. occurring regenerative power