1 mechanical drive axis, 1 lenze gearbox, Mechanical drive axis – Lenze DSD User Manual
Page 283: 10 structure of the drive axis
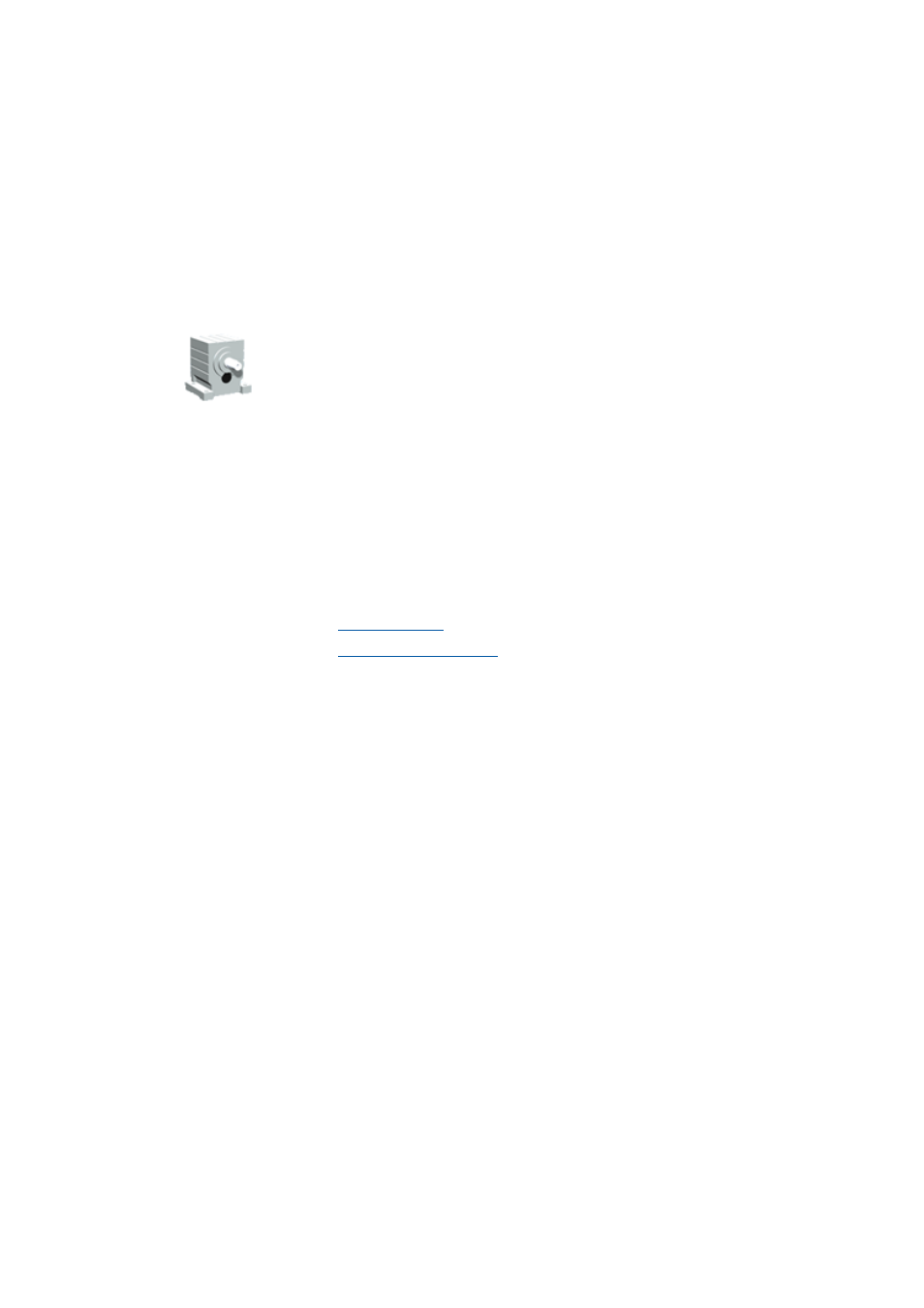
Lenze · Drive Solution Designer · Manual · DMS 4.2 EN · 12/2013 · TD23
283
10
Structure of the drive axis
10.1
Mechanical drive axis
_ _ _ _ _ _ _ _ _ _ _ _ _ _ _ _ _ _ _ _ _ _ _ _ _ _ _ _ _ _ _ _ _ _ _ _ _ _ _ _ _ _ _ _ _ _ _ _ _ _ _ _ _ _ _ _ _ _ _ _ _ _ _ _
10.1
Mechanical drive axis
The mechanical drive axis can consist of the mechanics of the application, a Lenze gearbox, an ad-
ditional drive element, a feedback system, and an electromechanical brake.
10.1.1
Lenze gearbox
Make this selection if the application includes a gearbox.
• If you do not select a Lenze gearbox and additional drive element the mo-
tor is directly connected to the application.
• Direct drive for winders
• If the speeds of the winder and the motor are compatible, the motor is
able to act directly on the reel shaft via a low-backlash clutch.
• For low speeds, multi-pole three-phase AC motors with a rated speed
of approx. 300 ... 500 min
-1
are used.
• Gearboxes for winders
• Generally, winding applications require the transformation of a high
motor speed into a low winding speed. For this task, we recommend
gearboxes with low backlash and low friction, especially if an indirect
tension control via the drive torque is used.
• The motor and the gearbox are selected in later dimensioning steps.