4 motors for winding drives, 10 structure of the drive axis – Lenze DSD User Manual
Page 292
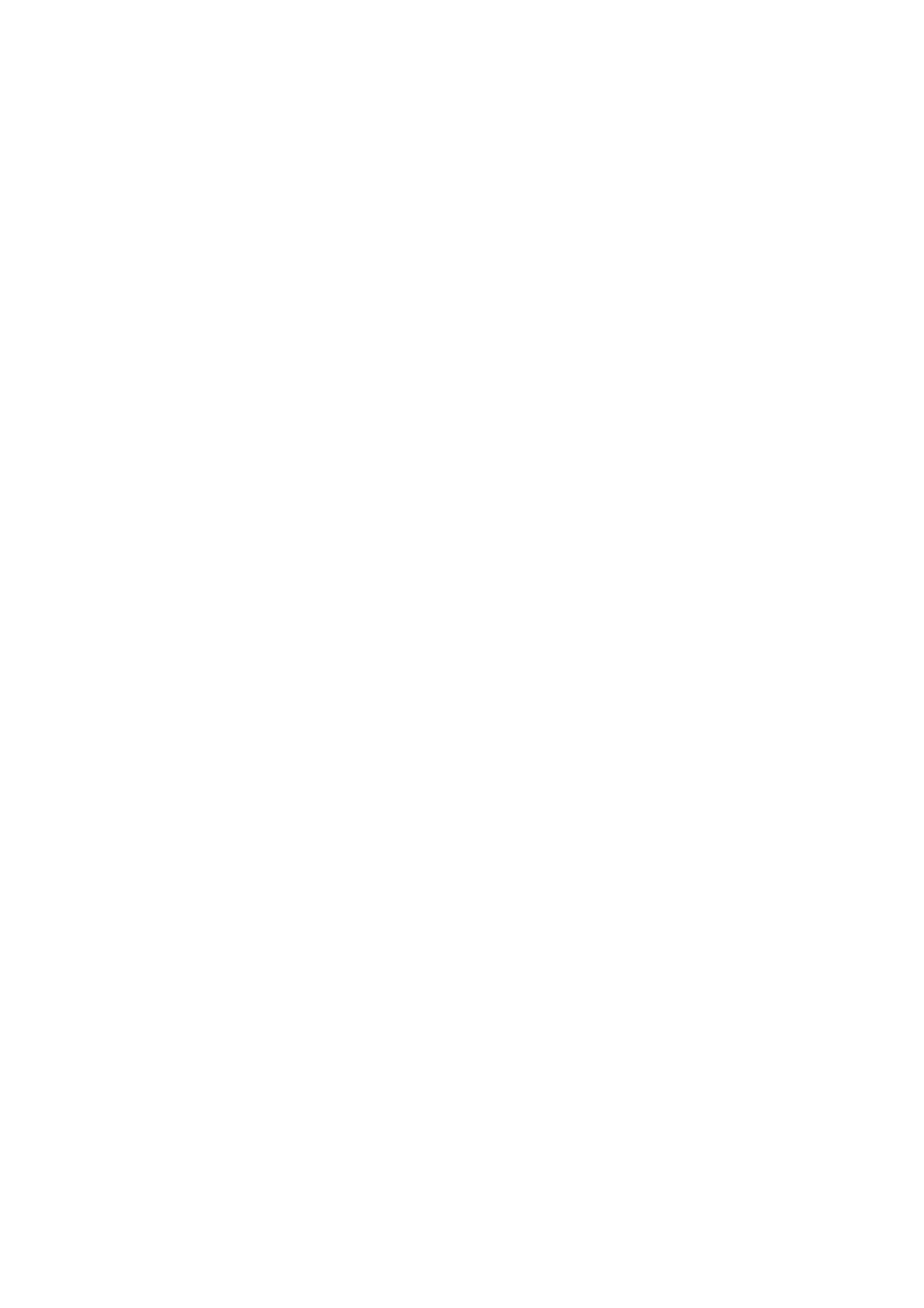
10
Structure of the drive axis
10.3
Drive concept
292
Lenze · Drive Solution Designer · Manual · DMS 4.2 EN · 12/2013 · TD23
_ _ _ _ _ _ _ _ _ _ _ _ _ _ _ _ _ _ _ _ _ _ _ _ _ _ _ _ _ _ _ _ _ _ _ _ _ _ _ _ _ _ _ _ _ _ _ _ _ _ _ _ _ _ _ _ _ _ _ _ _ _ _ _
10.3.2.4
Motors for winding drives
Asynchronous motors
Three-phase asynchronous motors are the standard solution to most winding applications. They are
cost-effective and can be operated in wide ranges of the field weakening without any difficulty. Due
to their high inherent inertia, they are well-suited for handling the high mass inertias of the reel in
the control system in a stable manner.
In combination with belt ratios, asynchronous motors with low rated speeds (higher-pole motors or
4-pole motors with 29-Hz technology) and optimally used field weakening are very well-suited for
many winding applications.
Generally, blowers are required for cooling the motors since the smallest speeds result in the high-
est power loss. DSD checks the thermal motor utilisation.
Synchronous motors
Synchronous servo motors are used if the construction requires compact designs. Synchronous ser-
vo motors are only suitable to a limited extent for torque-controlled drives (indirect tension control)
and for very accurate repeatability of the material tensile force. On the one hand the magnetisation
is strongly temperature-dependent which can be hardly compensated for, and on the other hand
the detent torques have an interfering impact. The achievable field weakening is considerably lower
than with asynchronous motors. The characteristic curve of the motor shows the max. field weak-
ening range.
Tandem motor systems
In case of greater motor powers or very big reels, every side of the winding shaft can be equipped
with a motor. That way, the drive torque is symmetrically shared. Torsions in the winding material
are minimised.
• Two asynchronous motors can be connected in parallel to an inverter without any difficulty and
are hence a cost-effective solution.
• Concepts including two inverters are also possible. The torque division is carried out symmetri-
cally via the control system.
• Synchronous servo motors require one inverter each. A parallel connection of the motors is not
possible.