Motor impedance – Rockwell Automation 7000L PowerFlex Medium Voltage AC Drive (C-Frame) - ForGe Control User Manual
Page 243
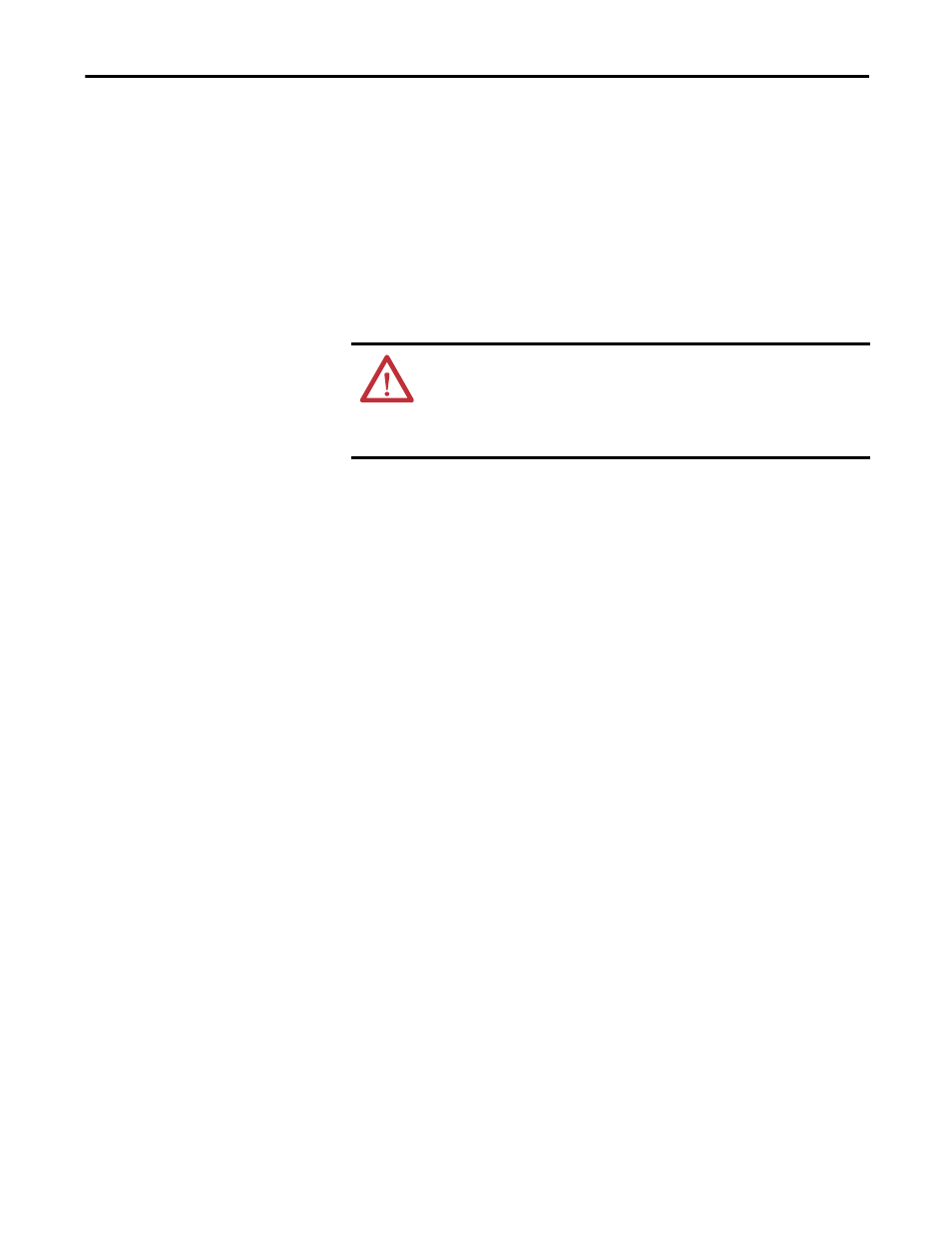
Rockwell Automation Publication 7000L-UM301D-EN-P - June 2014
243
Commissioning
Chapter 4
2. Motor Impedance
The motor impedance tuning function calculates stator resistance
R Stator (129)
and total leakage inductance
L Total Leakage (130) in Motor model Group.
These parameters are used in the reconstruction of the rotor flux. If these
parameters are not adjusted correctly, the resulting distortion in the flux feedback
may cause speed feedback or motor synchronization errors. These parameters
must be tuned during commissioning because it is affected not only by motor
parameters, but also by cable length. The tuning should be done with the motor
stationary.
The following auto-tune procedure can be followed.
Motor Impedance Auto-tuning
1.
Ensure that the motor is stationary. If the motor is turning, the results of
the test may be invalid. It is not necessary to lock the rotor.
2.
Set parameter
Autotune Select in Auto-tuning to Motor Impedance.
3.
Start the drive. In the first half of the test the output frequency is zero and
the dc current is ramped to 0.6pu for a few seconds. This step will calculate
R Stator. After this the current is ramped down to zero.
4.
In the second half of the step the output frequency ramps up to rated
frequency with the dc current equal to 1.0pu for a few seconds. This test
may produce a small amount of motor torque and some rotation may
occur. This step will calculate the
L Total Leakage. The current is ramped
down and parameter
Autotune Select is set to Off.
Parameter
Autotune RStator (219) is set to the measured Stator resistance.
R Stator (129) in Motor Model is set equal to Autotune R Stator. If the test fails or
the values are out of range, a warning is issued indicating the cause of the failure.
Parameter
Autotune LLeakage (220) is set to the measured leakage inductance.
L total leakage (P130) in Motor Model is set equal to Autotune LLeakage. If the
test fails, a warning is issued indicating the cause of the failure.
Following warnings can occur during this test:
R stator High
- this is probably caused by extremely long motor cables increasing
the apparent stator resistance of the motor. The drive cannot operate with stator
resistance greater than 0.50 pu.
ATTENTION: In the following steps, the rotation of the motor in an undesirable
direction may occur. To guard against possible equipment damage, it is
recommended that the motor is disconnected from the load and tested for
direction prior to proceeding, should the equipment be sensitive to reverse
direction rotation.