IAI America MSEP User Manual
Page 240
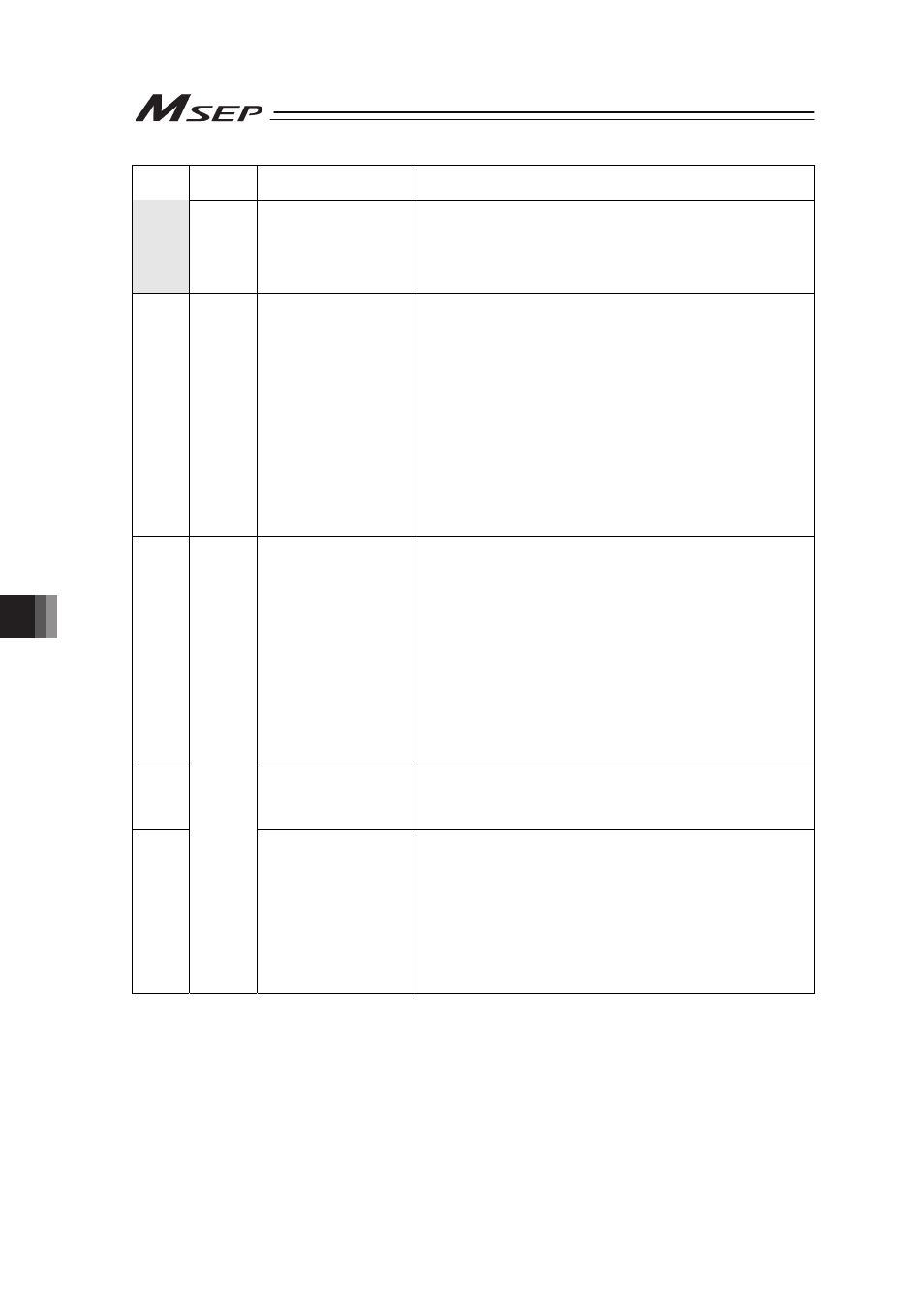
Chapter 6
Troubleshooting
232
Alarm
Code
Alarm
Level
Alarm Name
Cause/Treatment
0D2
Servo
motor
(*)
Only
when
connected
Operation
cancellation
Motor power source
voltage excessive
Cause
: A malfunction of a component inside the controller
can be considered.
Treatment : If this error occurs often, there is a concern of a
controller malfunction. Please contact IAI.
0D4
Cold start
Drive source error
Cause
: 1) Motor power input voltage (input to MPI
terminal) is too large
During acceleration/deceleration and servo-on,
the current consumption rises transiently. Using
the remote sensing function with a power supply
with no enough current capacity may cause
overvoltage responding to the current change.
2) Overcurrent is generated on the motor power
supply line.
Treatment : 1) Check the power voltage input to MPI terminal.
Think to use a power supply with enough current
capacity or not to use the remote sensing
function.
2) Check the wire layout between the actuator and
controller.
0D8
Deviation overflow
Cause
: This alarm indicates that the position deviation
counter has overflowed.
1) The speed dropped or the actuator stopped due
to the effect of external force or overload.
2) The excited-phase detection operation following
the power-on is unstable.
Treatment : 1) This error occurs when the actuator cannot be
operated as it is commanded. Check the load
conditions such as if the work is touching to the
surrounding object, or brake is properly
released, and remove the cause.
2) Overload can be concerned. Revise the
transportable weight and redo the home-return
operation.
0D9
Software stroke limit
exceeded
Cause
: The current position of the actuator exceeds the
software stroke limit.
Treatment : Return the actuator to be within the range of the
software stroke limit.
0DC
Operation
cancellation
Pressing motion range
over error
Cause
: 1) After the pressing operation has complete, the
force to push back is too large and the pushed
back to the pressing start position.
2) The actuator touched the work during the
approach movement before the pressing
movement.
Treatment : 1) Revise the setting and adjust it so the force to
push back gets smaller.
2) Set the “Position” setting in front in the position
table to shorten the approach distance.
(*) Servo motor : RCA, RCA2, RCL Series