IAI America MSEP User Manual
Page 121
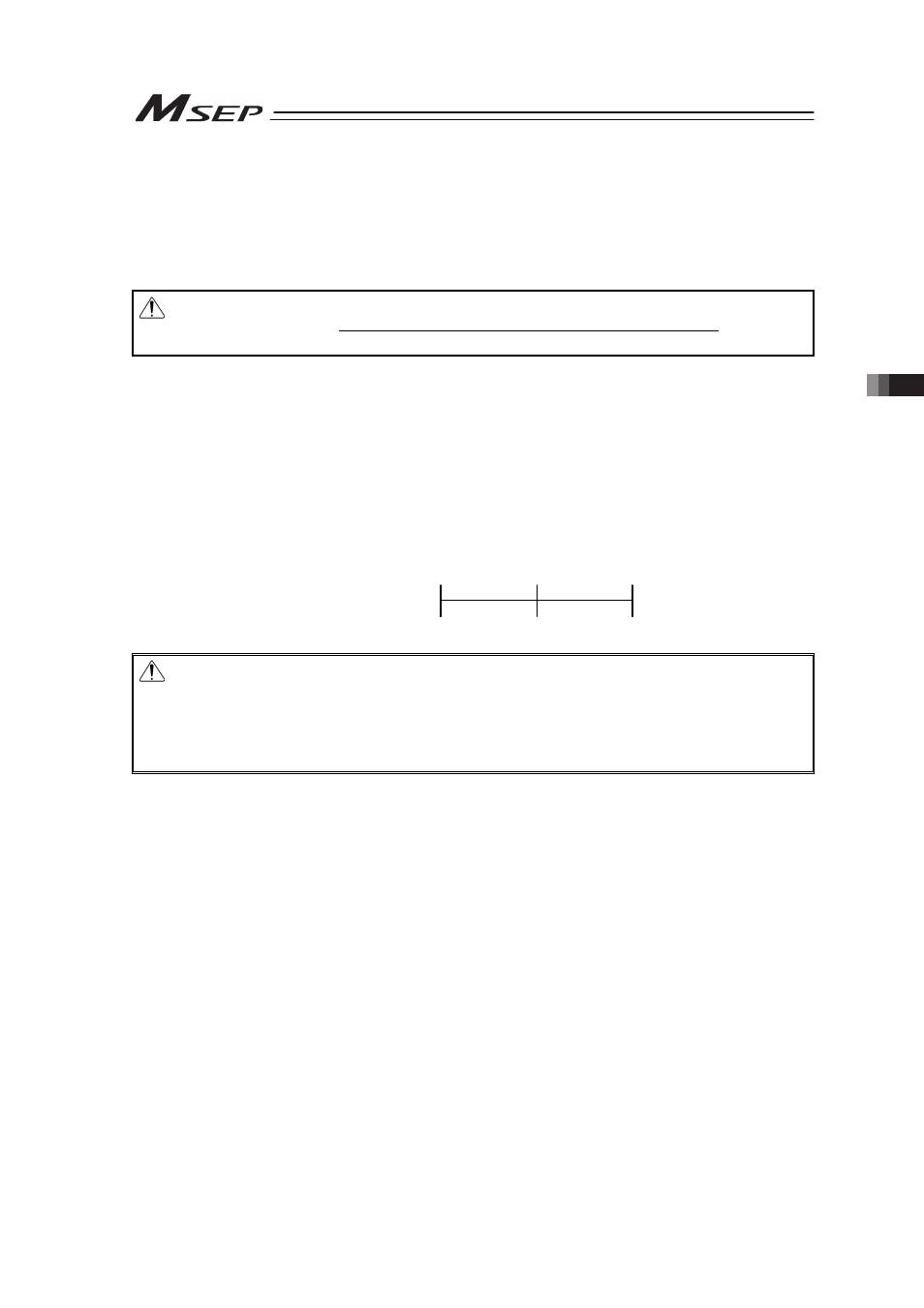
3.4 Fieldbus
Type
Address Map
113
(2) Input and Output Signal Assignment for each Axis
The I/O signals for each axis consists of 8-word for each I/O bit register.
Ɣ The control signals and status signals are ON/OFF signals in units of bit.
Ɣ For the target position and current position, 2-word (32-bit) binary data is available and values
from -999999 to +999999 (unit: 0.01mm) can be used. Negative numbers are to be dealt with
two’s complement.
Caution:
• Set the position data in the range of the soft stroke (0 to effective stroke length) of the
actuator.
Ɣ Set the positioning width. The positioning width is expressed using 2-word (32 bits) binary
data. The figures from 0 to +999999 (Unit: 0.01mm) can be set in PLC.
Ɣ The command speed is expressed using 1-word (16 bits) binary data. The figures from 1 to
+65535 (Unit: 1.0mm/sec or 0.1mm/sec) can be set in PLC. A change of the unit is to be
conducted on Gateway Parameter Setting Tool.
Ɣ The Acceleration/Deceleration is expressed using 1-word (16 bits) binary data. The figures
from 1 to 300 (Unit: 0.01G) can be set in PLC.
Ɣ The pressing current limit value is expressed using 1-word (16 bits) binary data. The figures
from 0 to 100% (0 to FFH) can be set in PLC.
Caution:
Have the setting with values available in the range of for speed, acceleration/deceleration and
pressing current of the actuator. (Refer to the catalog or instruction manual of the actuator.)
Otherwise, it may cause an abnormal condition of the servo or a malfunction of the actuator
such as the alarm codes 0A3 “Position Command Information Data Error”, 0C0 “Excess
Actual Speed”, 0C8 “Overcurrent”, 0CA “Overheated” or 0E0 “Overloaded”.
Ɣ The command current is expressed using 2-word (32 bits) binary data (Unit: 1mA).
Ɣ The current speed is expressed using 1-word (32 bits) binary data (Unit: 1.0mm/sec or
0.1mm/sec).
The unit is the one set in the command speed. A positive number is output when the
revolution of the driving motor is in CCW, while a negative number when CW. Negative
numbers are output with two’s complement.
For Slider and Rod Types of actuators, a negative number is output when a movement is
made towards the motor side, while a positive number when against the motor side. For
Reversed Motor Type, it is the other way around. For Gripper Type, a positive number is
output when fingers are closed. For Rotary Type, a positive number is output when rotating
clockwise.
Ɣ The alarm code is expressed using 1-word (16 bits) binary data.
䎃
Set Value 0
127
H
FF
H
(50 in decimal system) (255 in decimal system)
Pressing current Limit 0%
50%
100%