IAI America MSEP User Manual
Page 224
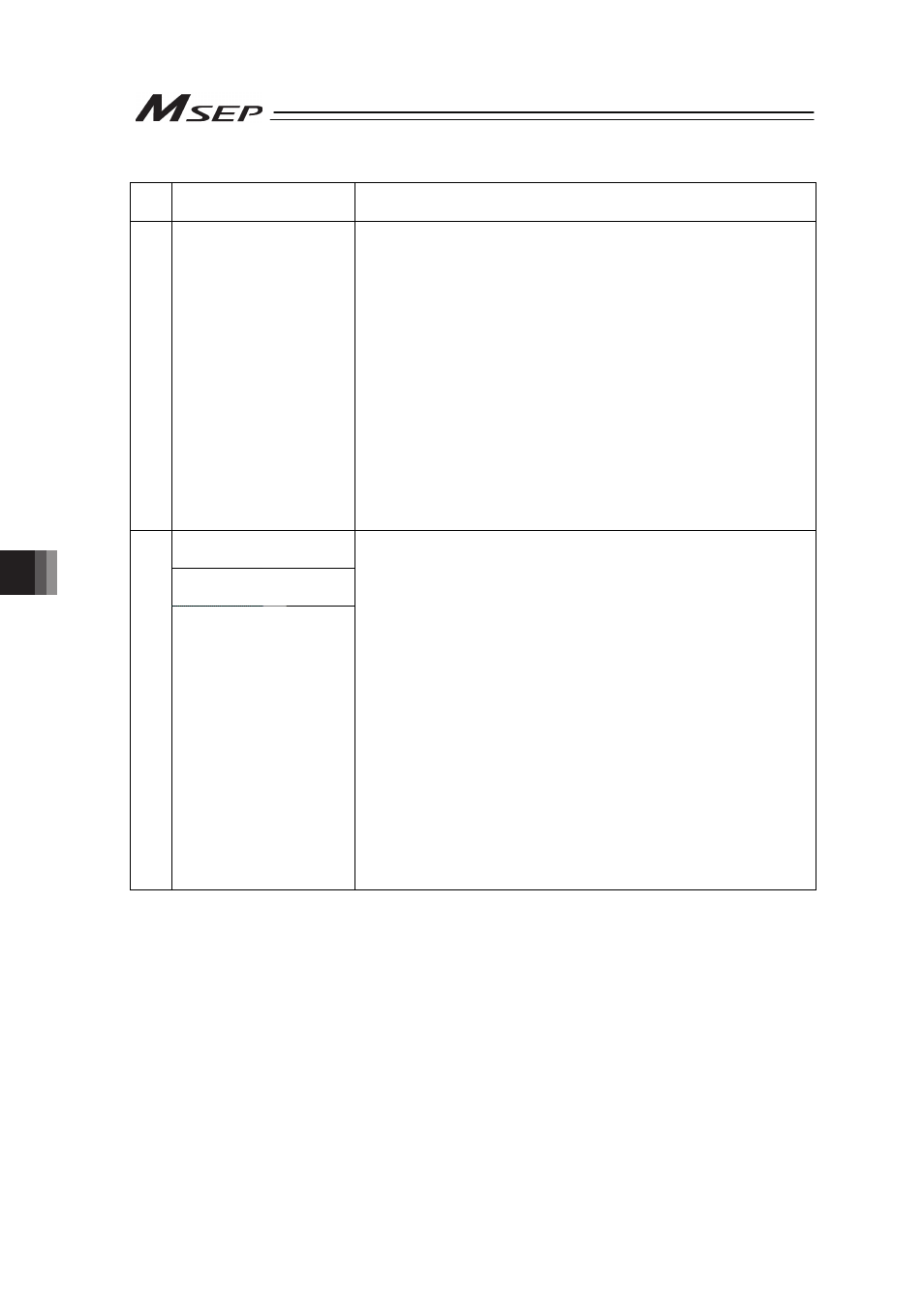
Chapter 5 I/O Parameter
216
No.
Situation that requires
adjustment
How to Adjust
4 Abnormal noise is
generated.
Especially, when stopped
state and operation in low
speed (less than
50mm/sec),
comparatively high noise
is generated.
x
Input the Parameter No.4 “Torque Filter Time Constant”. Try to
increase by 50 as a reference for the setting. If the setting is too
large, it may cause a loss of control system stability and lead the
generation of vibration.
[Important] Prior to Adjustment:
This phenomenon is likely to occur when the stiffness of the
mechanical components is not sufficient. The actuator itself may
also resonate if its stroke is over 600mm or it is belt-driven type.
Before having an adjustment, check if:
1) The value for Parameter No.3 “Servo gain number”, Parameter
No.5 “Speed loop proportional gain”, or Parameter No.6 “Speed
loop integral gain” are excessive.
2) The stiffness of the load is sufficient as much as possible, or the
attachments are not loosened.
3) The actuator unit is mounted securely with a proper torque.
4) There is no waviness on the actuator mounting surface.
Trace precision is desired
to be improved.
Equi-speed performance
is desired to be improved.
5
Response is desired to be
improved.
x
Make the condition optimized with Parameter No.3 “Servo gain
number” and Parameter No.5 “Speed loop proportional gain”
adjusted by referring to the way to adjust stated in No.1 to 3 in
the previous page.
[Reference]
The most important factor is to select the actuator (motor).
The servo is extremely sensitive to the inertia of the load. If the
inertia moment of the load is too large in comparison with the
inertia moment of the servo motor itself, the motor is highly
affected by the load. This may cause the actuator to be
controlled unstably.
Therefore, to improve the precisions of the trace, position, speed
and response of the actuator, the load inertia ratio must be made
small.
For high trace precision, equi-speed performance, and response
of the actuator in such a use as application, it is better to use ball
screws with small leads in the actuator as much as possible and
an actuator of motor capacity higher by at least one level.
The best method is to calculate the load inertia to select the
proper actuator.