IAI America XSEL-S User Manual
Page 53
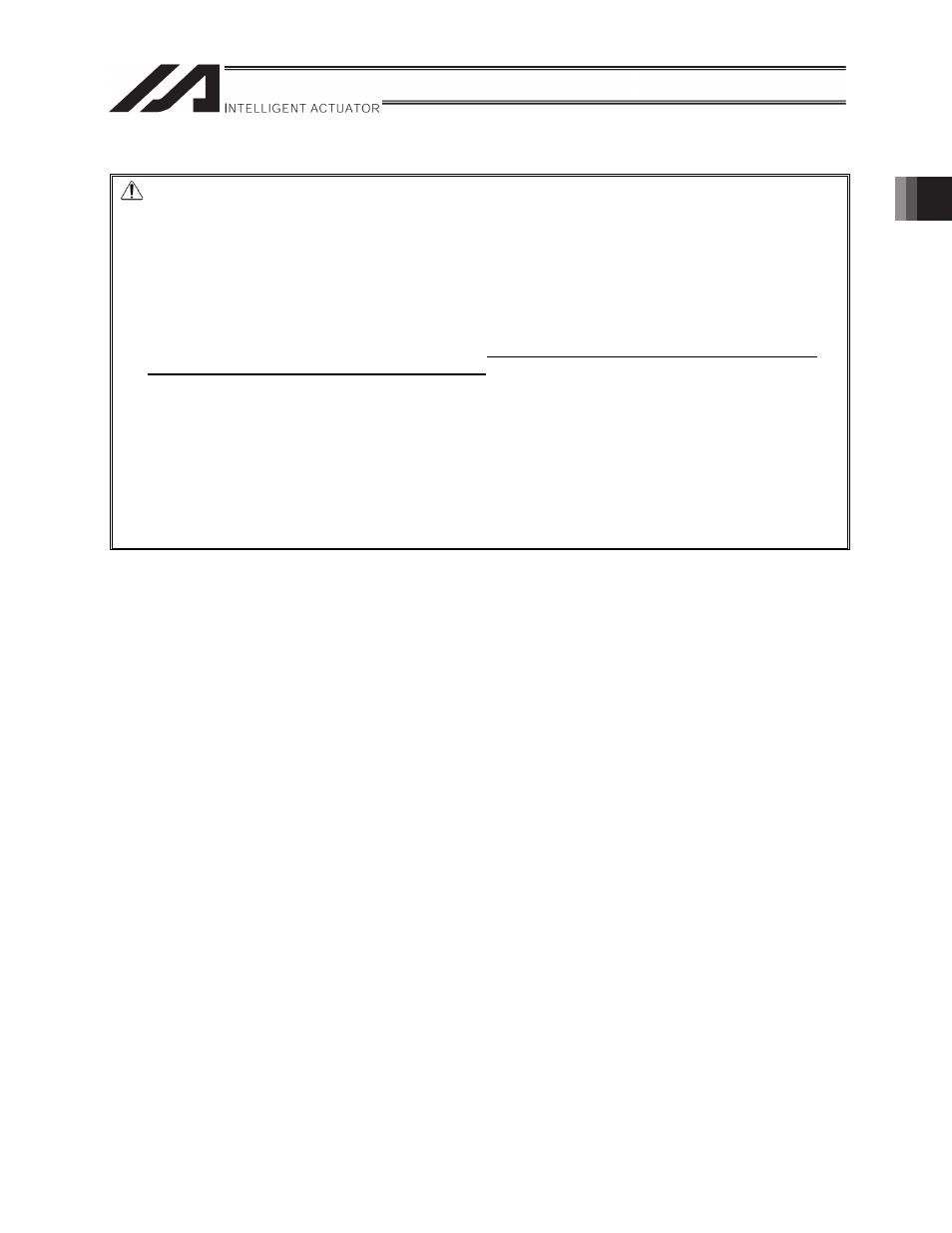
Chapter 2 Operations
45
Caution
(1) The position data for extension motion control board axis shares the user data-hold memory in the
main CPU board as the data saving areas, with the position data for RC axes of the RC gateway
function. For this reason, if the RC gateway function (method of using position data within X-SEL) is
used, some restrictions apply to the number of position data points that can be used. [Refer to “2.6.1
Number of Position Data Points” for the detailed explanation.]
(2) If you use the position data for RC axes with the RC gateway function, back up the position data for
RC axes before changing the parameters above. The position data of the RC gateway function is
cleared when the parameters above are changed. Perform the operations explained in 2.3.3, "Note”
to initialize the memory and reset the software and then transfer the saved backup data to the
controller, write to Flash ROM, and reset the software. [Refer to the section 2.3.2.]
(3) Under normal circumstances, set the same values for I/O parameters No. 530 and No. 532. The
number of set points of I/O parameter No. 530 becomes valid within the data area defined on the
UBM with I/O parameters No. 531 and No. 532. If the value set for I/O parameter No. 530 is smaller
than the value set for I/O parameter No. 532, the 6A1 error does not occur; such setting should be
used when you want to change the number of data points to be used temporarily for debugging
purpose.
[4] Synchronization point type setting of main CPU control master axis (I/O parameter No. 533)
Use this parameter to select the position to which slave axes should follow at synchronous
movement using a main CPU control axis as the master axis. Set “0” (current command position)
or “1” (current position) for each of the main CPU control axes. All axes are set to ”0” (current
command position) at the shipment.
When “0” is specified, slave axes perform synchronous movement to the current command
position of the main CPU control master axis. Since tracking commands of slave axes are output
synchronous with the command position of the main CPU control master axis, following error of
slave axis position to the master axis position can be made smaller.
When “1” is set, slave axes perform synchronous movement to the current position (feedback
value) of the main CPU control master axis. It is possible to synchronize the operation while
checking the current position of the main CPU control master axis, but since a command to
move to the corresponding slave axis position is output after the master axis reaches the current
position, the slave axis position tracking of the master axis potion delays. Select the appropriate
option according to the control specification of the device to be constructed and so on.