Part 1 specification – IAI America REXT User Manual
Page 239
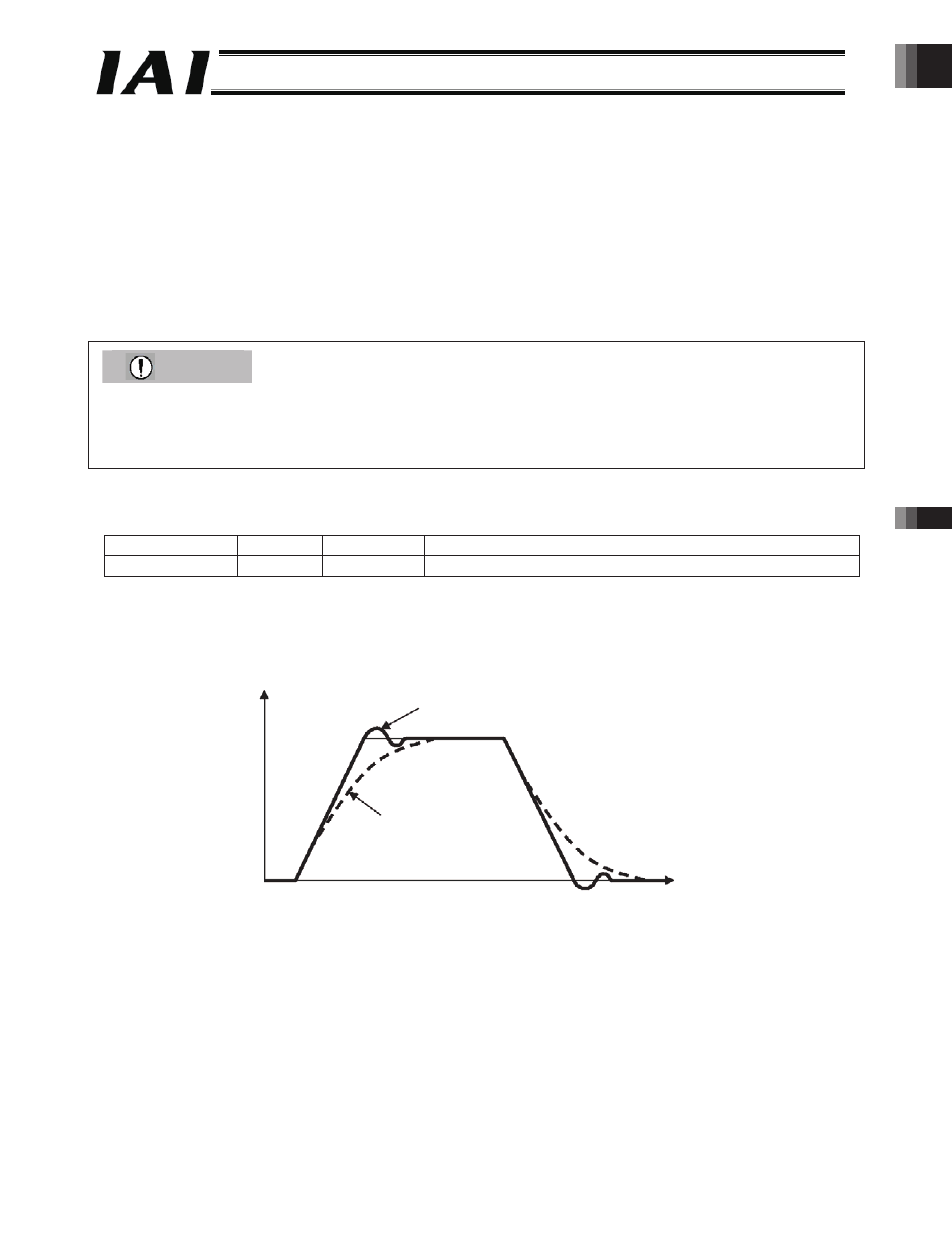
Part 1 Specification
Chapter 4 Controller Unit
215
Part 1 Specification
4.4.5 Parameters Relating to Servo Gain Adjustment
Since the servo has been adjusted at the factory to stabilize positioning operation at the maximum payload capacity of the
actuator, the servo gain need not be changed in normal conditions of use.
In actual use, however, the load condition may not be always ideal (where there is no resonance, vibration, load fluctuation,
etc.)
Accordingly, vibration or noise may occur depending on how the actuator is affixed, load condition, and so on, in which case
servo adjustment will become necessary.
Particularly with custom models (whose ball screw lead or stroke is longer than that of the standard model), vibration/noise
may occur due to external conditions.
In this case, the following parameters must be changed. Contact IAI for details.
Note
Check the following items before performing servo adjustment:
1. Is the load installed in a manner free from looseness, play, etc., and is the load rigidity maximally maintained?
2. Is the actuator installed firmly?
3. Is the actuator mounting surface free from distortion?
z
Servo Gain Number (No. 7, PLG0)
Parameter number
Unit
Input range
Default
7
5 rad/sec
0 to 15
Set individually in accordance with the actuator characteristics.
This parameter determines the level of response with respect to a position control loop.
Increasing the setting value improves compliance with the position command.
However, increasing the setting value too much increases the tendency of the actuator to overshoot.
If the setting value is low, compliance with the position command drops and the positioning time increases as a result.
Speed
Setting value is high (overshoot)
Setting value is low
Time
-239-