Yaskawa MP920 Motion Module User Manual
Page 343
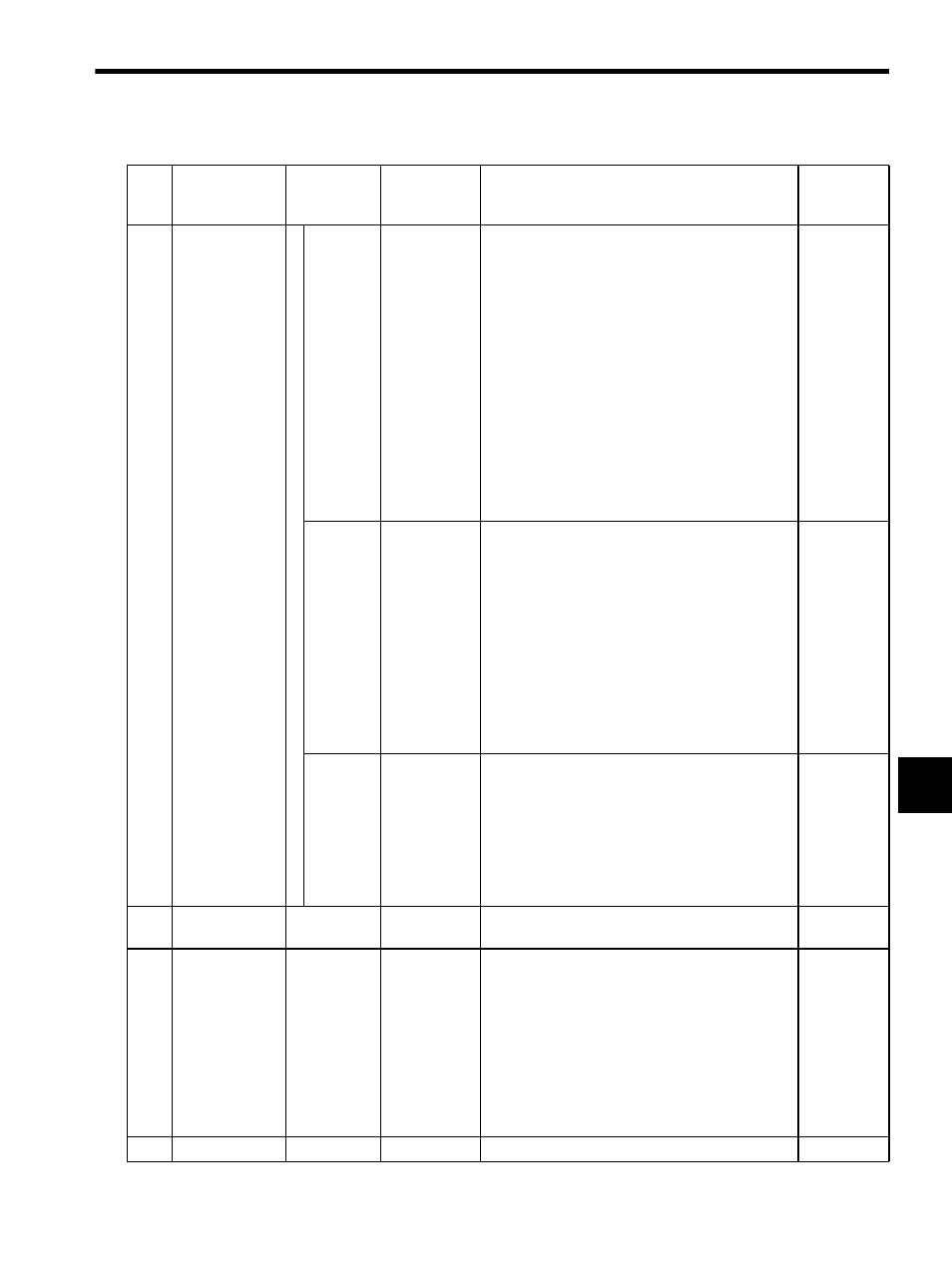
7.3 PO-01 Parameters
7-41
7
2
RUN
Command
Settings
(SVRUNCMD)
(cont’d)
Bit 13
Speed Refer-
ence Value
Selection
(SPDTYPE)
Set speed reference method for feed speed, approach
speed, and creep speed.
It is valid only when an OW20: Motion Com-
mand Code is used in Position Control Mode.
0: OL22
Set speed in reference units and sets rapid traverse
speed at OL22. The setting unit for
OW0A: Approach Speed and OW0B:
Creep Speed are also 1 = 10 reference units/min.
1: OW15
Set speed using a percentage and sets rapid
traverse speed at OL15. The setting unit for
OW0A: Approach Speed and OW0B:
Creep Speed are also 1 = 0.01%.
Refer to Speed Reference in 2.3.1 Prerequisites for
Position Control.
0
Bit 14
Speed Refer-
ence Type
(XREFTP)
Set the data type for OL12.
0: Absolute position method
Sets the absolute position at OL12.
1: Incremental addition method
Adds the current movement amount to the previ-
ous value at OL12 and then sets that data at
OL12.
Note: This is an absolute position method if the
position reference selection is indirectly
specified.
Refer to Position Reference in 2.3.1 Prerequisites
for Position Control.
1
Bit 15
Zero Point
Return Decel-
eration Point
Limit Signal
(LSDEC)
This signal functions as a limit switch signal (decel-
eration LS) when returning to the zero point.
It is valid when bit 2: Limit Switch Signal Selection
is OFF at fixed parameter number 14: Additional
Function Selections.
The external signal (DI signal input by the LIO-01 or
other Module) in the user program must be con-
nected (i.e., programmed) to OB01F.
0
3 to
6
Not used.
OW02 to
OW05
−
Set to “0.”
0
7
Machine Coor-
dinate System
Zero Point
Offset Setting
(ABSOFF)
OL06
-2
31
to 2
31
-1
Position data can be shifted by the value set in this
register. The parameter is valid during RUN opera-
tion, but set it while the system is OFF.
This register contains data used by PO-01 Modules
for position control and the following movements
are affected if this register is set incorrectly. Check to
see if the data is set correctly prior to starting opera-
tion.
Obstructions may damage tools and lead to personal
injury if this check is not performed.
0
9
Not used.
OL08
−
Set to “0.”
0
Table 7.10 Motion Setting Parameters (cont’d)
No. Name
Register
Number
Setting
Range/
Bit Name
Description
Factory
Setting