Supplemental explanation – Yaskawa MP920 Motion Module User Manual
Page 260
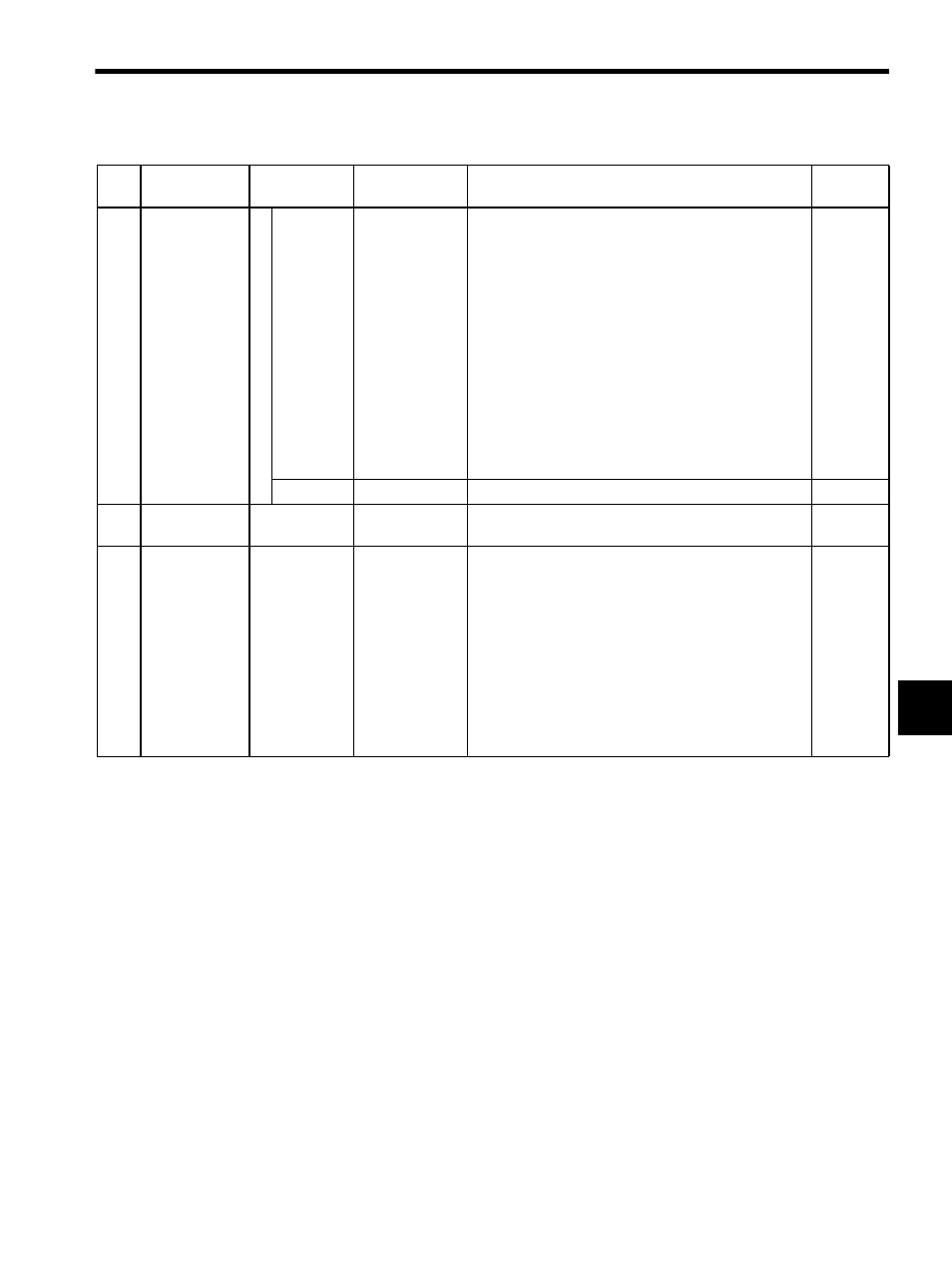
6.2 SVB-01 Parameters
6-25
6
Supplemental Explanation
1. Procedure for Using the Zero Point Offset
a) Applications where Absolute Encoder Rotates in One Direction
The zero point position offset can be used in applications where the absolute encoder
rotates in one direction by using OL06: Zero Point Offset Setting in the motion
parameters and creating a user program that will control the absolute position.
b) Initializing the Absolute Encoder
A pulse cannot be reset within one rotation simply by shorting R-S.
For example, an initial incremental pulse corresponding to 0.5 rotations will be sent
even though the absolute encoder is reset (R-S shorted) if the Servomotor stops at
95.5 rotations.
Consequently, position data corresponding to 0.5 rotations rather than 0 will be indi-
cated at IL08: Position Monitor.
Set the following in order to set the position monitor to 0.
2
RUN Com-
mand Settings
(SVRUNCMD)
(cont’d)
Bit 14
Position
Reference Type
(XREFTYPE)
Set the type of data for OL12 Position Reference Set-
ting when an OW20: Motion Command Code is used
in Position Control Mode.
0: Absolute position method
Sets the absolute position at OL12.
1: Incremental addition
Adds the current movement value to the previous
value at OL12 and then sets that data at
OL12.
Note: 1. Only the absolute position method can be set
if the position reference selection is indirectly
specified.
2. Select the incremental addition method when
moving an axis by using a motion program.
1
Bit 15
Not used.
Set to “0.”
0
3 to
6
Not used.
OW02 to
OW05
−
Set to “0.”
0
7
Machine Coor-
dinate System
Zero Point Off-
set Setting
(ABSOFF)
OL06
-2
31
to 2
31
-1
Position data can be shifted by the value set in this regis-
ter. See 1 of Supplemental Explanation below.
The parameter is valid during RUN operation, but set it
while the system is OFF.
This register contains data used by SVB Modules for
position control and the following movements are
affected if this register is set incorrectly. Check to see
if the data is set correctly prior to starting operation.
Obstructions may damage tools and lead to personal
injury if this check is not performed.
See 2 of Supplemental Explanation below.
0
Table 6.3 Motion Setting Parameters (cont’d)
No.
Name
Register
Number
Setting Range/
Bit Name
Description
Factory
Setting