Initial settings, Feedback position calculation, Execute out-of-step detection calculation – Yaskawa MP920 Motion Module User Manual
Page 330
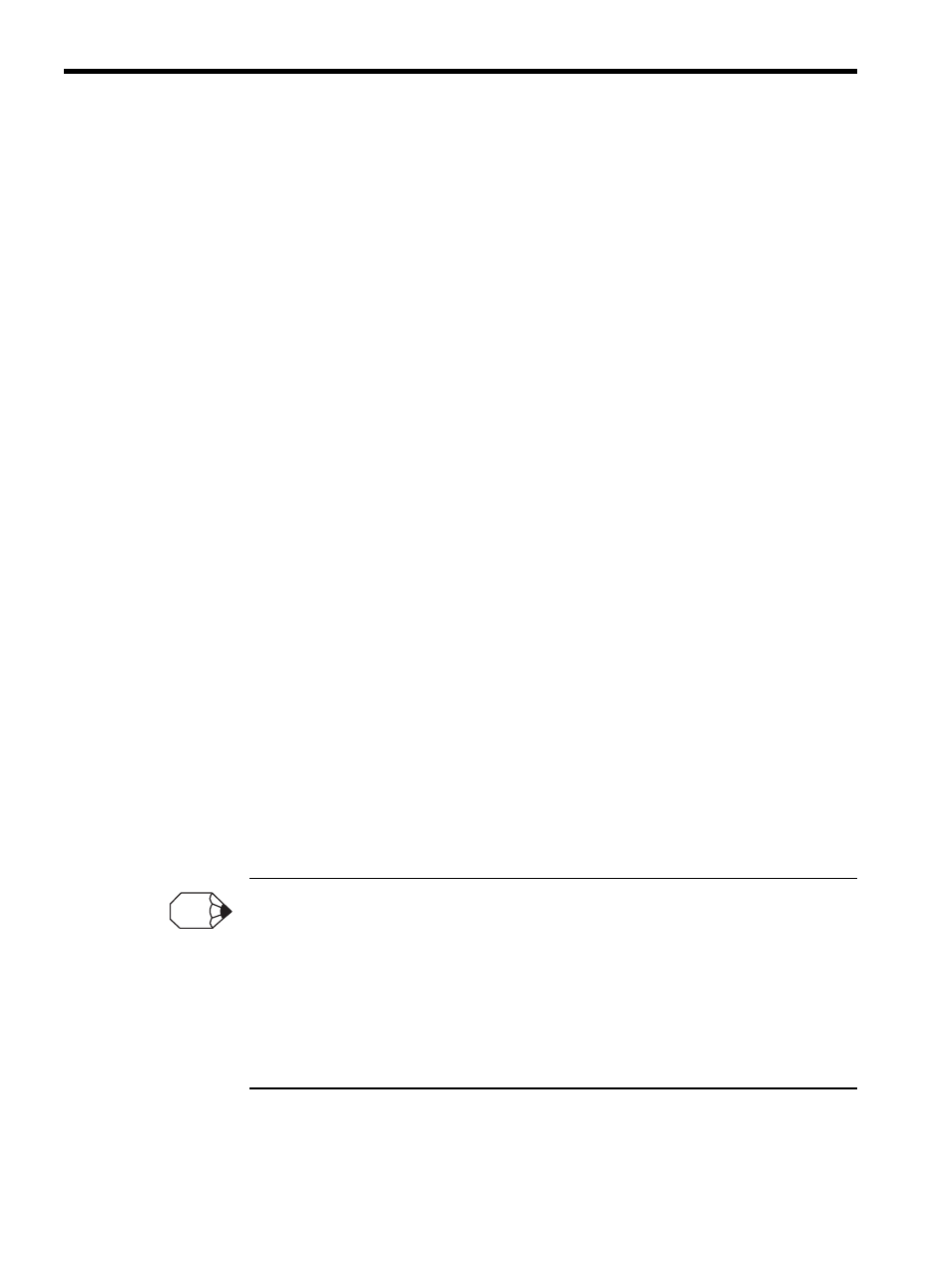
7 PO-01 Module Specification and Handling
7.2.4 Out-of-step Detection
7-28
The example application program shown on the previous page is briefly explained below.
Initial Settings
The following initial settings are set when out-of-step detection is OFF (MB000000 is OFF).
Create a separate application program for out-of-step detection ON/OFF timing.
• Calculated feedback position (DL00000) = 0
• Remainder from the calculated feedback position calculation (DL00002) = 0
• DL00004 = Encoder pulse multiplier (n)
× number of encoder pulses per Servomotor
rotation (N)
Note: The encoder pulse multiplier (n) = 4 and the number of encoder
pulses per Servomotor rotation (N) = 2000 in this particular example,
but use settings appropriate for your machine.
• Reference position (DL00010) = 0
Feedback Position Calculation
The feedback position (P
i
) is calculated from the following: The input data for the Counter
Module (number of pulses per scan: IL1002), the number of reference pulses per Servomo-
tor rotation (M), the encoder pulse multiplier (n), and the number of reference pulses per
Servomotor rotation (M).
Note: The number of reference pulses per Servomotor rotation (M) = 2000
in this particular example, but use settings appropriate for your
machine.
Execute Out-of-step Detection Calculation
If the absolute difference between the reference position (M
i
) and the calculated feedback
position (P
i
) exceeds the error width (
ε), then the situation is considered out of step and
OB00000 turns ON.
Note: The error width (
ε) = 200 in this particular example, but use settings
appropriate for your machine.
Guidelines for Setting Error Width
Set the error width to four times the number of output pulses per scan when the Servomotor is running
at the rated motor speed (rpm).
• NR: Rated motor speed (rpm)
• Ts: High-speed scan setting (ms)
We get the following result if NR = 300 (rpm), the number of reference pulses per Servomotor rotation
= 2000 pulses, and Ts = 5.
•
ε = { (300 × 2000 × 5) ÷ (60 × 1000) } × 4 = 200
INFO