Idle speed and top no-load speed, Chapter 2- drive system: cvt and transfer case – Cub Cadet 4 x 4 Volunteer User Manual
Page 15
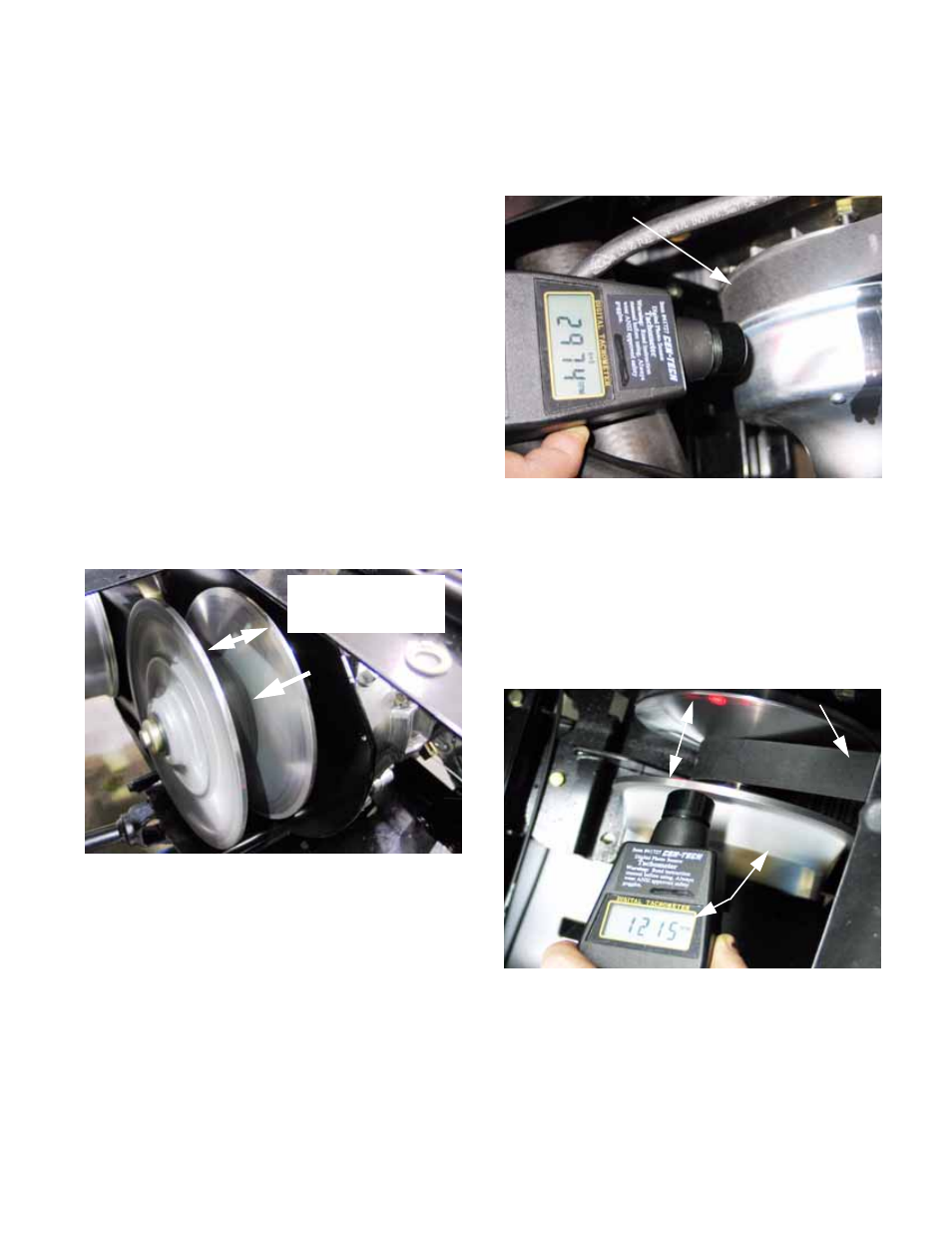
Chapter 2- Drive System: CVT and Transfer Case
11
•
The further the drive point (contact patch
between the belt and the sheaves) is from the
crankshaft, the greater the effective circumfer-
ence of the driving pulley (element).
•
The greater the effective circumference of the
driving pulley, the more linear motion is trans-
ferred to the belt for each crankshaft revolution.
•
This increases the drive speed, but reduces the
amount of torque the engine transfers to the
drive system.
•
If the engine is over-loaded by a combination of
grade and cargo weight while operating at full
throttle, the RPMs will be pulled-down. As the
engine RPMs are reduced, the drive ratio will
automatically shift in the numerically higher
direction, increasing the amount of torque avail-
able to the wheels, at the expense of ground
speed.
5d. As the belt is forced outward on the
sheaves of the driving element, the driven
element spread allowing the belt to be
drawn deeper-in. See Figure 2.5.
5e. As the belt is drawn deeper into the driven
pulley, two things are accomplished:
•
Belt tension is held constant, even though the
effective size of the driving pulley changes.
•
The range of available drive ratios is widened.
Figure 2.5
Driven pulley at speed
Belt deep in sheaves
Belt
Sheaves
5f. At about 3,000 RPM (Kohler) or 2,500
RPM (Caterpillar) the driving element
reaches the end of its travel.
See Figure 2.6.
•
Any increase in vehicle speed beyond the end of
CVT travel is due only to an increase in engine
speed. The rate of vehicle acceleration will
level-off.
IDLE SPEED AND TOP NO-LOAD SPEED
1.
The Kohler and CAT engines should idle at
1,200 RPM. See Figure 2.7.
Figure 2.6
Driven element fully
drawn together:
Belt at outer
edge
Figure 2.7
Belt still
spread
Sheaves
Clutch spinning
at idle speed