Function library – Lenze 8200 motec frequency inverter 0.25kW-7.5kW User Manual
Page 83
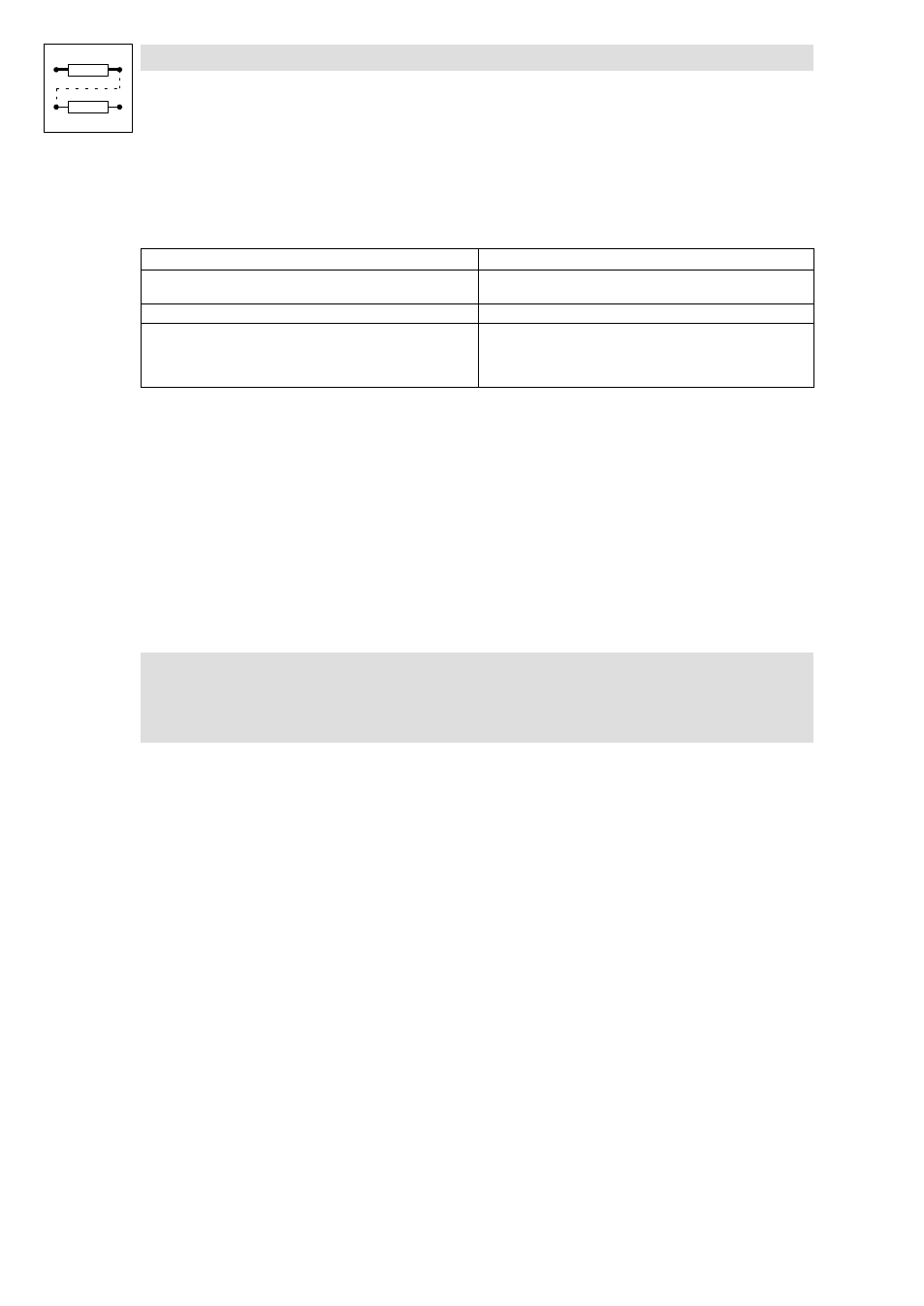
Function library
Selection of control mode, optimisation of operating behaviour
7−12
L
EDB82MV752 EN 5.2
Optimising the sensorless torque control
In general, the sensorless torque control is ready for operation after the motor parameters have been
identified. The drive performance can be optimised by manually setting several parameters:
12
Drive performance
Remedy
Torque is not constant
Reduce motor inductance (C0092) by approx. 10 ... 20 %.
Idle current and maximum current decrease.
Drive does not accelerate from standstill
Raise the torque setpoint to 20 ... 25 %.
Controller is not able to follow the quick load changes
Adapt gain C0077) and adjustment time (C0078) of the I
max
-controller:
·
Reduction of C0078 = I
max
controller becomes quicker (more
dynamic)
·
Increase of C0078 = I
max
controller becomes slower ("smoother")
Tip
·
The minimum torque setpoint must not fall below 10 % (setting range 1 : 10).
·
The motor may stall at operation with output frequencies < 3 Hz. If so, reset the internal
control by quickly switching the controller inhibit.
·
If C0412/6 is combined with an analog signal source it is possible to display the torque
setpoint under C0047.
·
If C0412/6 is not combined with an analog signal source (FIXED−FREE) it is possible to select
the torque setpoint under C0047. Please note:
– When disconnecting the mains, the value set will be lost!
– Before enabling the controller it is absolutely necessary at the restart to select the correct
setpoint under C0047. Otherwise the drive would start with the maximum torque.
)
Note!
In the control modes "V/f characteristic control" and "vector control" the signal
combined with C0412/6 or C0047 act as a torque limitation.