Function library – Lenze 8200 motec frequency inverter 0.25kW-7.5kW User Manual
Page 80
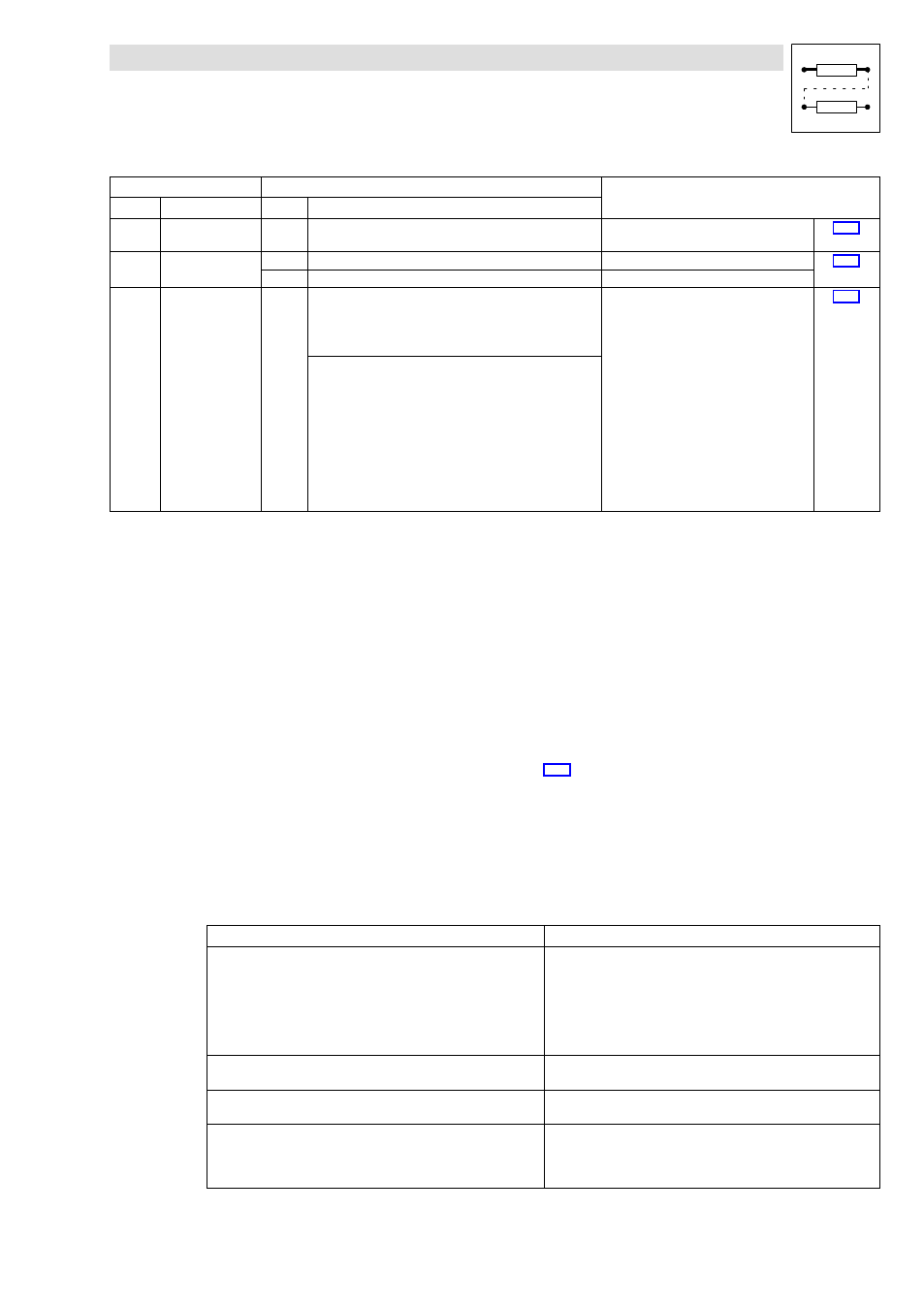
Function library
Selection of control mode, optimisation of operating behaviour
7−9
L
EDB82MV752 EN 5.2
Code
IMPORTANT
Possible settings
No.
Selection
Lenze
Name
C0091
Motor cos
ϕ
а
0.40
{0.1}
1.0
а
Depending on the controller
^ 7−48
C0092
Motor stator
inductance
0.0
0.000
{0.1 mH}
200.0
^ 7−48
0.00
0.00
{0.01 mH}
200.00 Only 8200 vector 15 ... 90 kW
C0148*
s
Motor parameter
identification
0
0
Ready
Only when the motor is cold!
1. Inhibit controller, wait until drive is at
standstill
2. Enter the correct motor data under
C0087, C0088, C0089, C0090, C0091
(see motor nameplate).
3. Set C0148 = 1 by
v
4. Enable controller
The identification
– starts,
c
goes off
– the motor makes a high−pitched tone,
but does not rotate!
– takes approx. 30 s
– is completed when
c
is on again
5. Inhibit controller
^ 7−48
1
Start identification
·
V/f−rated frequency (C0015), slip
compensation (C0021) and motor stator
inductivity (C0092) are calculated and saved.
·
The motor stator resistance (C0084) = total
resistance of motor cable and motor is
measured and saved
Setting of vector control
Use C0014 = 4 to set the operating mode "vector control".
Preparing motor parameter identification
You must enter the motor data of the motor nameplate:
·
Rated motor speed (C0087)
·
Rated motor current (C0088)
·
Rated motor frequency (C0089)
·
Rated motor voltage (C0090)
·
Motor cos
j (C0091)
Motor parameter identification
Carry out the motor parameter identification. (
^ 7−48
)
Automatically detected parameters
V/f−rated frequency (C0015), slip compensation (C0021) and motor stator inductivity (C0092) are
calculated and saved. The total resistance of motor cable and motor is measured and saved as
motor stator resistance (C0084).
Optimising the vector control
In general, the vector control is ready for operation after the motor parameters have been identified.
Vector control must only be optimised for the following drive performance:
11
Drive performance
Remedy
Rough motor run and motor current (C0054) > 60 % rated motor
current in idle running (stationary operation)
1. Reduction of motor inductance (C0092) by 10 %
2. Check of motor current under C0054
3. If the motor current (C0054) > 50 % of the rated motor current:
– C0092 must be reduced until the motor current amounts to 50 %
of the rated motor current
– Reduce C0092 by max. 20 %!
– Note: If you reduce C0092 the torque will decrease!
Torque too low for frequencies f < 5 Hz (starting torque)
Increase of motor resistance (C0084) or increase of motor inductance
(C0092)
Poor constant speed at high loads (setpoint and motor speed are not
proportional).
Increase of slip compensation (C0021)
Overcompensation results in drive instability!
Error messages OC1, OC3, OC4 or OC5 during acceleration times
(C0012) < 1 s (drive controller is no longer able to follow the dynamic
processes)
Change reset time of the I
max
controller (C0078):
·
Reduction of C0078 = I
max
controller becomes quicker (more
dynamic)
·
Increase of C0078 = I
max
controller becomes slower ("smoother")