Safety instructions – Lenze 8200 motec frequency inverter 0.25kW-7.5kW User Manual
Page 13
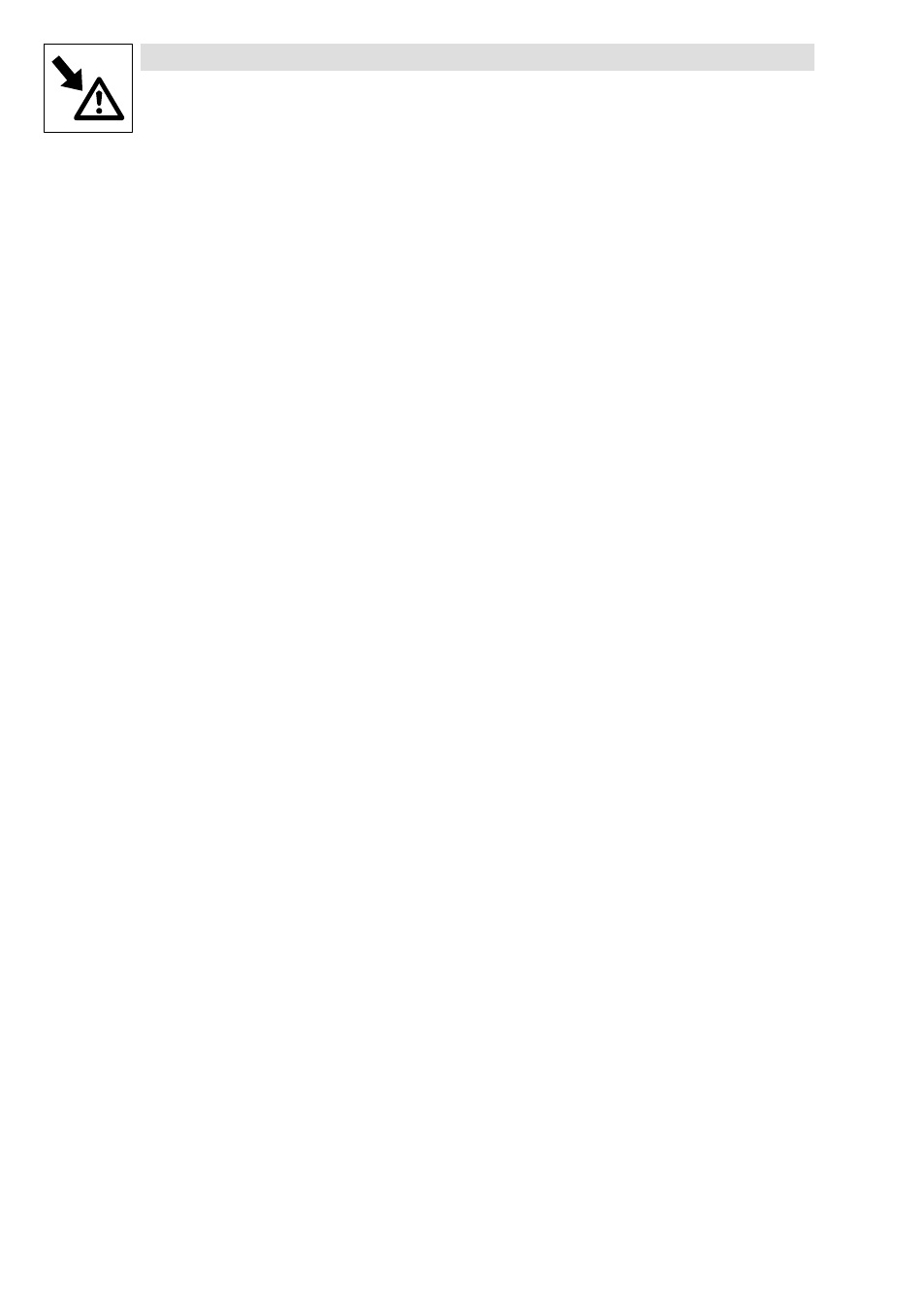
Safety instructions
Lenze low−voltage machinery
2−4
L
EDB82MV752 EN 5.2
Electrical connection
All operations must only be carried out by qualified and skilled personnel on the low−voltage machine
at standstill and deenergised and provided with a safe guard to prevent an unintentional restart.This
also applies to auxiliary circuits (e. g. brake, encoder, blower).
Check safe isolation from supply!
If the tolerances specified in EN 60034−1; IEC 34 (VDE 0530−1) − voltage ±5 %, frequency ±2 %,
waveform, symmetry − are exceeded, more heat will be generated and the electromagnetic
compatibility will be affected.
Observe the data on the nameplate, operating notes, and the connection diagram in the terminal box.
The connection must ensure a continuous and safe electrical supply (no loose wire ends); use
appropriate cable terminals. The connection to the PE conductor must be safe. The plug−in
connectors must be bolt tightly (to stop).
The clearances between blank, live parts and to earth must not fall below 8 mm at U
r
£ 550 V, 10 mm
at U
r
£ 725 V, 14 mm at U
r
£ 1000 V.
The terminal box must be free of foreign particles, dirt and moisture. All unused cable entries and the
box itself must be sealed against dust and water.
Commissioning and operation
Before commissioning after longer storage periods, measure insulation resistance. In case of values
£ 1 kW per volt of rated voltage, dry winding.
For trial run without output elements, lock the featherkey. Do not deactivate the protective devices,
not even in a trial run.
Check the correct operation of the brake before commissioning low−voltage machines with brakes.
Integrated thermal detectors do not provide full protection for the machine. If necessary, limit the
maximum current. Parameterise the controller so that the motor will be switched off with I > I
r
after
a few seconds of operation, especially at the risk of blocking.
Vibrational severities v
eff
£ 3.5 mm/s (P
r
£ 15 kW) or 4.5 mm/s (P
r
> 15 kW) are acceptable if the
clutch is activated.
If deviations from normal operation occur, e.g. increased temperatures, noises, vibrations, find the
cause and, if required, contact the manufacturer. In case of doubt, switch off the low−voltage
machine.
If the machine is exposed to dirt, clean the air paths regularly.
Shaft sealing rings and roller bearings have a limited service life.
Regrease bearings with relubricating devices while the low−voltage machine is running. Only use the
grease recommended by the manufacturer. If the grease drain holes are sealed with a plug, (IP54
drive end; IP23 drive and non−drive end), remove plug before commissioning. Seal bore holes with
grease. Replace prelubricated bearings (2Z bearing) after approx. 10,000 h − 20,000 h, at the latest
however after 3 − 4 years.
The product−specific safety and application notes given in these instructions must be
observed!