Application examples – Lenze 8200 motec frequency inverter 0.25kW-7.5kW User Manual
Page 197
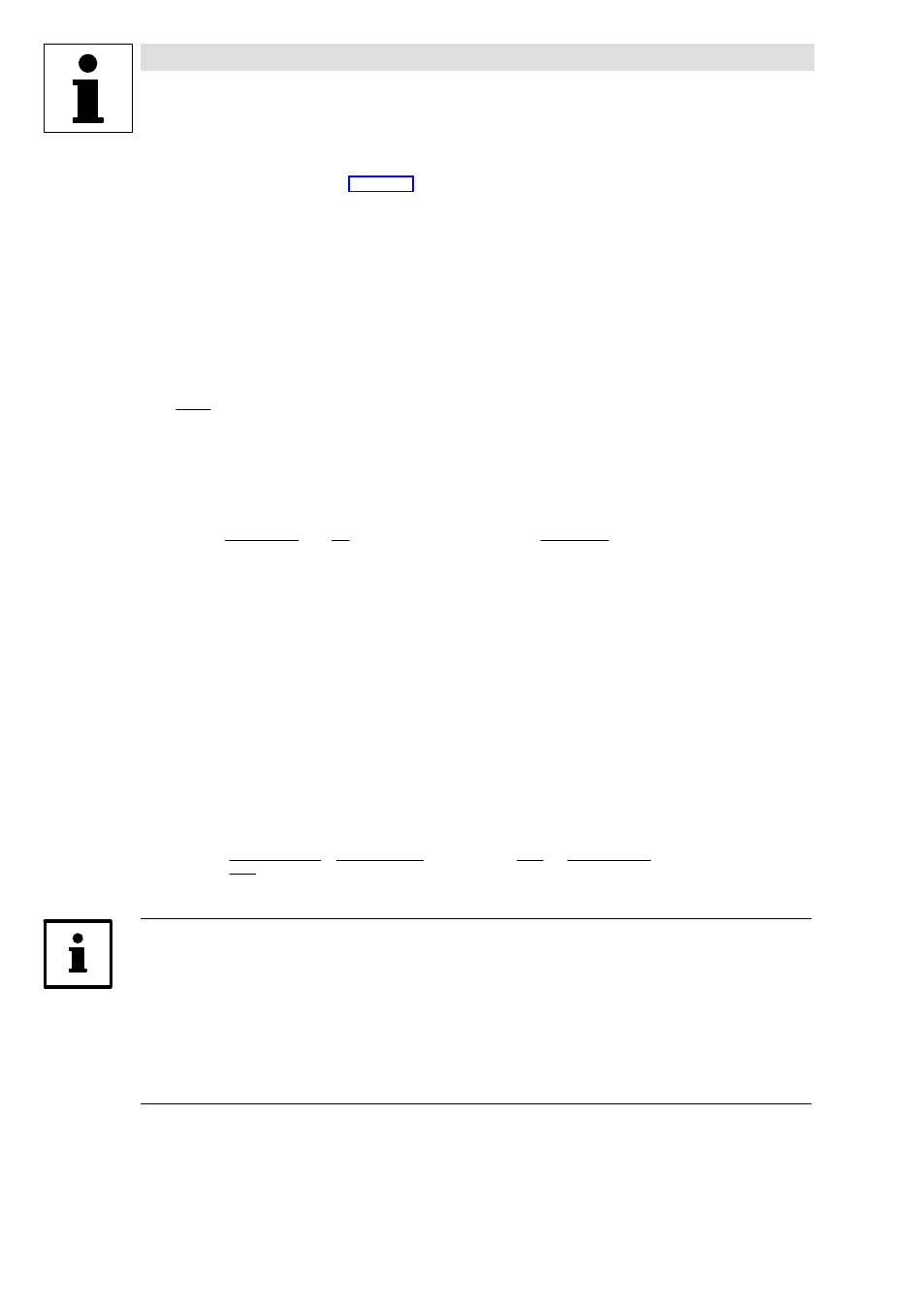
Application examples
Speed control
13−12
l
EDB82MV752 EN 5.2
Adjustment (see example in Fig. 13−4)
Basic conditions
·
A four−pole motor is to be operated up to n
max
= 1500 rpm. The motor has the following data:
– Rated speed n
r
= 1390 rpm
– Rated frequency f
r
= 50 Hz
– Slip s
N
= 7.3 %
– Slip frequency f
s
= 3.7 Hz
·
The pulse encoder supplies 6 increments/revolution (inc/rev).
– Thus, the maximum frequency at X3/E1 with maximum speed amounts to:
1500
60 s
@ 6 + 150 Hz
·
Set process controller influence (C0074) to 200% rated slip:
– C0074 = 14.6 %
·
Calculate maximum output frequency (C0011):
ǒ
1
)
C0074 [%]
100
Ǔ
@
p
60
@ n
max
[min
*1
]
+ 1.15 @ 2 @ 1500
60
+ 57.5 Hz
Adjustment of frequency input X3/E1
·
C0425 = −0−
– Normalisation frequency =100 Hz
– Maximum frequency = 300 Hz
·
Activate the frequency input with C0410/24 = 1.
– Ensure that no other digital signal is linked with E1 (no double assignment)!
·
Link the frequency input with the actual process controller value in C0412 (C0412/5 = 2)
·
Gain C0426
– The input frequency at X3/E1 is normalised to the value of the preselected frequency
(100 Hz), i.e. 100 Hz correspond internally to the output frequency set in C0011.
– Every time C0011 is changed, C0426 must be adapted.
C0426
+
f
N
(C0425)
nmax
60 s
@ incńrev
@
C0011
* f
s
C0011
@ 100 % + 100
150
@ 57.5 * 3.7
57.5
@ 100 % + 62.4 %
Tip!
If the number of increments per revolution of the encoder is not known, the gain to be set must be
determined by experiment:
1. Set C0238 = 0 or 1.
2. Accelerate the drive the maximum desired output frequency. The output frequency is now only
determined via the frequency feedforward control.
3. Set the gain via C0426 so that the actual value (C0051) corresponds to the setpoint (C0050).