3 derivative action (td), 4 controller pid loop tuning, Table 16-2. trial and error tuning method – Micromod Micro-DCI: 53MC5000 Multi-Loop Process Controller Instruction Manual User Manual
Page 299
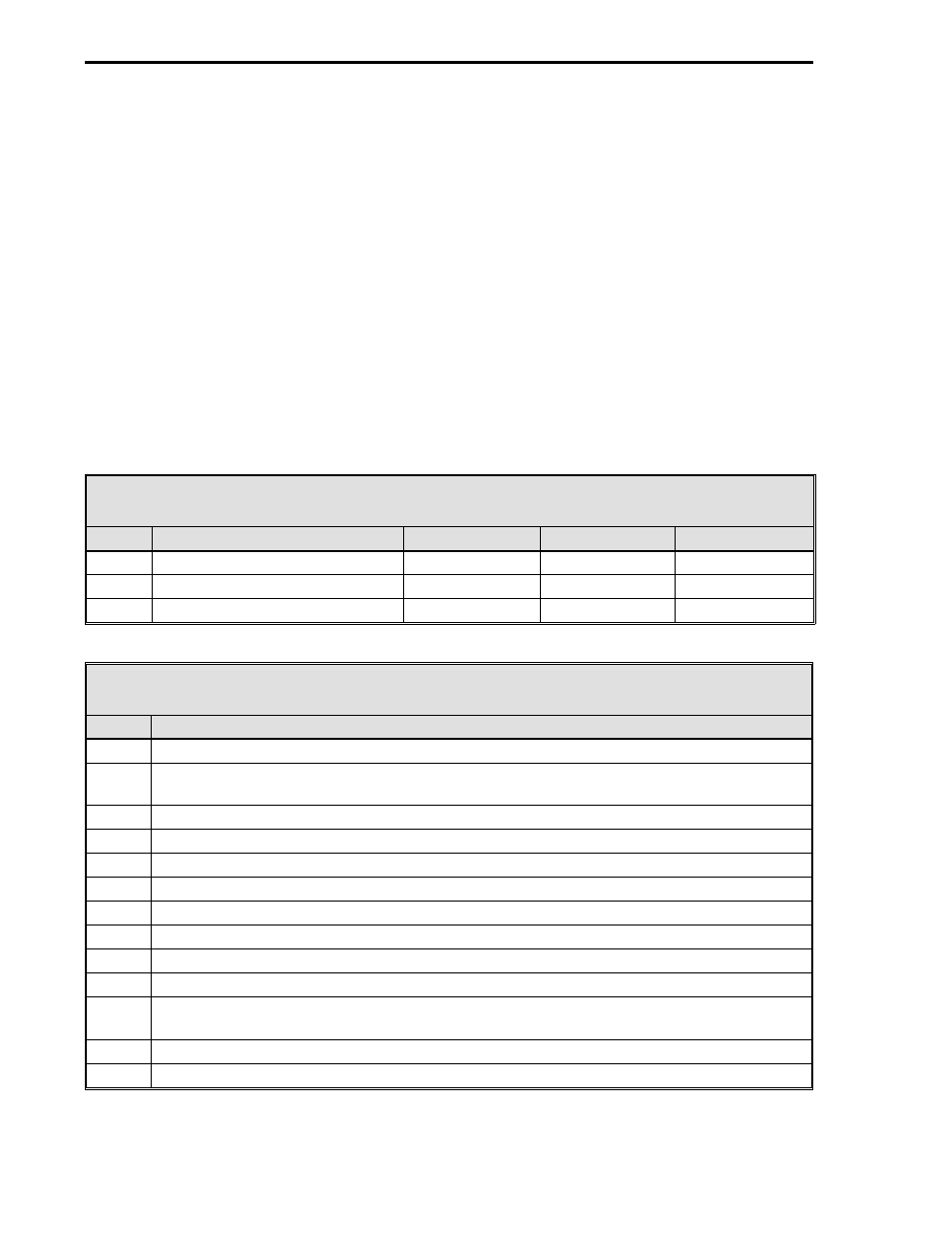
16.3 DERIVATIVE ACTION (TD)
Derivative action augments proportional action by responding to the rate of change of the process
variable. It is used to make each controller PID loop more responsive to sudden process
disturbances. The datapoints to set the Rate parameters for CON0 through CON3 are C108,
C144, C180, and C216; they each have a default value of 0 minutes. The minimum value for de-
rivative action is 0.01 minutes and the maximum value is 8 minutes; 0 is off. The derivative time in
minutes is the amount of time by which the proportional action (or proportional plus integral action)
is advanced.
16.4 CONTROLLER PID LOOP TUNING
Table 16-1 provides summary information for the tuning parameters referenced in the three tuning
methods that follow. The Trial and Error Method (Table 16-2) is usually preferred for process
loops that respond quickly, requiring no waiting to determine steady cycling process conditions.
The Proportional Cycle Method (Table 16-3) and Step Response Method (Table 16-4) are expedi-
ent procedures for slow processes. See Figure 16-1 for the Step Response Method Curve.
Table 16-1. Summary Information for Tuning Parameters
Abbr.
Datapoint (CON0, 1, 2, 3)
Min. Affect
Max. Affect
Parameter
P.B.
C106, C142, C178, C214
1000%
2%
Proportional Band
TR
C107, C143, C179, C215
200 min/rep.
0.02 min/rep.
Reset
TD
C108, C144, C180, C216
0.01 minutes
8 minutes
Rate
Table 16-2. Trial and Error Tuning Method
Step
Procedure
1
Set the process to approximately normal conditions in
Manual mode.
2
Set TR first to minimum value (0.02 minutes/rep.) for several moments, then set it to the
extreme maximum (200 minutes/rep.) to lock in a fixed reset value.
3
Set P.B. to the widest value (1000%).
4
Set TD to the lowest value (0.01 minutes).
5
Switch to
Auto mode..
6
Slowly reduce the P.B. value from 1000% until process cycling starts.
7
Increase TD slowly from 0.01 minutes until process cycling stops.
8
Reduce P.B. until process cycling starts again.
9
Increase TD again until cycling stops.
10
Repeat steps 8 and 9 until no improvement can be made when TD is increased.
11
Increase P.B. to a safe margin approximately 1.5 times the value attained in steps 8
through 10.
12
Introduce automatic reset slowly by decreasing TR until cycling starts.
13
Back off TR to a safe margin of about 1.5 times the value attained in step 12.
53MC5000 Process Control Station
16-2