0 tuning pid parameters – Micromod Micro-DCI: 53MC5000 Multi-Loop Process Controller Instruction Manual User Manual
Page 298
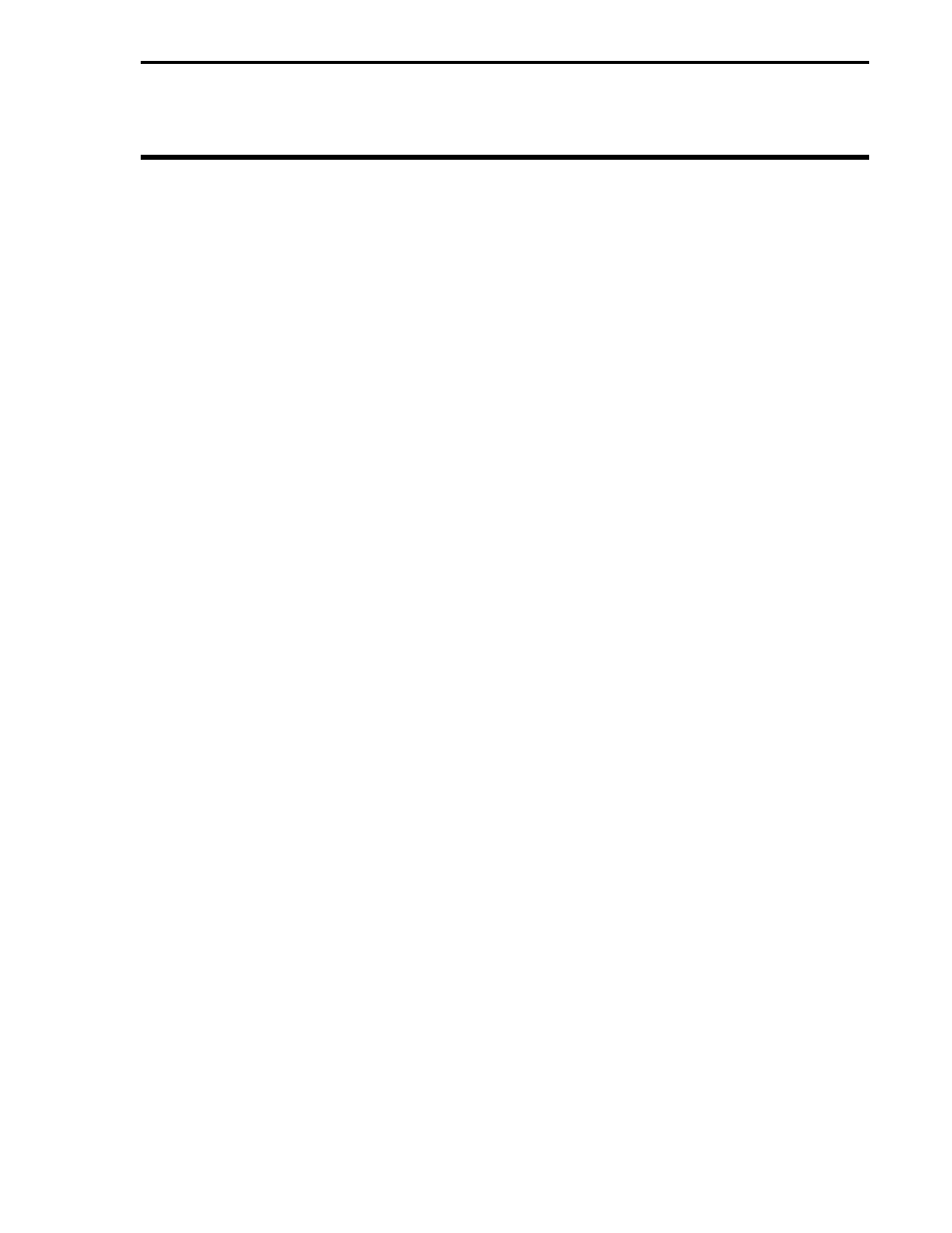
16.0 TUNING PID PARAMETERS
Tuning the controller is an iterative process to refine the Proportional Band (PB), Integral (also
called Reset Time [TR]), and Derivative (TD) parameters of each active Control Module (CON-0
through CON-3). The number of active CON Modules is determined by the Control Strategy se-
lected (e.g., CS1 - Single Loop PID Controller, would require tuning the PID parameters for only
CON-0; while CS41 - Four Loop Controller, would require tuning the PID parameters for all four
CON Modules). Values for these three datapoints in each CON module determine the proportional,
integral, and derivative action of that controller loop so that its output properly alters the final con-
trol element setting to correct the effects of a disturbance to the process or setpoint change.
16.1 PROPORTIONAL ACTION (PB)
In Proportional action there is a comparative relationship between the controller loop output signal
magnitude and the calculated error, which is the difference between the process variable and the
setpoint.
The proportional action of a controller is set as a percentage of the proportional band (% P.B.).
Percent proportional band is the full scale through which the error signal must vary to cause full
scale output variation due only to proportional control mode response. The proportionality factor
between the output signal and the error is called the gain.
Gain = 100 / % P.B.
If a small percent change in error is required to cause a full scale output variation from the final
control element (narrow proportional band), then the process system has a high gain. For exam-
ple, with the setpoint at 50% of scale and a percent proportional band at 20%, the process variable
feedback signal must vary from 40% to 60% of scale to make the final control element vary through
its full stroke. The gain would be 100 / 20 = 5. If a large percent change in error is required to
cause a full scale output variation from the final control element (wide proportional band), then the
controller is set for low gain. The datapoints to set the % P.B. parameters for CON0 through
CON3 are C106, C142, C178, and C214; they each have a default value of 100%. The minimum
value for proportional band is 2% (highest gain) and the maximum value is 1000% (lowest gain); 0
is off.
16.2 INTEGRAL ACTION (TR)
Integral action augments proportional action to cause a controller PID loop to drive its final control
element until the error is completely nulled. It produces a corrective signal proportional to the de-
viation and the length of time the controlled variable has not been at setpoint. Integral action is ex-
pressed as the length of time in minutes required for it to produce an output change equal in
magnitude to that produced by proportional action. The datapoints to set the Reset parameters for
CON0 through CON3 are C107, C143, C179, and C215; they each have a default value of 0 min-
utes (no integral action). The shortest repetition interval for integral action is 0.02 minutes/repeat
(maximum action) and the longest repetition interval is 200 minutes (minimum action). Each inte-
gral action datapoint (C107, C143, C179, or C215) must be 0 minutes if its respective CON Module
Manual Reset datapoint (C111, C147, C183, or C219) is used in lieu of integral action. The default
value for Manual Reset is 50%. The minimum value is 0% and the maximum value is 100%.
Section 16. Tuning PID Parameters
16-1