Rockwell Automation 1336E IMPACT Adjustable Frequency AC Drive User Manual V 1-4.XX User Manual
Page 308
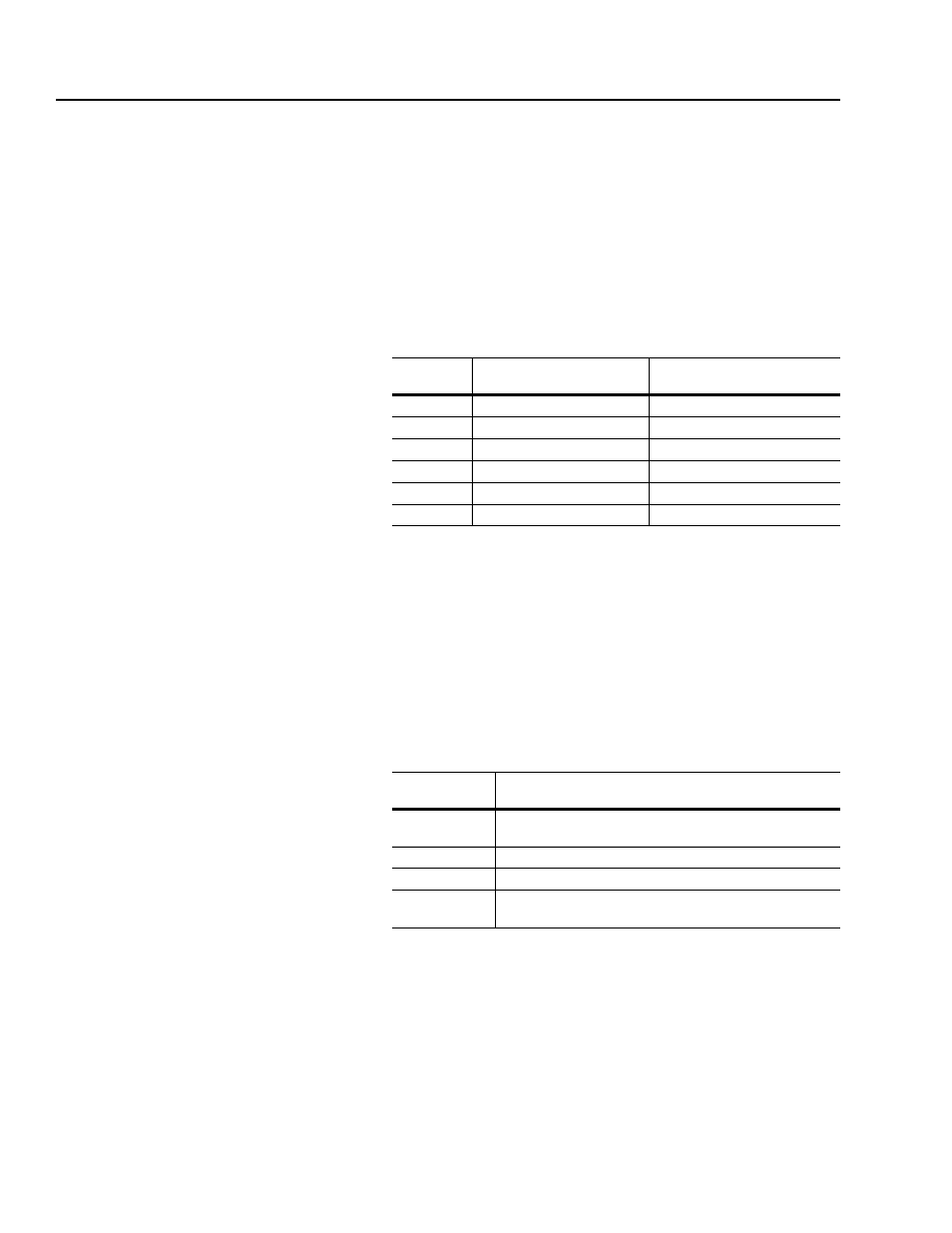
12-26
Troubleshooting
To fix a problem in this area, check for possible encoder faults.
Also check for possible encoder problems or excessive noise on
the encoder signals.
5. Enter a value of 10507 into Test Select 2.
6. Look at the value of Test Data 2. If Test Data 2 is zero, go to
step 7. If Test Data 2 is non-zero, there is a problem in the speed
regulator area. These conditions are unlikely to occur and
indicate an unusual combination of gains, references, and
feedback values. The drive attempts to regulate speed, however
operation in a current limited condition is likely. The following
table provides more specific information.
To fix a problem in this area, reduce the maximum level of speed
reference. Check if Total Inertia (parameter 157) and Spd Desired
BW (parameter 161) are appropriate for your system.
7. Enter a value of 10508 into Test Select 2.
8. Look at the value of Test Data 2. If Test Data 2 is zero, go to
step 9. If Test Data 2 is non-zero, there is a problem in the torque
reference area. These conditions indicate excessive levels of
torque reference. The 1336 IMPACT drive uses a maximum
internal torque reference of 800% and further limits this torque by
the drive’s torque and current limit settings.
To fix a problem in this area, determine if the torque reference
levels are excessive and possibly reduce the maximum level of
torque reference.
9. Enter a value of 10509 into Test Select 2.
If Test
Data 2 is:
Then:
Occurred
during:
1 (bit 0)
A subtract overflow
The integral error calculation.
2 (bit 1)
A multiply overflow
The integral gain calculation.
4 (bit 2)
An overflow
The bumpless calculation.
8 (bit 3)
A subtract overflow
The droop offset.
256 (bit 8)
A subtract overflow
The speed error calculation.
512 (bit 9)
A subtract overflow
The Kf error calculation.
If Test
Data 2 is:
Then:
1024 (bit 10)
An overflow occurred when Slave Torque % (parameter 70)
was applied to Torque Ref 1 (parameter 69).
4096 (bit 12)
An add overflow occurred for Torque Ref 1 + Torque Trim.
8192 (bit 13)
An add overflow occurred for the torque sum mode.
16384 (bit 14)
A divide overflow occurred for the torque to current
conversion (divide by flux).