Interface plc <˘> nc operating system – Lenze ETC Motion Control User Manual
Page 257
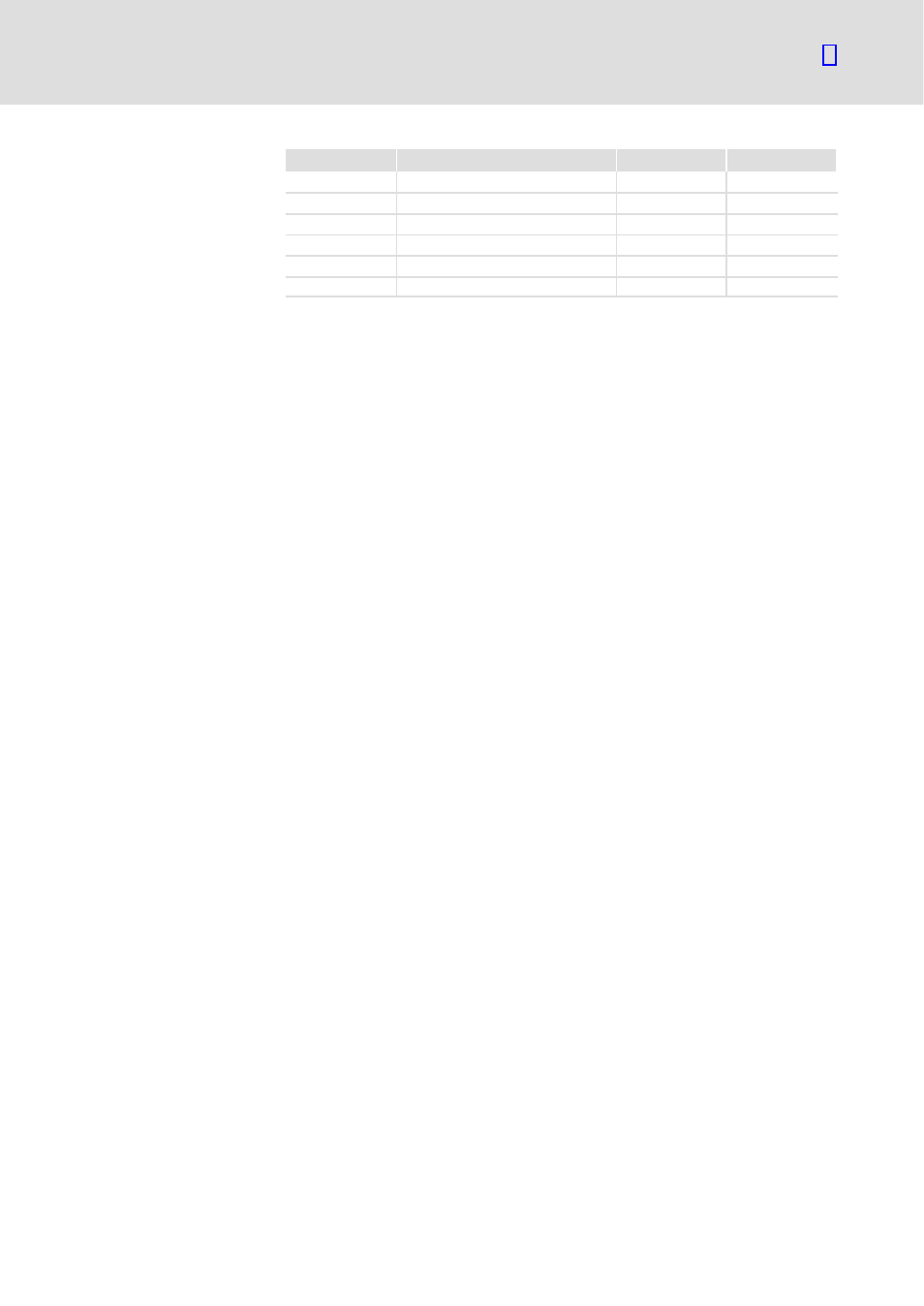
Interface PLC <˘> NC operating system
Definitions
Data block 1
5.1
5.1.2
l
257
EDSTCXN EN 2.0
Data word
Name
Direction
Type of signal
084.00−07
Traverse key axis 0
PLC
→
NC
static
084.08−15
Traverse key axis 1
PLC
→
NC
static
...
...
...
...
...
...
...
....
091.00−07
Traverse key axis 14
PLC
→
NC
static
091.08−15
Traverse key axis 15
PLC
→
NC
static
These signals are used for traversing the axes. One byte is available for each
axis. By writing the bytes, the respective action is executed. These traverse
keys are only active if traverse keys enable is not set.
Effect in the NC:
−100 ... +100: traversing with % of the maximum speed. The sign defines the
direction.
+/−101: inching by increments (corresponding to DB15 DW44 ... 47) on the
path if there is no feed enable. Only available for a programmed traversing
movement.
+/−102: home position approach (sign is ignored)
+/−103: setting zero point (sign is ignored)
+/−104: step travel (P673 increment)
+/−105: handwheel active − evaluation factor 1
+/−106: handwheel active − evaluation factor 3
+/−107: handwheel active − evaluation factor 10
+/−108: handwheel active − evaluation factor 30
+/−109: handwheel active − evaluation factor 100
+/−110: traverse command for PLC axis
+/−111: traversing with the speed from P208−223.
The sign specifies the direction.
Description of the traverse command for PLC axes: The PLC can move any
axis to a specific position that has been entered in the P field. The following
parameters are used for this purpose:
P176 ... 191 = target position specification by PLC for axes 0 ... 15 [mm] or [
°
]
P208 ... 223 = speed specification by PLC for axes 0 ... 15 [mm/min] or [rpm]
P240 ... 255 = speed specification by PLC for axes 0 ... 15 [m/sec
2]
or [rps
2
]
The following parameters are available for display:
P144 ... 159 = accepted target position after positive edge of the traverse key
[mm] or [
°
]
P160 ... 175 = current modal actual position [mm] or [
°
]
A target point approach of an axis starts when the value +/−110 is specified
in its traverse key. Make sure in the process that the NC computer detects the
change of the traverse key (if required, observe handshake; see diagram).