5 configuration of axes - basics, 1 mk_candrives, Configuration of axes − basics – Lenze ETC Motion Control User Manual
Page 204: Mk_candrives, Machine constants
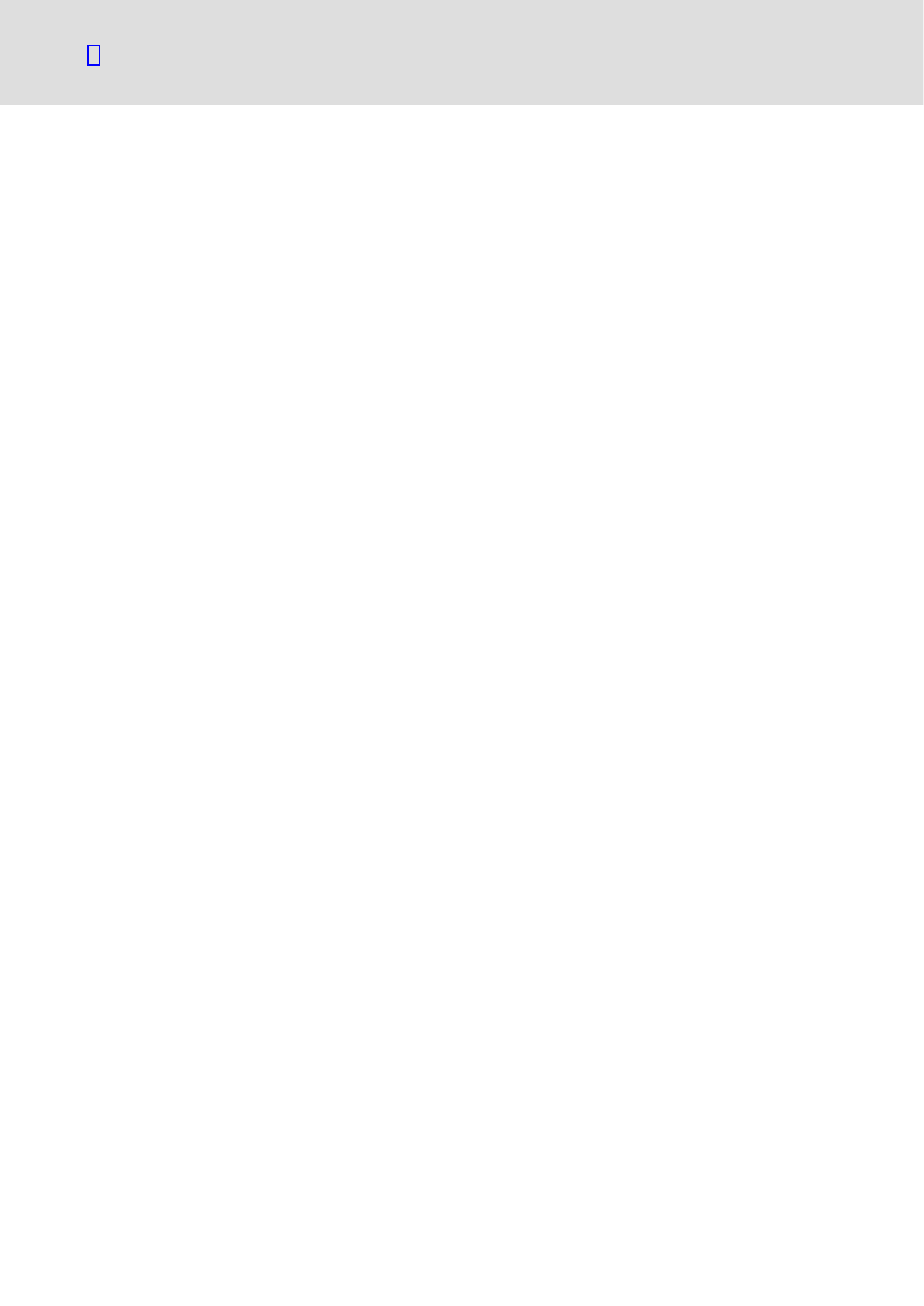
Machine constants
Configuration of axes − Basics
MK_CANDRIVES
4.5
4.5.1
l
204
EDSTCXN EN 2.0
4.5
Configuration of axes − Basics
These are the most important settings that have to be implemented as they
are used to adapt the control to the mechanics.
As the control can be used for the many different axis combinations, the
following must be specified by means of the machine constants:
ƒ which type of axes exist on this specific machine,
ƒ with which identification letter the axes are to be addressed,
ƒ to which (hardware) axis computer channel the corresponding
(software) axis is connected.
In the control, the axes are consecutively numbered from 0 ... N−1, while N is
the maximum number of configurable application (=software) axes. This
number is control−specific and does not have to correspond to the maximum
number of the physical (=hardware) axes. At the end of this chapter, you can
find a table in which the maximum number of axes is listed for the individual
control types.
After it has been established which physical axes exist on the machine, the
application axes must be assigned to the physical axes.
4.5.1
MK_CANDRIVES
MK_CANDRIVES defines the axes that are connected to the second CAN bus.
Enter a valid (0 ... N−1) application axis number or the value −1 in each
parameter of this MC with N as the maximum number of application axes.
If two physical axes are assigned to one application axis, which means that
one application axis number appears twice in one of these MCs, this is called
a synchronous axis. This is the only case, when the number of configured
physical axes differs from the number of configured application axes.
After it has been established which application axes exist, letters must be
assigned to these axes. The axes in the DIN program can only be
programmed via the axis letters.