5 mk_polar_achsnr, 6 mk_wlk_c_grenzwinkel, 7 mk_wlk_c_offset – Lenze ETC Motion Control User Manual
Page 223: Mk_polar_achsnr, Mk_wlk_c_grenzwinkel, Mk_wlk_c_offset, Machine constants
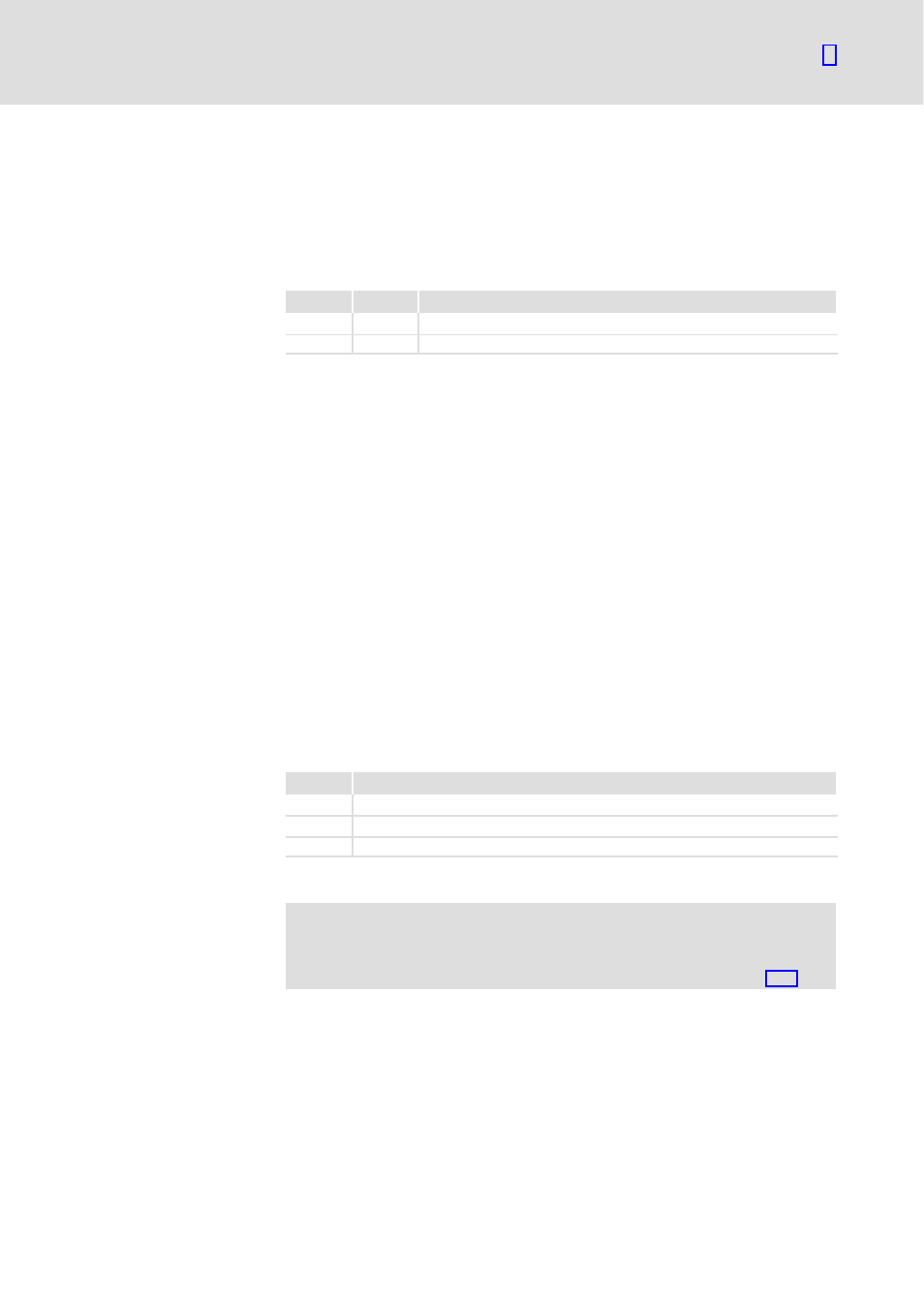
Machine constants
Technology−specific settings
MK_POLAR_ACHSNR
4.15
4.15.5
l
223
EDSTCXN EN 2.0
4.15.5
MK_POLAR_ACHSNR
This machine constant defines the numbers of the radius and the angle axis
in the polar machine coordinate system. They are the physical axes for radius
and angle on the machine.
This MC has the following 2 entries:
Index
Default
Meaning
0
0
Number of radius axis
1
1
Number of angle axis
As these should be the same axis numbers as the first two axes in
MK_KARTESISCH_ACHSNR, the remaining configuration is the same. The
only difference is that in MK_WEG, degrees must be used as the unit for the
angle axis as it is a real rotation axis.
4.15.6
MK_WLK_C_GRENZWINKEL
This machine constant is used by different correction modules (e.g.
"SCHNEIDEN" ["CUT"]) for the tangential correction of the C axis and defines
up to which relative angle an abrupt positioning of this axis may take place.
If the angles are greater than this MC, the feed on the path is stopped, the C
axis is fed individually with G0 and then the path is interpolated further.
Depending on the correction module, an M15 is inserted before the G0 and
an M14 behind the G0 in order to carry out the positioning with the tool
raised.
In the case of smaller angles the positioning of the C axis to the new profile
angle takes place at the block transition in one step without affecting the
path interpolation.
Value
Meaning
45
abrupt positioning up to 45
°
(default)
15
abrupt positioning up to 15
°
90
abrupt positioning up to 90
°
Any angle between 0 and 180
°
can be set.
)
Note!
Which correction module is switched on for G41/G42 depends
on the technology used and the value in MK_KUNDE (
¶ 193).
4.15.7
MK_WLK_C_OFFSET
This machine constant is used in the correction module "Schneiden" ("Cut")
for compensating the technology−specific pitch of the tool. The MC specifies
the offset in degrees by which the C axis is to be shifted in relation to the
calculated path orientation. The default value of 0 does not cause a shift.