5 interface plc <-> nc operating system, 1 definitions, Interface plc <−> nc operating system – Lenze ETC Motion Control User Manual
Page 240: Definitions
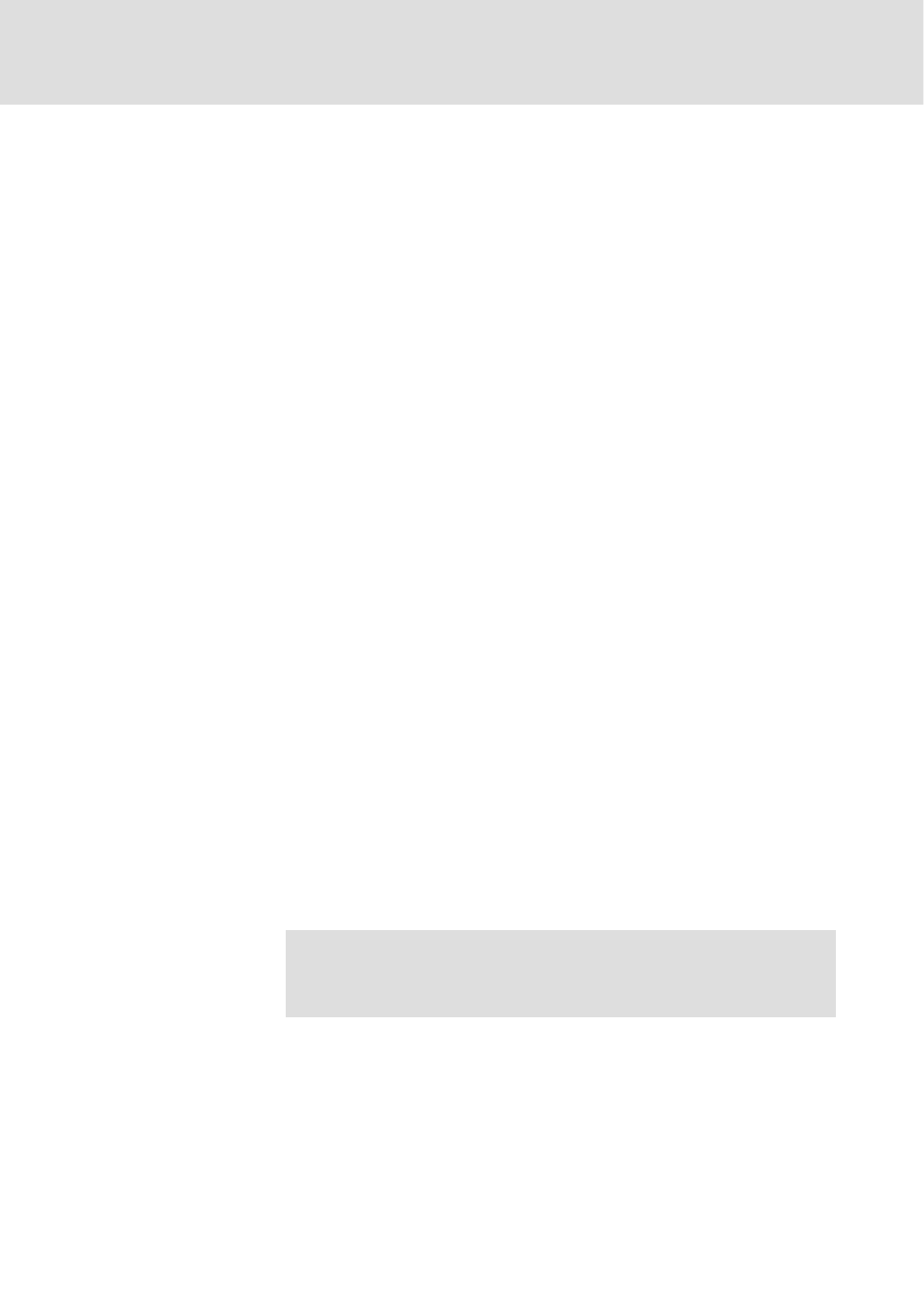
Interface PLC <˘> NC operating system
Definitions
5
5.1
l
240
EDSTCXN EN 2.0
5
Interface PLC <−> NC operating system
The integrated PLC is a component of the hardware and software of the ETC
control. It is programmed like a conventional PLC and generally has the same
features. For the communication with the actual CNC control (NC), a formal
interface is provided within the CNC, whose function follows the regulations
according to IEC 550, ISO 4336 and VDI 3422.
In this chapter, the function of the interface is described. The individual
signals are defined and their function mode described.
It is not necessary to describe the signal types and the timing of the signals,
because the interface is created solely by internal memories and is thus sub-
ject to the same regulations as the data exchange within the CNC. Signal pro-
pagation delays must not be taken into account.
5.1
Definitions
The data exchange between NC computer and integrated PLC takes place via
an internal RAM area, which is defined as "Data words" for the PLC. The
transfer takes place in data blocks "DB0", "DB1", "DB2" and "DB8 ... DB15".
DB0: Contains the interface to the ETC_MMI.
DB1: Contains all standard signals (NC <−> PLC) as well as an area from the
"virtual keyboard".
DB2: Interface between PLC and MMI.
DB8 ... DB15: This is where the interface data between the NC computer and
the MMI is stored.
This interface corresponds to the Dual−Port RAM interface,
which is used as a connection to the MMI.
Every data block consists of 256 data words (DW) of 16 bit each. One block
contains static signals as well as messages (data) that are exchanged with
acknowledge characters ("handshake"). The data areas are bidirectional, i.e.
the data from the PLC to the NC as well as the data from the NC to the PLC
is included.
)
Note!
In CoDeSys, the signals/data of the data blocks are available as
what is called system variables.
The data exchange between NC and SPS takes place cyclically during each cy-
cle of the PLC program. The data which is transferred from the NC to the PLC,
is copied before a PLC cycle starts, the data from the PLC to the NC, after a cy-
cle.
Static signals are set without prior evaluation. Data whose evaluation must
be ensured is transmitted as a message and has two additional signals for a
handshake: "Strobe" and "Acknowledgement".