Cnc programming – Lenze ETC Motion Control User Manual
Page 167
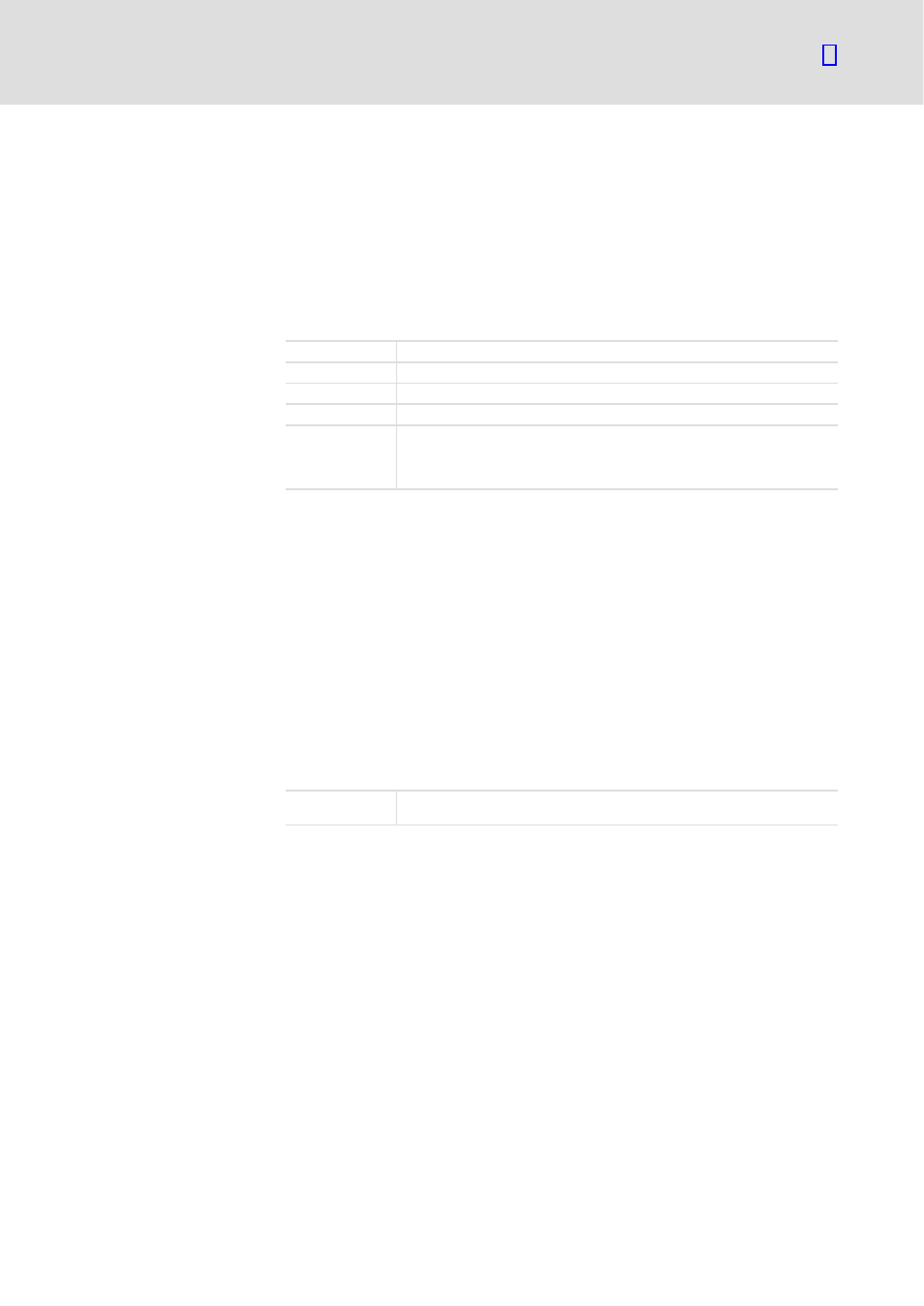
CNC programming
G functions
G functions individual descriptions
3.2
3.2.2
l
167
EDSTCXN EN 2.0
3.2.2.79
G251 Accept step response of an axis
G251 is used to set the drive and attitude control parameters of an axis
through the acceptance of a step response and can only be used by a special
axis setting tool like the AXSCOPE. Generally, this function is not important
for DIN programmers.
G251 AXES I J K L
AXES
Speed stroke of the axis to be set in [mm/min] or [1/min]
I
Jump duration in seconds
J
Acceleration duration in seconds
K
Number of jumps
L
Identification
0: recording of the master axis (default)
1: recording of the slave axis
2: recording of master and slave axis
The function oscillates the specified axis K−times with the specified speed,
the accelerating duration J and the jump duration I to and fro. At the end of
the movement the axis is positioned at its starting point again. The traverse
path corresponds to I * speed. The pause between the jumps is I − J. If K is not
specified, the axis oscillates to and fro 1−time.
During the output of the jump function on the axis, theoretical speed, actual
speed, following error and correcting variable are recorded as a 16−bit
integer data type and transmitted asynchronously to the PC. This can display
the recorded information as a graph or evaluate it elsewhere.
If the identification L2 is specified for a synchronous axis, the control records
the actual speed of the master axis, the slave axis, the synchronous distance
between the two axes and the theoretical speed.
G251 X1000 I0.2
J0.1
Output of a setpoint step−change with a speed stroke of 1 m/min, a jump
duration of 200 ms and an accelerating duration of 100 ms.
Syntax
Meaning of the addresses
Explanation
Example