6 application macros, 7 motor temperature – Siemens 440 User Manual
Page 69
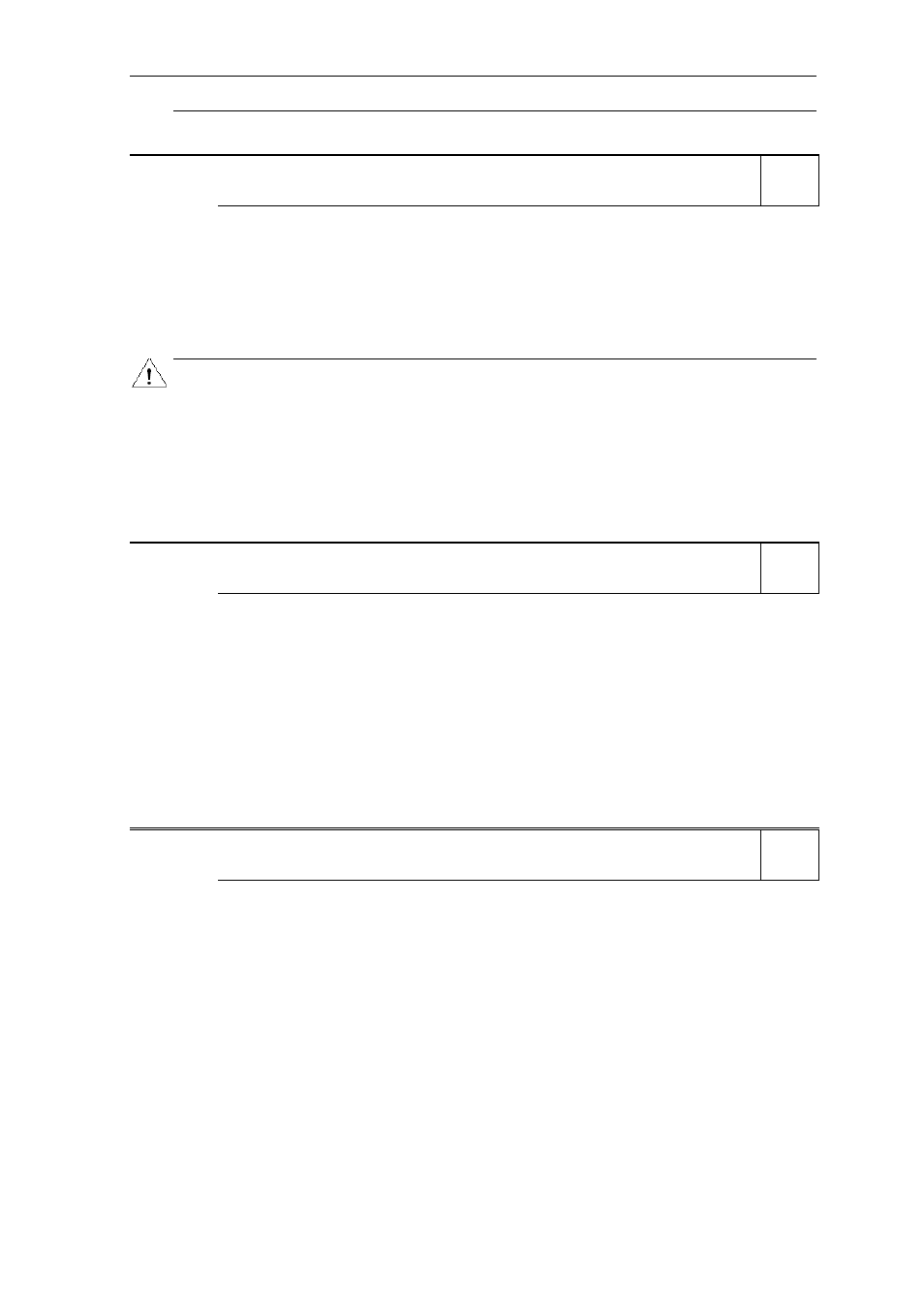
Issue 01/06
Parameter Description
MICROMASTER 440 Parameter List
6SE6400-5BB00-0BP0
69
Note:
The value of P0492 should be approx. 2x rated slip, if the motor power is less (<=) 90 kW
The value of P0492 should be approx. 4x rated slip, if the motor power is greater (>) 90 kW
P0494[3]
Delay frequency loss reaction
Min: 0
CStat:
CUT
Datatype: U16 Unit:
ms
Def:
10
P-Group: ENCODER
Active: first confirm
QuickComm.: No
Max: 65000
Used for low frequency encoder loss detection. If the motor shaft frequency is less than the value in P0492
then encoder loss is detected using a low frequency encoder loss detection algorithm. This parameter
selects the delay between loss of encoder at low frequency and reaction to the encoder loss.
Index:
P0494[0] : 1st. Drive data set (DDS)
P0494[1] : 2nd. Drive data set (DDS)
P0494[2] : 3rd. Drive data set (DDS)
Dependency:
This parameter is updated when motor start-up time P0345 is changed or when a frequency-loop
optimisation is performed (P1960 = 1).
Caution:
P0494 = 0 (disabled):
When the delay in P0494 is set to 0, then low frequency encoder loss detection is disabled and low
frequency encoder loss cannot be detected (high frequency encoder loss detection will still operate if P0492
> 0).
If low frequency encoder loss detection is disabled and encoder should be lost at low frequency, then
operation of motor may become unstable.
3.6 Application
macros
P0500[3] Technological
application
Min: 0
CStat:
CT
Datatype: U16 Unit:
-
Def:
0
P-Group: TECH_APL
Active: first confirm
QuickComm.: Yes Max: 3
Selects technological application. Sets control mode (P1300).
Possible Settings:
0 Constant
torque
1
Pumps and fans
3 Simple
Positioning
Index:
P0500[0] : 1st. Drive data set (DDS)
P0500[1] : 2nd. Drive data set (DDS)
P0500[2] : 3rd. Drive data set (DDS)
Dependency:
See parameter P0205
3.7 Motor
temperature
P0601[3]
Motor temperature sensor
Min: 0
CStat:
CUT
Datatype: U16 Unit:
-
Def:
0
P-Group: MOTOR
Active: first confirm
QuickComm.: No
Max: 2
Selects motor temperature sensor.
Possible Settings:
0 No
sensor
1 PTC
thermistor
2 KTY84
Index:
P0601[0] : 1st. Drive data set (DDS)
P0601[1] : 2nd. Drive data set (DDS)
P0601[2] : 3rd. Drive data set (DDS)
Dependency:
If "no sensor" is selected, the motor temperature monitoring will be done based on the estimated value of
the thermal motor model.
The temperature of the motor, when a thermal sensor is connected is calculated using the thermal motor
model. When a KTY sensor is fitted, the loss of connection can be detected (Alarm F0015). Using the
methods described above the monitoring of the temperature will automatically switch to the thermal model
using values derived from the estimated value. Using a PTC sensor the temperature of the motor is
calculated by the sensor in conjunction with the thermal model. This allows for redundancy of the monitoring
process.
Level
2
Level
3
Level
2