Parameter description issue 01/06 – Siemens 440 User Manual
Page 154
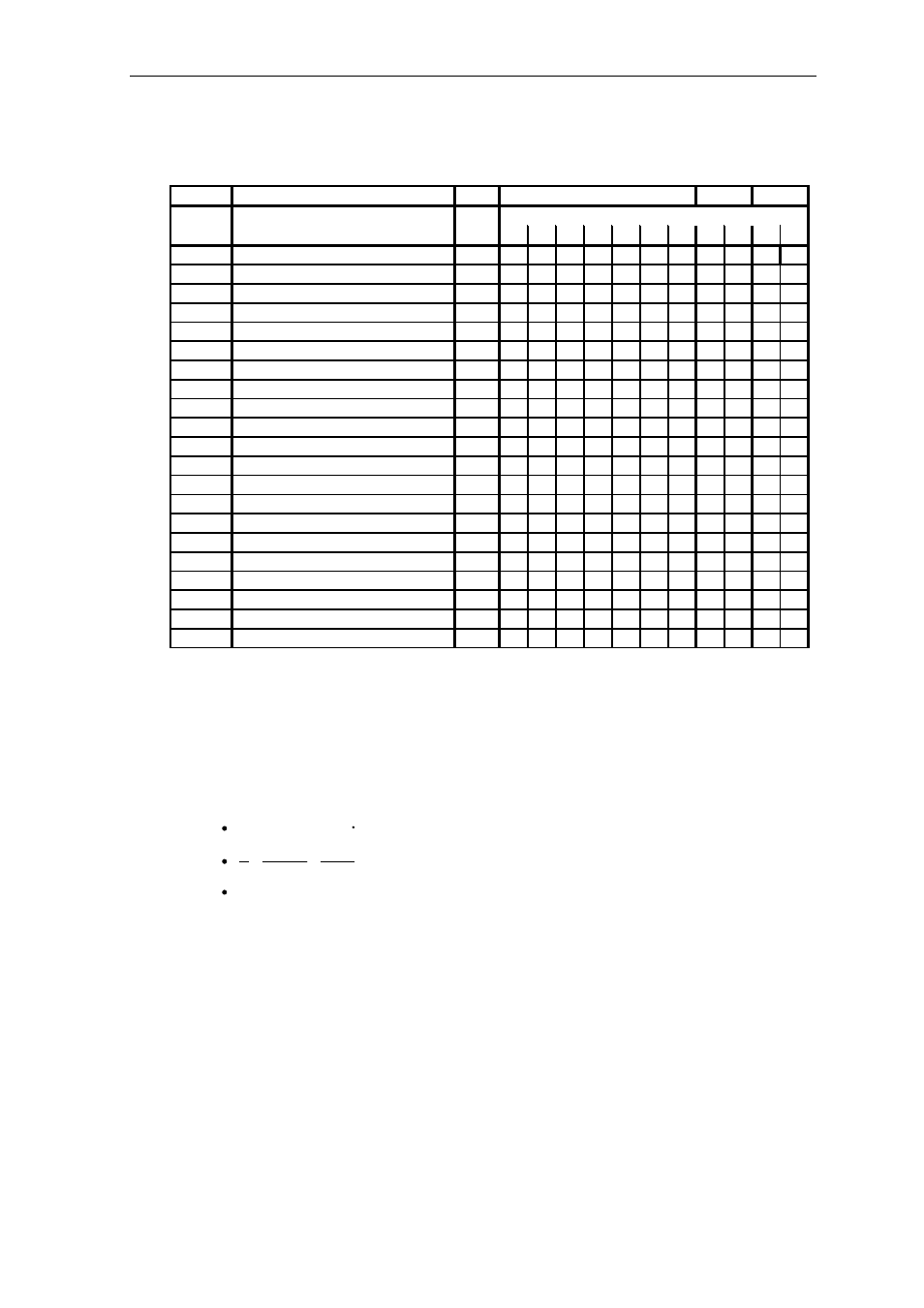
Parameter Description
Issue 01/06
MICROMASTER 440 Parameter List
154
6SE6400-5BB00-0BP0
P1300 = 19 : V/f control with independent voltage setpoint
The following table presents an overview of control parameters (V/f) that can be modify in relationship to
P1300 dependencies:
ParNo.
Level
0
1
2
3
5
6
19
20
22
21
23
P1300[3]
2
x
x
x
x
x
x
x
x
x
x
x
P1310[3]
2
x
x
x
x
x
x
x
−
−
−
−
P1311[3]
2
x
x
x
x
x
x
x
−
−
−
−
P1312[3]
2
x
x
x
x
x
x
x
−
−
−
−
P1316[3]
3
x
x
x
x
x
x
x
−
−
−
−
P1320[3]
3
−
−
−
x
−
−
−
−
−
−
−
P1321[3]
3
−
−
−
x
−
−
−
−
−
−
−
P1322[3]
3
−
−
−
x
−
−
−
−
−
−
−
P1323[3]
3
−
−
−
x
−
−
−
−
−
−
−
P1324[3]
3
−
−
−
x
−
−
−
−
−
−
−
P1325[3]
3
−
−
−
x
−
−
−
−
−
−
−
P1330[3]
3
−
−
−
−
−
−
x
−
−
−
−
P1333[3]
3
−
x
−
−
−
x
−
−
−
−
−
P1335[3]
2
x
x
x
x
−
−
−
−
−
−
−
P1336[3]
2
x
x
x
x
−
−
−
−
−
−
−
P1338[3]
3
x
x
x
x
−
−
−
−
−
−
−
P1340[3]
3
x
x
x
x
x
x
x
−
−
−
−
P1341[3]
3
x
x
x
x
x
x
x
−
−
−
−
P1345[3]
3
x
x
x
x
x
x
x
−
−
−
−
P1346[3]
3
x
x
x
x
x
x
x
−
−
−
−
P1350[3]
3
x
x
x
x
x
x
x
−
−
−
−
U/f
SLVC
VC
P1300 =
Parameter name
Control mode
Continuous boost
Acceleration boost
Starting boost
Boost end frequency
Programmable V/f freq. coord. 1
Programmable V/f volt. coord. 1
Programmable V/f freq. coord. 2
Programmable V/f volt. coord. 2
Programmable V/f freq. coord. 3
CI: Voltage setpoint
Start frequency for FCC
Slip compensation
CO: U/f Slip limit
Resonance damping gain V/f
Imax freq. controller prop. gain
Imax controller integral time
Imax controller prop. gain
Imax voltage ctrl. integral time
Voltage soft start
Programmable V/f volt. coord. 3
V/f
SLVC / VC can provide excellent performance for the following types of application:
-
Applications which require high torque performance
-
Applications which require fast respond to shock loading
-
Applications which require torque holding while passing through 0 Hz
-
Applications which require very accurate speed holding
-
Applications which require motor pull out protection
SLVC/VC-Restrictions:
-
SLVC / VC is dependent on the accuracy of the motor model being used and the measurements being
performed by the inverter. There are therefore certain restrictions on the use of SLVC / VC:
(max. frequency)
f
max
= min(200 Hz, 5 P0310)
r0207
r0209
r0207
P0305
4
1
≤
≤
(ratio of rated motor current to rated inverter current)
no synchronuos motor
Recommended means of SLVC/VC-commissioning:
-
For correct operation under SLVC / VC control it is imperative that the name plate data of the motor
(P0304 - P0310) is correctly entered and that the motor data identification (P1910) must be carried out
on a cold motor. It is also necessary to ensure that the motor ambient temperature is correctly entered
in P0625 if this is significantly different from the default value of 20°C. This must be done after the quick
commissioning has been completed (P3900) but before the motor data identification measurements are
carried out.
-
See parameter P0400 and documentation of encoder and encoder module when commissioning VC
(P1300 = 21 or 23).
SLVC/VC-Optimisation:
The following parameters can be adjusted by the user to improve performance.
-
P0003 = 3
-
P0342: Total / motor inertia ratio
Sensorless Vector Control (SLVC):
-
P1470: P gain (SLVC)
-
P1472: I term (SLVC)
-
P1610: Continuous torque boost (SLVC, open loop boost)
-
P1611: Acceleration torque boost (SLVC, open loop boost)
-
P1750: Control word of motor model
-
P1755: Start-frequency motor model (SLVC)